When selecting aluminum for CNC machining, aerospace, automotive, or structural applications, the choice between 7075 aluminum and 6082 aluminum is critical. Both alloys offer unique benefits, but which one is better suited for your needs?
7075 aluminum is renowned for its high strength and durability, making it a top choice for aerospace and high-performance applications. Meanwhile, 6082 aluminum is valued for its corrosion resistance, weldability, and structural strength, making it a preferred material for marine, automotive, and industrial applications.
Understanding the key differences between 7075 and 6082 aluminum will help you make an informed decision for CNC machining, prototyping, and industrial use.
What is 7075 Aluminum (AL 7075)?
7075 aluminum is a high-strength, heat-treatable aluminum alloy that belongs to the 7xxx series, known for its exceptional mechanical properties and hardness. It contains zinc as the primary alloying element, along with small amounts of magnesium, copper, and chromium.
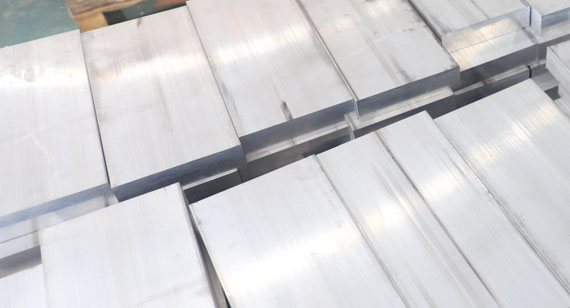
Key Characteristics of 7075 Aluminum
- Extremely high strength-to-weight ratio (stronger than many steels).
- High tensile strength (~500 MPa in T6 temper).
- Excellent fatigue resistance for high-stress applications.
- Poor weldability and lower corrosion resistance compared to 6xxx series aluminum.
- Widely used in aerospace, defense, and high-performance sports equipment.
Best suited for CNC machining applications that require maximum strength and wear resistance.
What is 6082 Aluminum (AL 6082)?
6082 aluminum is a medium-strength, corrosion-resistant aluminum alloy from the 6xxx series, with silicon and magnesium as its primary alloying elements. It is known for its excellent machinability, weldability, and structural integrity.
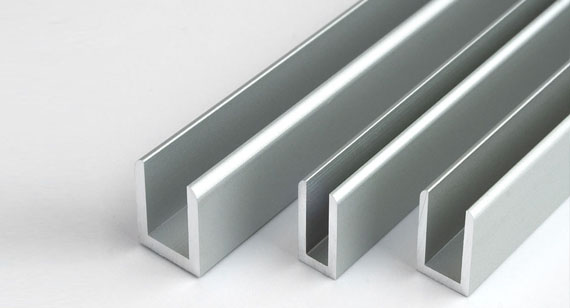
Key Characteristics of 6082 Aluminum
- Good strength-to-weight ratio (lower than 7075 but still high).
- High corrosion resistance, making it ideal for marine and outdoor applications.
- Superior weldability and formability compared to 7075 aluminum.
- Commonly used in structural engineering, bridges, transportation, and marine components.
Ideal for applications requiring strength, corrosion resistance, and ease of fabrication.
What is the Difference Between 7075 and 6082 Aluminum?
Al7075 and Al6082 Chemical Composition Table
Element |
7075 Aluminum (%) |
6082 Aluminum (%) |
Aluminum (Al) |
Balance |
Balance |
Zinc (Zn) |
5.1 – 6.1 |
0.0 |
Magnesium (Mg) |
2.1 – 2.9 |
0.6 – 1.2 |
Silicon (Si) |
0.0 – 0.4 |
0.7 – 1.3 |
Copper (Cu) |
1.2 – 2.0 |
0.0 – 0.1 |
Manganese (Mn) |
0.3 |
0.4 – 1.0 |
Chromium (Cr) |
0.18 – 0.28 |
0.0 – 0.25 |
Iron (Fe) |
0.5 max |
0.0 – 0.5 |
Key Takeaways:
- 7075 aluminum contains a high percentage of zinc and copper, making it stronger but less corrosion-resistant.
- 6082 aluminum has higher silicon and magnesium content, enhancing corrosion resistance and weldability.
Al7075 and Al6082 Aluminum Alloy Family: Understanding Their Classification and Uses
Both 7075 aluminum (Al7075) and 6082 aluminum (Al6082) belong to different aluminum alloy families, each with unique characteristics and applications. These alloys are classified based on their composition, properties, and intended use, making them suitable for specific machining and manufacturing processes.
- Al7075 belongs to the 7xxx series, known for high strength, aerospace applications, and hardness.
- Al6082 is part of the 6xxx series, recognized for corrosion resistance, weldability, and structural applications.
Understanding how these aluminum families differ will help you determine the best choice for CNC machining, aerospace, automotive, and industrial applications.
1. What is the Aluminum Alloy Series Classification?
Aluminum alloys are categorized into wrought and cast alloys, divided into series based on their major alloying elements. The 6xxx and 7xxx series are two of the most commonly used in CNC machining and industrial applications.
Aluminum Alloy Series Overview
Alloy Series |
Primary Alloying Element |
Properties |
Example Alloys |
1xxx |
Pure Aluminum (99%+) |
High corrosion resistance, excellent thermal and electrical conductivity |
1050, 1100, 1350 |
2xxx |
Copper |
High strength, aerospace applications, lower corrosion resistance |
2024, 2219 |
3xxx |
Manganese |
Excellent corrosion resistance, moderate strength |
3003, 3105 |
4xxx |
Silicon |
Wear resistance, high-temperature performance |
4032, 4045 |
5xxx |
Magnesium |
Marine applications, excellent corrosion resistance |
5052, 5083, 5754 |
6xxx |
Magnesium & Silicon |
Medium-to-high strength, corrosion resistance, weldable |
6061, 6082, 6106 |
7xxx |
Zinc |
Ultra-high strength, aerospace applications, lower corrosion resistance |
7075, 7050, 7475 |
- Al6082 belongs to the 6xxx series (medium strength, good corrosion resistance).
- Al7075 belongs to the 7xxx series (high strength, aerospace-grade properties).
2. Understanding the 6xxx Series (Al6082 Family)
What is the 6xxx Series?
The 6xxx series aluminum alloys are medium-strength, heat-treatable alloys that combine magnesium and silicon as their primary alloying elements. These alloys are widely used in structural applications, transportation, and marine industries due to their excellent corrosion resistance and weldability.
Key Properties of the 6xxx Series
- Medium-to-high strength – Stronger than 5xxx series but lower than 7xxx series.
- Good corrosion resistance – Suitable for marine and outdoor applications.
- Excellent weldability – Preferred for fabricated structures and construction.
- Good machinability – Can be CNC machined but requires proper cutting tools and lubrication.
Common 6xxx Series Alloys
- 6061 Aluminum – Most commonly used, excellent balance of strength and corrosion resistance.
