Choosing the right type of metal for CNC machining, manufacturing, and industrial applications can be confusing. Should you use ferrous metals or non-ferrous metals? Which is better for strength, corrosion resistance, weight, or cost? If you're unsure about the differences, you're not alone.
Problem: Using the wrong type of metal in manufacturing can lead to premature failure, rust, excessive weight, or unnecessary costs. For example, ferrous metals are stronger but prone to rust, while non-ferrous metals resist corrosion but may be weaker.
Agitation: Without understanding their differences, industries like automotive, aerospace, medical, and construction may suffer from inefficiency, reduced durability, or higher costs.
Solution: This guide explains everything you need to know about ferrous vs. non-ferrous metals, including their properties, advantages, applications, and CNC machining considerations.
Keep reading to discover which type of metal best suits your needs.
What Is a Ferrous Metal?
Ferrous metals are metals that contain iron (Fe). They are known for their strength, durability, and magnetic properties. Common ferrous metals include steel, stainless steel, carbon steel, cast iron, and wrought iron.
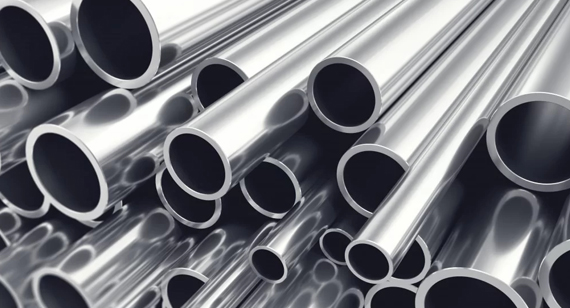
Characteristics of Ferrous Metals
- High Strength: Ferrous metals are stronger than most non-ferrous metals, making them ideal for structural and industrial applications.
- Magnetic Properties: Most ferrous metals are magnetic, making them useful for electrical applications.
- Prone to Rust: Many ferrous metals rust because of iron's reaction with moisture and oxygen. However, stainless steel is an exception due to its chromium content.
Ferrous metals are widely used in construction, automotive, aerospace, and manufacturing industries.
Advantages and Disadvantages of Ferrous Metals
Ferrous metals are the backbone of industrial manufacturing, offering high strength, durability, and versatility in numerous applications. They are widely used in construction, automotive, aerospace, and machinery industries due to their superior mechanical properties. However, despite their many advantages, ferrous metals also come with certain limitations, such as susceptibility to rust and weight concerns.
In this section, we will explore the advantages and disadvantages of ferrous metals, helping you determine when they are the best choice for CNC machining and manufacturing applications.
Advantages of Ferrous Metals
1. High Strength and Durability
- Ferrous metals are incredibly strong, making them ideal for heavy-duty applications such as bridges, buildings, automotive frames, and industrial machinery.
- Materials like carbon steel and alloy steel offer excellent load-bearing capacity and resistance to wear, ensuring longevity in harsh environments.
2. Cost-Effective and Widely Available
- Ferrous metals, especially mild steel and carbon steel, are relatively inexpensive due to their abundance and ease of production.
- The high availability of iron ore and the widespread use of steel in manufacturing make ferrous metals a cost-effective solution for industrial applications.
3. Magnetic Properties
- Most ferrous metals are magnetic, making them essential in applications requiring magnetic properties, such as electrical transformers, motors, and generators.
- This characteristic is particularly useful in electronic devices and power transmission systems.
4. Versatility in Applications
- Ferrous metals are used in almost every major industry, including construction, automotive, railways, shipbuilding, and heavy machinery.
- Different types of ferrous metals, such as stainless steel and alloy steel, allow for customized properties based on specific engineering needs.
5. Heat Resistance and Hardness
- Many ferrous metals, such as stainless steel and tool steel, exhibit excellent heat resistance.
- Cast iron and high-carbon steels are known for their hardness, making them ideal for cutting tools, engine components, and machine parts.
Ferrous metals provide unmatched strength, cost efficiency, and versatility, making them the first choice for demanding engineering applications.
Disadvantages of Ferrous Metals
1. Prone to Rust and Corrosion
- Ferrous metals containing iron are highly susceptible to rust when exposed to moisture and oxygen.
- Mild steel and carbon steel corrode easily, requiring coatings or alloying (such as adding chromium to create stainless steel) to improve resistance.
- Regular maintenance is often needed to prevent oxidation in outdoor or humid environments.
2. Heavier than Non-Ferrous Metals
- Ferrous metals are generally denser and heavier, which makes them less ideal for lightweight applications such as aerospace or portable consumer electronics.
- Aluminum and titanium, both non-ferrous metals, are often preferred when weight reduction is a priority.
3. Lower Machinability
- Some ferrous metals, particularly hardened steels and cast iron, can be difficult to machine due to their hardness and brittleness.
- They often require specialized CNC tooling and cooling techniques to avoid excessive tool wear and overheating.
4. Not Always Corrosion-Resistant
- While stainless steel offers excellent corrosion resistance, many other ferrous metals require protective coatings (e.g., galvanization or painting) to prevent rusting.