- 6082 Aluminum – Stronger than 6061, better corrosion resistance, used in structural applications.
- 6106 Aluminum – Good weldability, often used in architectural structures.
6082 is one of the strongest 6xxx series alloys, making it ideal for CNC machining and industrial applications.
3. Understanding the 7xxx Series (Al7075 Family)
What is the 7xxx Series?
The 7xxx series aluminum alloys are high-strength, aerospace-grade alloys that use zinc as the primary alloying element, with additional magnesium, copper, and chromium for enhanced properties. These alloys are stronger than steel in some cases, making them the top choice for aerospace, defense, and high-performance sports applications.
Key Properties of the 7xxx Series
- Extremely high strength – Among the strongest aluminum alloys available.
- Good fatigue resistance – Ideal for aircraft and structural applications.
- Lower corrosion resistance – Needs anodizing or protective coatings.
- Poor weldability – More difficult to weld due to the risk of cracking.
- Excellent machinability – Preferred for precision CNC machining.
Common 7xxx Series Alloys
- 7075 Aluminum – Aerospace-grade, highest strength, widely used in military and aviation.
- 7050 Aluminum – Similar to 7075 but with better corrosion resistance.
- 7475 Aluminum – Used in aircraft fuselage and wings for high durability.
7075 is the go-to aluminum for applications demanding extreme strength and wear resistance.
4. Key Differences Between 6082 and 7075 Aluminum Families
Property
|
6082 (6xxx Series)
|
7075 (7xxx Series)
|
Primary Alloying Elements |
Magnesium, Silicon |
Zinc, Magnesium, Copper |
Strength |
Medium to High |
Very High |
Tensile Strength |
~330 MPa |
~500 MPa |
Yield Strength |
~280 MPa |
~430 MPa |
Corrosion Resistance |
High |
Low (unless treated) |
Weldability |
Excellent |
Poor |
Machinability |
Good |
Excellent |
Common Uses |
Structural applications, bridges, marine, automotive |
Aerospace, defense, high-performance sports equipment |
- Al6082 is preferred for corrosion-resistant and structural applications.
- Al7075 is used when strength and durability are the top priorities.
5. Which Aluminum Alloy Family is Best for Your Project?
Use 6082 Aluminum If:
- You need corrosion resistance and weldability.
- You require good strength without extreme hardness.
- You are working on marine, automotive, or structural applications.
Use 7075 Aluminum If:
- You need maximum strength and fatigue resistance.
- You are manufacturing aerospace or military components.
- You require high-performance CNC machining parts with superior hardness.
For CNC machining services, 7075 aluminum is better for high-strength applications, while 6082 is better for corrosion resistance and weldability.
Conclusion: Which Aluminum Alloy Family Should You Choose?
- 6082 aluminum (6xxx series) is a versatile, corrosion-resistant aluminum alloy widely used in marine, construction, and automotive applications. It is highly weldable and affordable, making it ideal for CNC machining projects that require strength and durability.
- 7075 aluminum (7xxx series) is an ultra-high-strength aluminum alloy used in aerospace, defense, and high-performance applications. It is stronger than many steels but requires protective coatings due to its lower corrosion resistance.
For CNC machining and prototype manufacturing, both aluminum alloys are valuable, but the choice depends on the application’s strength, corrosion resistance, and fabrication requirements.
Looking for precision CNC machining in 6082 or 7075 aluminum? Contact us for custom CNC machining services, CNC prototype machining, and expert material selection!
7075 vs. 6082 Aluminum: A Comprehensive Comparison of Properties
When selecting an aluminum alloy for CNC machining, aerospace, automotive, or industrial applications, 7075 and 6082 aluminum are two of the most commonly used options. 7075 aluminum is known for its high strength and hardness, making it ideal for aerospace and military applications. 6082 aluminum, on the other hand, is corrosion-resistant, weldable, and widely used in structural and marine applications.
Understanding the differences in density, strength, corrosion resistance, machinability, and cost can help you choose the best alloy for CNC machining, custom fabrication, and industrial manufacturing.
Density of 7075 vs. 6082 Aluminum
- 7075 Aluminum Density: 2.81 g/cm³
- 6082 Aluminum Density: 2.70 g/cm³
Key Takeaway
- 6082 aluminum is slightly lighter than 7075 aluminum, but the difference is minor.
- For applications where weight savings are critical, 6082 aluminum may provide a slight advantage.
Both alloys are lightweight compared to steel, making them ideal for aerospace and automotive use.
Strength Comparison: 7075 vs. 6082 Aluminum
Strength is one of the biggest factors when choosing between 7075 and 6082 aluminum.
- 7075 aluminum is among the strongest aluminum alloys available.
- 6082 aluminum is a high-strength structural alloy, but it is not as strong as 7075.
Tensile Strength of 7075 vs. 6082 Aluminum
- 7075-T6 Aluminum Tensile Strength: 500–580 MPa
- 6082-T6 Aluminum Tensile Strength: 300–340 MPa
Key Takeaway
- 7075 aluminum is nearly twice as strong as 6082 aluminum, making it better for high-stress applications like aerospace, military, and automotive racing.
- 6082 aluminum is strong enough for most structural applications but may not be suitable for extremely high-load conditions.
For applications requiring maximum tensile strength, 7075 aluminum is the superior choice.
Yield Strength of 7075 vs. 6082 Aluminum
- 7075-T6 Aluminum Yield Strength: 430–500 MPa
- 6082-T6 Aluminum Yield Strength: 260–300 MPa
Key Takeaway
- 7075 aluminum has a much higher yield strength than 6082 aluminum, meaning it can withstand higher loads before permanently deforming.
- 6082 aluminum is more ductile, allowing for easier forming and bending before failure.
If you need a material that resists deformation under heavy loads, 7075 aluminum is the best choice.
Corrosion Resistance: 7075 vs. 6082 Aluminum
- 6082 aluminum has excellent corrosion resistance, making it ideal for marine, outdoor, and humid environments.
- 7075 aluminum has lower corrosion resistance, meaning it requires anodizing or protective coatings to prevent oxidation.
Key Takeaway
- For applications exposed to moisture, saltwater, or harsh environments, 6082 aluminum is the better option.
- 7075 aluminum should be used in dry environments or coated to enhance its corrosion resistance.
For outdoor and marine applications, 6082 aluminum is the preferred choice due to its superior corrosion resistance.
Weldability of 7075 vs. 6082 Aluminum
- 6082 aluminum is highly weldable, making it easy to fabricate and assemble using TIG and MIG welding.
- 7075 aluminum is difficult to weld, as it is prone to hot cracking and requires special welding techniques.
Key Takeaway
- If your project requires welding, 6082 aluminum is the best choice.
- 7075 aluminum is rarely welded and is instead joined using fasteners or adhesives.
For CNC machining projects that require welding, 6082 aluminum is the clear winner.
Machinability: 7075 vs. 6082 Aluminum
- 7075 aluminum is easier to machine than 6082 aluminum due to its hardness and reduced stickiness.
- 6082 aluminum requires cutting fluids and sharp tools to avoid tool wear and material buildup.
Key Takeaway
- For CNC machining, 7075 aluminum is easier to work with and provides better surface finishes.
- 6082 aluminum is machinable but may require special tool coatings and slower cutting speeds.
If machinability is a priority, 7075 aluminum is the better option.
Cost Comparison: 7075 vs. 6082 Aluminum
- 7075 aluminum is more expensive due to its higher strength and aerospace-grade properties.
- 6082 aluminum is more affordable, making it the better option for budget-sensitive projects.
Estimated Material Costs (Per kg)
- 7075 Aluminum Cost: $6 – $10 per kg
- 6082 Aluminum Cost: $4 – $7 per kg
Key Takeaway
- If cost is a concern, 6082 aluminum is the more economical choice.
- If high strength is necessary, 7075 aluminum is worth the additional cost.
For budget-friendly projects, 6082 aluminum offers great value without sacrificing too much strength.
Common Applications of 7075 vs. 6082 Aluminum
Application
|
7075 Aluminum
|
6082 Aluminum
|
Aerospace Components |
Preferred due to high strength |
Not commonly used |
Automotive Parts |
High-performance, racing |
Structural, chassis parts |
Marine & Shipbuilding |
Prone to corrosion |
Excellent corrosion resistance |
Bicycle Frames |
Lightweight and strong |
More affordable alternative |
CNC Machining Parts |
Best for high-stress applications |
Great for cost-effective machining |
Structural Engineering |
Not ideal due to low weldability |
Bridges, buildings, support structures |
Conclusion: Which Aluminum Alloy Should You Choose?
Choose 7075 aluminum if:
- You need maximum strength and durability.
- Your application involves high-stress aerospace, military, or automotive racing components.
- You require superior machinability and are not concerned about weldability.
Choose 6082 aluminum if:
- You need corrosion resistance for marine or outdoor applications.
- Your project requires welding and structural strength.
- You want a cost-effective, strong, and versatile aluminum alloy.
For CNC machining factories and custom CNC machining services, the choice between 7075 and 6082 aluminum depends on strength, corrosion resistance, machinability, and budget requirements.
Looking for precision CNC machining in 7075 or 6082 aluminum? Contact us today for high-quality custom CNC machining and prototype manufacturing services!
7075-T6 vs. 6082-T6 Aluminum Properties: A Complete Comparison
When selecting an aluminum alloy for high-performance CNC machining, aerospace, automotive, or structural applications, 7075-T6 and 6082-T6 aluminum are two of the most popular choices.
7075-T6 aluminum is an ultra-high-strength alloy, often used in aerospace, defense, and automotive racing.
6082-T6 aluminum is a high-strength, corrosion-resistant alloy, commonly used in marine, structural, and industrial applications.
The T6 temper means both alloys have undergone solution heat treatment and artificial aging, enhancing their mechanical properties. But which one is better for your application?
Let’s analyze their chemical composition, mechanical properties, and key differences to help you make the right choice.
7075-T6 vs. 6082-T6 Chemical Composition Table
Element
|
7075-T6 (%)
|
6082-T6 (%)
|
Aluminum (Al) |
Balance |
Balance |
Zinc (Zn) |
5.1 – 6.1 |
0.0 |
Magnesium (Mg) |
2.1 – 2.9 |
0.6 – 1.2 |
Silicon (Si) |
0.0 – 0.4 |
0.7 – 1.3 |
Copper (Cu) |
1.2 – 2.0 |
0.0 – 0.1 |
Manganese (Mn) |
0.3 |
0.4 – 1.0 |
Chromium (Cr) |
0.18 – 0.28 |
0.0 – 0.25 |
Iron (Fe) |
0.5 max |
0.0 – 0.5 |
Key Takeaways:
- 7075-T6 contains high levels of zinc (Zn) and copper (Cu), which contribute to its high strength and hardness.
- 6082-T6 contains magnesium (Mg) and silicon (Si), improving corrosion resistance and weldability.
- 7075-T6 is significantly stronger, but 6082-T6 offers better corrosion resistance and machinability.
If strength is the priority, 7075-T6 is the best choice. If corrosion resistance and weldability are needed, 6082-T6 is the better option.
7075-T6 vs. 6082-T6 Aluminum: Mechanical Properties Comparison
When selecting between 7075-T6 and 6082-T6 aluminum for CNC machining, aerospace, automotive, marine, or structural applications, their mechanical properties play a crucial role.
- 7075-T6 aluminum is known for its exceptional strength, hardness, and fatigue resistance, making it a preferred choice for high-performance and aerospace applications.
- 6082-T6 aluminum, on the other hand, offers great corrosion resistance, good strength, and excellent weldability, making it ideal for marine and structural applications.
Which alloy is better for your project?
To help you decide, let’s compare tensile strength, yield strength, elongation, hardness, thermal conductivity, and other essential mechanical properties.
Tensile Strength: 7075-T6 vs. 6082-T6 Aluminum
- 7075-T6 Tensile Strength: 500–580 MPa
- 6082-T6 Tensile Strength: 300–340 MPa
Key Takeaway:
- 7075-T6 is significantly stronger than 6082-T6, making it ideal for high-stress applications like aerospace and defense.
- 6082-T6 is strong but not as tough as 7075-T6, making it more suitable for structural and marine applications where corrosion resistance is needed.
For applications where maximum strength is needed, 7075-T6 is the better choice.
Yield Strength: 7075-T6 vs. 6082-T6 Aluminum
- 7075-T6 Yield Strength: 430–500 MPa
- 6082-T6 Yield Strength: 260–300 MPa
Key Takeaway:
- 7075-T6 has almost twice the yield strength of 6082-T6, meaning it can withstand higher stress before permanent deformation occurs.
- 6082-T6 is better suited for applications that require forming or bending before final assembly.
For high-load applications requiring rigidity, 7075-T6 is superior.
Elongation at Break: 7075-T6 vs. 6082-T6 Aluminum
- 7075-T6 Elongation at Break: 5–10%
- 6082-T6 Elongation at Break: 8–12%
Key Takeaway:
- 6082-T6 is more ductile than 7075-T6, making it easier to form, bend, and shape before breaking.
- 7075-T6 is more brittle, meaning it can fracture under excessive stress.
If forming or bending is required, 6082-T6 is the better choice.
Brinell Hardness: 7075-T6 vs. 6082-T6 Aluminum
- 7075-T6 Brinell Hardness: 150–160 HB
- 6082-T6 Brinell Hardness: 85–95 HB
Key Takeaway:
- 7075-T6 is almost twice as hard as 6082-T6, meaning it is more resistant to wear and deformation.