- Long-term exposure to harsh environments (e.g., marine applications) can degrade ferrous metals faster than non-ferrous metals like brass or aluminum.
5. Susceptibility to Oxidation at High Temperatures
- Some ferrous metals, such as low-carbon steel and iron, can oxidize or scale when exposed to extremely high temperatures.
- This requires heat-resistant coatings or the use of alloy steels for high-temperature industrial applications.
While ferrous metals are strong and affordable, they require additional protection against rust, weight concerns, and machining difficulties.
Conclusion: When to Use Ferrous Metals?
- Use ferrous metals when high strength and durability are required, such as in construction, automotive, and industrial machinery applications.
- Consider stainless steel or coated metals if corrosion resistance is important.
- For lightweight applications, non-ferrous metals like aluminum and titanium may be better alternatives.
Need high-quality CNC machining for ferrous metals? Contact us for expert solutions today!
Properties of Ferrous Metals
Ferrous metals play a fundamental role in industrial applications due to their high strength, durability, and versatility. Their unique properties make them ideal for construction, automotive, aerospace, machinery, and heavy equipment manufacturing. Understanding the key properties of ferrous metals helps manufacturers and engineers determine the best material for specific applications.
Key Properties of Ferrous Metals
1. High Strength and Hardness
- Ferrous metals are stronger than most non-ferrous metals, making them perfect for load-bearing structures, machinery, and tools.
- Carbon steel, stainless steel, and alloy steel offer excellent tensile strength, while cast iron provides high compressive strength.
2. Magnetic Properties
- Most ferrous metals, especially iron, steel, and cast iron, exhibit magnetic properties, which make them essential in electrical applications, motors, and generators.
- However, stainless steel (especially austenitic grades like 304 and 316) is non-magnetic due to its high chromium and nickel content.
3. Prone to Rust and Corrosion
- Ferrous metals containing iron are prone to rusting when exposed to moisture and oxygen.
- Stainless steel resists corrosion due to its chromium content, while carbon steel and cast iron require coatings or treatments (e.g., galvanization, painting, or powder coating) to prevent rust.
4. High Density and Weight
- Ferrous metals are denser and heavier than non-ferrous metals, which makes them ideal for structural applications but less suitable for weight-sensitive industries like aerospace.
5. Heat Resistance and Durability
- Many ferrous metals, such as tool steel and stainless steel, can withstand high temperatures and harsh environments.
- Cast iron has excellent heat resistance, making it a preferred choice for engine components and cookware.
6. High Melting Point
- Ferrous metals generally have high melting points, which enhances their structural integrity under extreme conditions.
- Example: Carbon steel melts at around 1,370°C (2,500°F), while stainless steel melts at 1,400°C–1,530°C (2,550°F–2,800°F).
Ferrous metals offer a combination of strength, durability, and heat resistance, making them essential for structural and industrial applications.
Examples and Uses of Ferrous Metals
Ferrous metals are widely used across various industries due to their superior mechanical properties. Each type of ferrous metal has unique characteristics that make it suitable for specific applications. Below is a breakdown of the most common ferrous metals and their uses.
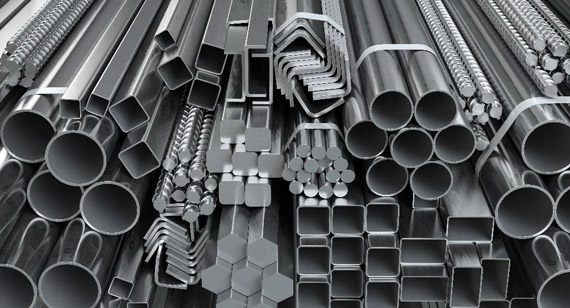
Common Ferrous Metals and Their Applications
1. Steel
Composition: Iron + Carbon (0.2% – 2.1%)
Properties: High strength, ductile, machinable, and affordable.
Uses:
- Construction – Beams, columns, and reinforcement bars.
- Automotive Industry – Car frames, engine parts, and gears.
- Machinery & Tools – CNC machining parts, cutting tools, and drill bits.
Steel is the most widely used ferrous metal due to its strength, affordability, and versatility.
2. Stainless Steel
Composition: Iron + Chromium (≥10.5%) + Nickel (varies by grade)
Properties: Corrosion-resistant, strong, durable, and non-magnetic (austenitic grades).
Uses:
- Medical Equipment – Surgical instruments, implants, and diagnostic devices.
- Aerospace & Marine – Aircraft components, shipbuilding, and propellers.
- Food Processing Industry – Industrial kitchen equipment and food storage tanks.
Stainless steel is ideal for applications requiring corrosion resistance and hygiene.
3. Carbon Steel
Composition: Iron + Carbon (up to 2.1%)
Properties: High tensile strength, durable, and cost-effective.
Uses:
- Pipelines and Bridges – Structural applications requiring high strength.
- Pressure Vessels – Gas cylinders, tanks, and boilers.
- Mechanical Parts – CNC machined components for industrial machinery.
Carbon steel is commonly used in heavy-duty applications due to its strength and affordability.