- 6082-T6 is softer, making it easier to machine and work with.
If hardness and wear resistance are priorities, 7075-T6 is the better option.
Modulus of Elasticity: 7075-T6 vs. 6082-T6 Aluminum
- 7075-T6 Modulus of Elasticity: 70–72 GPa
- 6082-T6 Modulus of Elasticity: 68–70 GPa
Key Takeaway:
- Both alloys have similar stiffness, meaning they resist deformation at nearly the same rate under stress.
- 7075-T6 has slightly higher elasticity, making it better for high-performance applications that experience stress cycles.
For applications requiring high stiffness, both alloys perform similarly.
Thermal Conductivity: 7075-T6 vs. 6082-T6 Aluminum
- 7075-T6 Thermal Conductivity: 130–150 W/m·K
- 6082-T6 Thermal Conductivity: 180–200 W/m·K
Key Takeaway:
- 6082-T6 conducts heat more efficiently than 7075-T6, making it a better choice for heat exchangers, cooling systems, and applications requiring high thermal dissipation.
- 7075-T6 retains more heat, which can be a disadvantage in applications needing rapid heat removal.
For applications needing efficient heat transfer, 6082-T6 is the better choice.
Density: 7075-T6 vs. 6082-T6 Aluminum
- 7075-T6 Density: 2.81 g/cm³
- 6082-T6 Density: 2.70 g/cm³
Key Takeaway:
- 6082-T6 is slightly lighter than 7075-T6, but the difference is minor.
- For weight-sensitive applications, 6082-T6 provides slight weight savings.
Both alloys are lightweight compared to steel, making them ideal for aerospace and automotive applications.
Melting Point: 7075-T6 vs. 6082-T6 Aluminum
- 7075-T6 Melting Point: 477–635°C
- 6082-T6 Melting Point: 555–650°C
Key Takeaway:
- 6082-T6 has a slightly higher melting point, making it more stable at high temperatures.
- 7075-T6 can soften at lower temperatures, affecting performance in high-heat environments.
For high-temperature applications, 6082-T6 is the better choice.
Resistivity: 7075-T6 vs. 6082-T6 Aluminum
- 7075-T6 Resistivity: 5.0 × 10⁻⁶ Ω·m
- 6082-T6 Resistivity: 4.0 × 10⁻⁶ Ω·m
Key Takeaway:
- 6082-T6 has lower electrical resistivity, making it slightly better for electrical applications.
- 7075-T6 is not commonly used in electrical systems due to its high resistance.
For electrical conductivity applications, 6082-T6 is the preferred option.
Coefficient of Thermal Expansion: 7075-T6 vs. 6082-T6 Aluminum
- 7075-T6 Coefficient of Thermal Expansion: 22–24 µm/m·K
- 6082-T6 Coefficient of Thermal Expansion: 23–25 µm/m·K
Key Takeaway:
- Both alloys expand at similar rates with temperature changes.
- For precision CNC machining applications, slight expansion differences should be considered in design tolerances.
Both alloys have comparable thermal expansion, making them suitable for similar environments.
Conclusion: Which Aluminum Alloy is Best for Your Project?
Choose 7075-T6 aluminum if:
- You need maximum strength and hardness.
- Your application involves high stress, aerospace, or military use.
- You require exceptional fatigue resistance and wear resistance.
Choose 6082-T6 aluminum if:
- You need corrosion resistance for marine or outdoor environments.
- Your project requires welding and good machinability.
- You need better thermal and electrical conductivity.
For CNC machining, 7075-T6 is best for high-stress, high-strength applications, while 6082-T6 is better for corrosion resistance, welding, and heat dissipation.
7075-T6 vs. 6082-T6: Which Aluminum Alloy is Better?
When choosing an aluminum alloy for CNC machining, aerospace, automotive, or structural applications, 7075-T6 and 6082-T6 are two of the most commonly used options. Both alloys are heat-treated (T6) for enhanced mechanical properties, but they differ in strength, corrosion resistance, weldability, machinability, and cost.
- 7075-T6 aluminum is known for exceptional strength, hardness, and fatigue resistance, making it the preferred choice for high-performance applications.
- 6082-T6 aluminum offers superior corrosion resistance, weldability, and affordability, making it ideal for marine, structural, and industrial applications.
Which alloy is the best for your specific project?
To help you decide, let's compare strength, corrosion resistance, machinability, weldability, formability, applications, and cost.
Key Comparison Points: 7075-T6 vs. 6082-T6
Property |
7075-T6 Aluminum |
6082-T6 Aluminum |
Strength |
Extremely high strength (500–580 MPa tensile) |
Moderate strength (300–340 MPa tensile) |
Corrosion Resistance |
Poor, needs anodizing or coating |
Excellent, naturally corrosion-resistant |
Machinability |
Excellent, easy to machine |
Good, but stickier than 7075 |
Weldability |
Poor, prone to cracking |
Excellent, commonly used in welded structures |
Formability |
Low, brittle under bending |
Good, can be bent and shaped easily |
Applications |
Aerospace, defense, automotive racing, sporting equipment |
Marine, bridges, construction, industrial components |
Cost & Availability |
Expensive, limited availability |
Affordable, widely available |
- 7075-T6 is the best choice for extreme strength and wear resistance.
- 6082-T6 is the better choice for corrosion resistance, welding, and affordability.
Strength: Which Alloy is Stronger?
- 7075-T6 Tensile Strength: 500–580 MPa
- 6082-T6 Tensile Strength: 300–340 MPa
- 7075-T6 Yield Strength: 430–500 MPa
- 6082-T6 Yield Strength: 260–300 MPa
Key Takeaway:
- 7075-T6 is nearly twice as strong as 6082-T6, making it the top choice for high-stress applications like aerospace, military, and high-performance sports equipment.
- 6082-T6 has sufficient strength for structural applications but isn’t suitable for extreme loads.
If strength is the most important factor, 7075-T6 is the superior choice.
Corrosion Resistance: Which Alloy Performs Better?
- 6082-T6 aluminum has excellent corrosion resistance, making it ideal for marine, coastal, and outdoor applications.
- 7075-T6 aluminum has lower corrosion resistance because of its higher zinc content, making it prone to oxidation unless anodized or coated.
Key Takeaway:
- 6082-T6 is better for environments exposed to moisture, saltwater, and humidity.
- 7075-T6 requires additional protective coatings to prevent corrosion.
For corrosion-resistant applications, 6082-T6 is the best option.
Machinability: Which Alloy is Easier to Machine?
- 7075-T6 is easier to machine than 6082-T6 because it is harder and produces cleaner cuts with less tool wear.
- 6082-T6 tends to be stickier, meaning it requires sharp cutting tools and proper lubrication to prevent material buildup.
Key Takeaway:
- If machining speed and surface finish are a priority, 7075-T6 is the better choice.
- 6082-T6 is still machinable but requires careful tool selection and cutting speeds.
For high-precision CNC machining, 7075-T6 is preferred.
Weldability: Which Alloy is Better for Welding?
- 6082-T6 is highly weldable, making it the preferred choice for welded structures and fabricated parts.
- 7075-T6 is difficult to weld due to its high zinc and copper content, which makes it prone to cracking.
Key Takeaway:
- If welding is required, 6082-T6 is the best choice.
- 7075-T6 is typically fastened using bolts, rivets, or adhesives instead of welding.
For applications requiring welding, 6082-T6 is the clear winner.
Formability: Which Alloy is Easier to Shape and Bend?
- 6082-T6 is more ductile and can be bent and formed more easily than 7075-T6.
- 7075-T6 is brittle and may crack under bending or forming stress.
Key Takeaway:
- For applications that require bending or shaping, 6082-T6 is the better choice.
- 7075-T6 is best for rigid, high-strength components that do not require forming.
For formed parts and sheet metal applications, 6082-T6 is the best option.
Applications: Where is Each Alloy Used?
Industry |
7075-T6 Aluminum |
6082-T6 Aluminum |
Aerospace & Defense |
Aircraft frames, structural components |
Not commonly used |
Automotive & Racing |
High-performance chassis, suspension |
Structural parts, body panels |
Marine & Shipbuilding |
Poor corrosion resistance |
Ideal for boat hulls, frames |
Construction & Architecture |
Not common |
Bridges, buildings, scaffolding |
CNC Machining & Prototyping |
High-precision, durable parts |
Cost-effective structural parts |
- 7075-T6 is best for aerospace, defense, and high-performance applications.
- 6082-T6 is best for marine, construction, and structural applications.
Cost and Availability: Which Alloy is More Affordable?
- 7075-T6 is more expensive than 6082-T6, due to its higher strength and aerospace-grade properties.
- 6082-T6 is widely available and more affordable, making it a better choice for budget-sensitive projects.
Estimated Material Costs (Per kg)
- 7075-T6 Aluminum Cost: $6 – $10 per kg
- 6082-T6 Aluminum Cost: $4 – $7 per kg
Key Takeaway:
- If cost is a concern, 6082-T6 is the better choice.
- If strength is the priority, 7075-T6 is worth the additional cost.
For budget-conscious projects, 6082-T6 is more economical.
Conclusion: Which Aluminum Alloy is Best?
Choose 7075-T6 aluminum if:
- You need maximum strength and hardness.
- Your application involves high stress, aerospace, or defense applications.
- You require excellent machinability and fatigue resistance.
Choose 6082-T6 aluminum if:
- You need corrosion resistance for marine or outdoor applications.
- Your project requires welding, bending, or forming.
- You need an affordable, high-strength aluminum alloy for structural applications.
For CNC machining services, 7075-T6 is best for high-performance parts, while 6082-T6 is better for cost-effective, corrosion-resistant applications.
Summary: 7075 vs. 6082 Aluminum – A Detailed Comparison Chart
7075 vs. 6082 Aluminum: Quick Overview
7075-T6 and 6082-T6 aluminum are among the most commonly used aluminum alloys, each offering unique mechanical properties suited for different applications. Below is a summarized comparison of these two alloys based on strength, weldability, formability, corrosion resistance, processing, and cost.
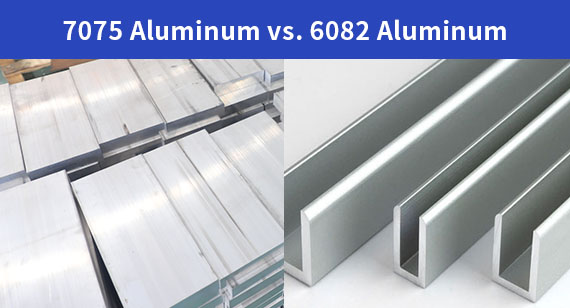
7075 vs. 6082 Aluminum: Comparison Chart
Property |
7075-T6 Aluminum |
6082-T6 Aluminum |
Strength |
Very high (500–580 MPa tensile strength, 430–500 MPa yield strength) |
Moderate (300–340 MPa tensile strength, 260–300 MPa yield strength) |
Weldability |
Poor – Prone to cracking, difficult to weld |
Excellent – Good for MIG/TIG welding and fabrication |
Formability |
Poor – Brittle under bending and forming |
Good – Can be bent and shaped easily |
Corrosion Resistance |
Low – Needs anodizing or coatings for protection |
Excellent – Naturally corrosion-resistant, ideal for marine applications |
Machinability |
Excellent – Produces clean cuts, easy to machine |
Good – Machinable but slightly stickier than 7075 |
Processing Complexity |
Difficult – Requires precision machining and special coatings |
Easier – Can be processed with conventional methods |
Cost |
Expensive – $6–$10 per kg |
More affordable – $4–$7 per kg |
Common Applications |
Aerospace, defense, automotive racing, high-performance sports equipment |
Marine, structural engineering, industrial components, bridges |
- 7075-T6 is the best choice for extreme strength, high-stress applications, and CNC machining.
- 6082-T6 is the better choice for welding, corrosion resistance, affordability, and structural applications.
Mechanical Properties of 7075 vs. 6082 Aluminum
1. Strength: Which Aluminum Alloy is Stronger?
- 7075-T6 Aluminum has a tensile strength of 500–580 MPa and a yield strength of 430–500 MPa, making it one of the strongest aluminum alloys available.
- 6082-T6 Aluminum has a tensile strength of 300–340 MPa and a yield strength of 260–300 MPa, which is strong but not as tough as 7075.
- 7075-T6 is nearly twice as strong as 6082-T6, making it ideal for aerospace, defense, and high-stress applications.
For maximum strength, choose 7075-T6 aluminum.
2. Weldability: Which Alloy is Easier to Weld?
- 6082-T6 aluminum is highly weldable, making it a great choice for structural applications, marine environments, and fabricated components.
- 7075-T6 aluminum is difficult to weld, as it is prone to cracking and heat-induced stress failure.
For applications requiring welding, 6082-T6 is the better option.
3. Formability: Which Alloy is Easier to Shape and Bend?
- 6082-T6 aluminum is more ductile, meaning it can be bent and shaped with ease.
- 7075-T6 aluminum is more brittle, meaning it may crack if bent without proper heat treatment.
For bending and forming applications, 6082-T6 is the best choice.
4. Corrosion Resistance: Which Alloy Performs Better?
- 6082-T6 has excellent corrosion resistance, making it perfect for marine and outdoor applications.
- 7075-T6 is more prone to corrosion and requires anodizing or protective coatings.
For environments exposed to moisture and saltwater, 6082-T6 aluminum is the better option.
5. Processing: Which Alloy is Easier to Machine and Fabricate?
- 7075-T6 aluminum is easier to machine due to its hardness, producing cleaner cuts and less tool wear.
- 6082-T6 aluminum requires careful machining as it is slightly stickier, needing lubricants and sharp cutting tools.
For high-precision CNC machining, 7075-T6 aluminum is the superior choice.
6. Cost: Which Aluminum Alloy is More Affordable?
- 7075-T6 aluminum is expensive, typically costing $6–$10 per kg, due to its high-strength properties and aerospace-grade quality.
- 6082-T6 aluminum is more affordable, ranging from $4–$7 per kg, making it ideal for budget-sensitive applications.
For cost-effective projects, 6082-T6 aluminum is the better option.
Conclusion: Which Aluminum Alloy is Best for Your Project?
Choose 7075-T6 Aluminum If:
- You need the highest possible strength for applications like aerospace, defense, and high-performance sports equipment.
- You require excellent machinability for precision CNC machining parts.
- Your application does not require welding.
- You can apply protective coatings to prevent corrosion.
Choose 6082-T6 Aluminum If:
- You need excellent corrosion resistance, especially for marine, structural, and outdoor applications.
- You require good weldability for fabricated structures and industrial parts.
- Your project involves forming or bending components.
- You are looking for a cost-effective, strong, and versatile aluminum alloy.
For CNC machining, 7075-T6 aluminum is best for extreme strength, while 6082-T6 aluminum is ideal for corrosion resistance, welding, and affordability.
Pros and Cons of 7075 vs. 6082 Aluminum: Which One is Right for Your Project?
Choosing the right aluminum alloy is essential for CNC machining, aerospace, automotive, structural, and marine applications. 7075 and 6082 aluminum are two of the most commonly used alloys, each offering unique advantages and limitations.
- 7075 aluminum is best known for its exceptional strength and hardness, making it ideal for high-stress applications like aerospace and military components.
- 6082 aluminum offers superior corrosion resistance, weldability, and affordability, making it a preferred material for marine, transportation, and structural applications.
Which alloy is best for your specific needs?
To help you decide, let’s break down the pros and cons of 7075 and 6082 aluminum, and discuss when to use each alloy.
7075 Aluminum: Pros and Cons
Pros of 7075 Aluminum
Extremely High Strength
- 7075 aluminum is one of the strongest aluminum alloys available, with a tensile strength of 500–580 MPa and a yield strength of 430–500 MPa.
- This makes it suitable for high-stress applications like aerospace, military, and automotive racing.
Excellent Fatigue Resistance
- 7075 aluminum has outstanding fatigue resistance, making it ideal for components subjected to repeated stress cycles, such as aircraft structures and bicycle frames.
Superior Hardness and Wear Resistance
- With a Brinell hardness of 150–160 HB, 7075 aluminum is highly resistant to wear and impact, reducing surface damage in high-load applications.
Lightweight Yet Strong
- Despite its steel-like strength, 7075 aluminum is significantly lighter than steel, making it an excellent choice for weight-sensitive applications like aerospace and sports equipment.
Good Machinability
- Due to its hardness, 7075 aluminum machines very well, producing clean cuts and smooth finishes with minimal tool wear.
Cons of 7075 Aluminum
Poor Corrosion Resistance
- 7075 aluminum is prone to corrosion, especially in marine and humid environments.
- Requires anodizing or protective coatings to enhance corrosion resistance.
Difficult to Weld
- 7075 aluminum is challenging to weld due to its high zinc and copper content, which makes it prone to hot cracking and porosity.
- It is typically joined using bolts, rivets, or adhesives rather than welding.
Lower Formability
- 7075 aluminum is brittle under bending or forming, making it less suitable for applications requiring shaping or deep drawing.
Higher Cost
- 7075 aluminum is more expensive than 6082 aluminum, with prices ranging from $6–$10 per kg.
6082 Aluminum: Pros and Cons
Pros of 6082 Aluminum
Good Strength and Structural Stability
- While not as strong as 7075, 6082 aluminum still has excellent mechanical properties, with a tensile strength of 300–340 MPa and a yield strength of 260–300 MPa.
- It is commonly used in bridges, construction, and industrial structures.
Superior Corrosion Resistance
- 6082 aluminum is highly corrosion-resistant, making it ideal for marine environments, outdoor applications, and humid climates.
- Does not require protective coatings, unlike 7075 aluminum.
Excellent Weldability
- 6082 aluminum is one of the most weldable high-strength aluminum alloys, making it a top choice for fabricated structures and industrial applications.
Better Formability
- 6082 aluminum is more ductile than 7075, allowing for easier bending, rolling, and forming.
- Suitable for complex shapes and deep-drawn components.
More Affordable
- 6082 aluminum is less expensive than 7075, typically costing $4–$7 per kg, making it ideal for budget-sensitive projects.
Cons of 6082 Aluminum
Lower Strength Than 7075
- While strong, 6082 aluminum does not match the strength of 7075 aluminum, making it less suitable for extreme stress applications.
Slightly More Difficult to Machine
- 6082 aluminum is softer and stickier than 7075, making CNC machining slightly more challenging.
- Requires sharp cutting tools and lubrication to prevent tool wear and material buildup.
When to Use 7075 or 6082?
Use 7075 Aluminum If:
- Maximum strength is required, such as in aerospace, military, or high-performance sports equipment.
- High fatigue resistance is needed, especially in aircraft, bicycle frames, and automotive racing parts.
- CNC machining is a priority, as 7075 aluminum machines well and produces excellent surface finishes.
- The application does not require welding, as 7075 is difficult to weld and prone to cracking.
Best for: Aerospace, defense, high-performance automotive, CNC machining, sporting goods.
Use 6082 Aluminum If:
- Corrosion resistance is important, such as in marine, coastal, and outdoor environments.
- Welding is required, as 6082 aluminum is one of the most weldable high-strength alloys.
- Good formability is needed, as 6082 aluminum can be easily bent, rolled, and shaped.
- Budget is a concern, as 6082 is more affordable than 7075 while still offering good strength.
Best for: Marine, construction, bridges, transportation, structural engineering, industrial parts.
Final Thoughts: Which Aluminum Alloy is Best?
- 7075 aluminum is the best choice when strength, hardness, and wear resistance are the top priorities.
- 6082 aluminum is better suited for applications requiring weldability, corrosion resistance, and affordability.
Quick Summary:
Feature
|
7075 Aluminum
|
6082 Aluminum
|
Strength |
Very high (500–580 MPa) |
Moderate (300–340 MPa) |
Corrosion Resistance |
Poor, needs protective coating |
Excellent, naturally corrosion-resistant |
Weldability |
Difficult, prone to cracking |
Excellent, highly weldable |
Formability |
Brittle, difficult to shape |
Good, easy to bend and form |
Machinability |
Excellent |
Good, but requires sharp tools |
Cost |
Expensive ($6–$10 per kg) |
More affordable ($4–$7 per kg) |
Best For |
Aerospace, defense, racing, CNC machining |
Marine, construction, structural applications |
- For CNC machining, aerospace, and extreme strength applications, choose 7075 aluminum.
- For marine, structural, and corrosion-resistant applications, choose 6082 aluminum.
7075 and 6082 Aluminum CNC Machining Manufacturing Considerations
When selecting 7075 or 6082 aluminum for CNC machining, it's essential to understand their machining behavior, tool wear, cutting speeds, and finishing requirements. These alloys differ significantly in terms of machinability, tool selection, and application requirements, influencing the final cost, precision, and production efficiency.
- 7075 aluminum is ideal for high-strength, high-precision machining, commonly used in aerospace, defense, and automotive applications.
- 6082 aluminum offers better weldability and corrosion resistance, making it suitable for marine, structural, and industrial applications.
What CNC machining challenges should you expect with these alloys?
Let's examine cutting speeds, tool wear, surface finishing, and cooling requirements for 7075 and 6082 aluminum CNC machining.
7075 and 6082 Aluminum CNC Machining Considerations
1. Machinability and Cutting Speeds
Property |
7075 Aluminum |
6082 Aluminum |
Machinability Rating |
Excellent |
Good |
Cutting Speed |
Higher speeds possible |
Requires lower speeds to avoid tool wear |
Chips Formation |
Short, breakable chips |
Longer, sticky chips |
- 7075 aluminum has better machinability than 6082, producing cleaner cuts and shorter chips, reducing tool wear.
- 6082 aluminum tends to be stickier, requiring sharp cutting tools and proper lubrication to avoid built-up edge (BUE) formation.
For precision CNC machining, 7075 aluminum is preferred.
For applications requiring welding after machining, 6082 aluminum is the better choice.
2. Tool Wear and Cutting Tools
- 7075 aluminum causes less tool wear due to its hardness and clean cutting behavior.
- 6082 aluminum requires carbide or coated cutting tools to prevent material adhesion and chip buildup.
- Coolant or lubrication is essential for 6082 aluminum to reduce heat and friction.
For longer tool life, CNC machining of 7075 aluminum is more efficient.
For best results with 6082 aluminum, use sharp carbide tools and proper lubrication.
3. Surface Finishing and Post-Processing
- 7075 aluminum provides an excellent surface finish and requires minimal post-processing.
- 6082 aluminum needs additional smoothing due to its slightly softer texture.
- Anodizing improves corrosion resistance for 7075 aluminum.
For high-precision, smooth surface finishes, 7075 aluminum is the better choice.
Both 7075 and 6082 aluminum alloys are used across various industries, but they cater to different strength, corrosion resistance, and machining requirements.
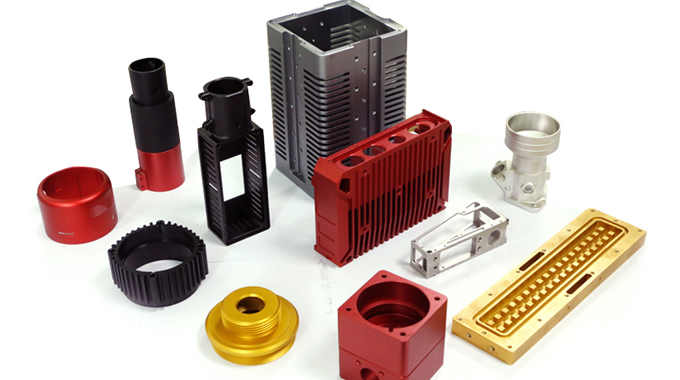
1. Electronics Industry
7075 aluminum is used in:
- High-performance electronic enclosures and heat sinks
- Precision-machined mounting brackets and frames
6082 aluminum is used in:
- Corrosion-resistant electronic casings
- Lightweight industrial enclosures
7075 is ideal for strength-critical electronic components.
6082 is better for weatherproof, corrosion-resistant enclosures.
2. Medical Industry
7075 aluminum is used in:
- High-strength surgical tools and orthopedic devices
- Durable prosthetic components
6082 aluminum is used in:
- Welded medical equipment frames and housings
- Corrosion-resistant biomedical devices
For CNC-machined high-strength medical tools, 7075 aluminum is preferred.
For structural and welded medical equipment, 6082 aluminum is better.
3. Industrial Applications
7075 aluminum is used in:
- High-load industrial machinery parts
- Precision-machined jigs and fixtures
6082 aluminum is used in:
- Structural frames and support components
- Corrosion-resistant pipes and tanks
7075 aluminum is better for wear-resistant industrial components.
6082 aluminum is ideal for corrosion-resistant applications.
4. Automotive Industry
7075 aluminum is used in:
- Performance car suspension components
- High-strength chassis parts
6082 aluminum is used in:
- Structural car body parts
- Lightweight automotive panels
For racing and performance vehicles, 7075 aluminum is the top choice.
For structural automotive frames, 6082 aluminum is preferred.
5. Aerospace Industry
7075 aluminum is used in:
- Aircraft fuselage structures
- Landing gear and wing components
6082 aluminum is used in:
- Structural aerospace parts requiring corrosion resistance
- Welded aircraft frames and fuel tanks
For aerospace components requiring maximum strength, 7075 aluminum is superior.
For lightweight, corrosion-resistant aerospace structures, 6082 aluminum is ideal.
6. Other Applications
7075 aluminum is used in:
- High-performance sports equipment (bicycles, archery bows, golf clubs)
- Military firearms and defense systems
6082 aluminum is used in:
- Marine boat hulls, docks, and offshore platforms
- Bridges and construction frameworks
7075 aluminum is best for performance-driven applications.
6082 aluminum is best for marine, outdoor, and construction applications.
Conclusion: Which Aluminum Alloy is Best for CNC Machining?
Use 7075 Aluminum If:
- You need extreme strength and hardness, such as in aerospace, defense, and high-performance applications.
- You require superior machinability for high-precision CNC machining components.
- Your application doesn’t require welding, as 7075 aluminum is difficult to weld.
Best for: Aerospace, defense, racing, CNC machining, high-stress applications.
Use 6082 Aluminum If:
- You need corrosion resistance, especially for marine, structural, or outdoor applications.
- You require good weldability, as 6082 aluminum is one of the most weldable high-strength alloys.
- Your project involves forming or bending components, as 6082 aluminum is more ductile.
Best for: Marine, construction, structural engineering, industrial components.
Final Thoughts
- 7075 aluminum is the best choice for extreme strength, fatigue resistance, and high-precision CNC machining.
- 6082 aluminum is better suited for applications requiring corrosion resistance, welding, and cost-effectiveness.
For CNC machining services, 7075-T6 is best for aerospace and high-stress parts, while 6082-T6 is better for cost-effective, corrosion-resistant applications.
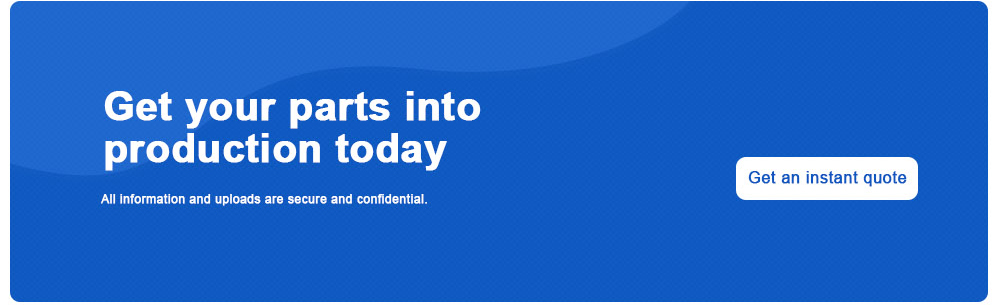
FAQs: 7075 vs. 6082 Aluminum – Everything You Need to Know
What is the difference between 7075 and 6082 aluminum?
- 7075 aluminum is a high-strength, aerospace-grade alloy with excellent fatigue resistance but poor corrosion resistance and weldability.
- 6082 aluminum is a medium-strength, corrosion-resistant alloy with good weldability and machinability, commonly used in marine and structural applications.
If strength is the priority, choose 7075 aluminum. If corrosion resistance and welding are important, choose 6082 aluminum.
Is 7075 aluminum better than 6061 aluminum?
- 7075 aluminum is significantly stronger than 6061 aluminum, making it ideal for high-stress aerospace, defense, and performance applications.
- 6061 aluminum is more corrosion-resistant, more affordable, and easier to weld, making it better for general-purpose applications.
If maximum strength is required, 7075 aluminum is better. If weldability and corrosion resistance are needed, 6061 aluminum is a better choice.
What is the aluminum equivalent of 6082?
- The closest aluminum equivalent to 6082 is 6061 aluminum, both belonging to the 6xxx series and offering medium strength, good corrosion resistance, and excellent weldability.
- In European standards, EN AW-6082 is commonly used in place of 6061 aluminum.
For structural applications, 6082 aluminum is a common alternative to 6061.
What are the disadvantages of 7075 aluminum?
- Poor weldability – Prone to hot cracking, making it difficult to weld.
- Lower corrosion resistance – Requires anodizing or coatings for protection.
- Brittle under bending – Not ideal for deep forming or shaping applications.
- Higher cost – More expensive than 6082 or 6061 aluminum.
7075 aluminum is best for high-strength applications where welding and corrosion resistance are not required.
What are the advantages of 7075 aluminum?
- Extremely high strength – Among the strongest aluminum alloys available.
- Excellent fatigue resistance – Ideal for aircraft and military components.
- Lightweight yet durable – High strength-to-weight ratio makes it great for aerospace and sports equipment.
- Superior machinability – Produces clean cuts and excellent surface finishes in CNC machining.
For extreme strength and durability, 7075 aluminum is the top choice.
What is the strongest type of aluminum?
- 7075 aluminum is one of the strongest aluminum alloys, with a tensile strength of 500–580 MPa.
- 7050 and 7475 aluminum are also very strong and used in aerospace applications.
For maximum strength, 7075 aluminum is the best option.
Is 7075 aluminum as strong as steel?
- 7075 aluminum has a tensile strength of up to 580 MPa, which is comparable to some mild steels but still weaker than high-carbon steels.
- However, 7075 aluminum is much lighter than steel, making it superior for weight-sensitive applications.
7075 aluminum offers a great balance between strength and weight, making it a top choice for aerospace and performance applications.
Why can't you weld 7075 aluminum?
- 7075 aluminum is difficult to weld due to its high zinc and copper content, which makes it prone to hot cracking and poor fusion.
- Instead of welding, 7075 aluminum parts are often joined using fasteners, rivets, or adhesives.
For welding applications, 6082 or 6061 aluminum is a better choice.
What is the strongest weldable aluminum?
- The strongest weldable aluminum alloy is 5083 aluminum, commonly used in marine and structural applications.
- 6061 and 6082 aluminum are also weldable, though not as strong as 5083.
For high-strength welding applications, 5083 or 6082 aluminum is recommended.
How durable is 7075 aluminum?
- 7075 aluminum is highly durable, wear-resistant, and impact-resistant, making it ideal for military, aerospace, and sports applications.
- Its hardness (150–160 HB) ensures long-lasting performance in demanding conditions.
For high-stress applications, 7075 aluminum is one of the most durable aluminum alloys.
Can you stress-relieve 7075 aluminum?
- Yes, 7075 aluminum can be stress-relieved through controlled heat treatments to reduce residual stresses from machining.
- The T73 temper is a stress-relieved version of T6, providing better toughness and corrosion resistance.
For applications requiring stress relief, 7075-T73 aluminum is a good alternative.
Which aluminum is easiest to weld?
- 5083, 6061, and 6082 aluminum are among the easiest to weld, making them ideal for marine, structural, and fabrication applications.
- Avoid 7075 aluminum if welding is required.
For welding, 6082 aluminum is one of the best choices.
Can 7075 aluminum be forged?
- Yes, 7075 aluminum can be forged, and it is commonly used in high-strength aerospace and automotive components.
- Forged 7075 aluminum parts offer superior fatigue resistance and structural integrity.
For high-performance forged components, 7075 aluminum is a great option.
Can you bend 7075 aluminum?
- 7075 aluminum is difficult to bend due to its high strength and brittleness.
- If bending is required, heat treatment or annealing may help reduce cracking risks.
For applications requiring bending, 6082 aluminum is a better choice.
What is the fatigue limit of 7075 aluminum?
- The fatigue limit of 7075 aluminum is approximately 160–180 MPa, making it one of the most fatigue-resistant aluminum alloys.
- This makes it ideal for aerospace and structural applications where parts undergo repeated stress cycles.
For fatigue-resistant parts, 7075 aluminum is one of the best choices.
Is 7075 aluminum stronger than carbon fiber?
- No, carbon fiber has a higher strength-to-weight ratio than 7075 aluminum.
- However, 7075 aluminum is more impact-resistant and machinable, making it preferable for high-load applications.
- Carbon fiber is better for ultra-lightweight applications, but 7075 aluminum is better for durability and machining.
For lightweight, high-strength applications, carbon fiber is superior, but for CNC-machined durability, 7075 aluminum is preferred.
Conclusion: Choosing Between 7075 and 6082 Aluminum
- 7075 aluminum is best for aerospace, defense, racing, and high-strength CNC machining applications.
- 6082 aluminum is ideal for marine, structural, welding, and corrosion-resistant applications.
For extreme strength and fatigue resistance, choose 7075 aluminum.
For corrosion resistance, welding, and cost-effectiveness, choose 6082 aluminum.