4. Cast Iron
Composition: Iron + Carbon (2% – 4%) + Silicon (1% – 3%)
Properties: High compressive strength, wear-resistant, and excellent heat retention.
Uses:
- Engine Blocks & Machine Tools – Durable and heat-resistant.
- Cookware – Cast iron pans and griddles for superior heat distribution.
- Pipes & Valves – Used in plumbing and wastewater systems.
Cast iron is valued for its durability and heat resistance in industrial and household applications.
5. Wrought Iron
Composition: Iron with very low carbon content (<0.08%)
Properties: Malleable, corrosion-resistant, and decorative.
Uses:
- Gates, Railings, and Fences – Durable and aesthetic appeal.
- Antique Furniture – Often used in vintage or artistic metalwork.
- Handcrafted Tools & Weapons – Used in blacksmithing.
Wrought iron is no longer produced on an industrial scale but is still used for artistic and decorative applications.
6. Alloy Steel
Composition: Iron + Carbon + Alloying Elements (Nickel, Manganese, Chromium, Molybdenum)
Properties: Enhanced strength, wear resistance, and corrosion resistance.
Uses:
- Automotive & Aerospace Components – Gears, shafts, and landing gear.
- Cutting Tools & Drill Bits – High-speed steel (HSS) for machining applications.
- Structural Engineering – Bridges, skyscrapers, and offshore drilling platforms.
Alloy steel combines the best properties of multiple metals, making it ideal for high-performance applications.
Conclusion: Choosing the Right Ferrous Metal
- Use Steel for general structural applications and industrial machinery.
- Choose Stainless Steel for corrosion resistance in medical, food, and marine industries.
- Opt for Cast Iron when durability and heat retention are required.
- Select Alloy Steel for high-performance automotive and aerospace applications.
- Use Wrought Iron for decorative or artistic metalwork.
Need precision CNC machining for ferrous metal components? Get a custom quote today!
Common Applications of Ferrous Metals
Ferrous metals are essential in manufacturing, engineering, and industrial applications due to their strength, durability, and affordability. From automotive parts to medical equipment, pressure vessels to turbine engine components, ferrous metals play a key role in various industries.
In this section, we explore the primary applications of ferrous metals, their functionality in different machinery and equipment, and the industries that rely on ferrous materials for high-performance solutions.
Applications of Ferrous Metals
Ferrous metals are used in applications requiring high tensile strength, heat resistance, and durability. Below is an in-depth look at some of their most common applications.
1. Bush Sleeves
- Bush sleeves (or bushings) are cylindrical components used to reduce friction and wear between moving parts in machinery and automotive applications.
- Commonly made from alloy steel or carbon steel, they provide shock absorption and load distribution.
- Used in gear systems, suspension mechanisms, and industrial machinery.
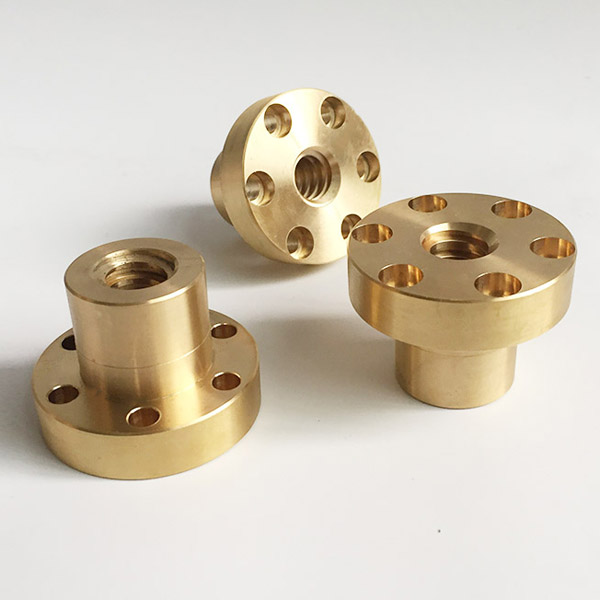
2. Heat Exchangers
- Heat exchangers transfer heat between two fluids without mixing them, used in HVAC systems, chemical plants, and power generation.
- Stainless steel is preferred for heat exchangers due to its corrosion resistance and thermal conductivity.
- Found in refrigeration systems, industrial furnaces, and steam turbines.
3. Pressure Vessels
- Pressure vessels store gases and liquids under high pressure, requiring strong, durable materials.
- Carbon steel and stainless steel are commonly used due to their high strength and resistance to extreme conditions.
- Found in chemical plants, power plants, and industrial processing facilities.
4. Calciners
- Calciners are used in the thermal processing of raw materials, such as cement, lime, and ores.
- High-strength ferrous metals like heat-resistant alloy steel withstand extreme temperatures in industrial kilns.
- Used in cement plants, chemical industries, and metal refining.
5. Centrifuges
- Centrifuges use rotational force to separate substances of different densities, commonly used in medical, pharmaceutical, and food processing industries.
- Stainless steel components ensure corrosion resistance and hygienic operation.
- Used in wastewater treatment, oil refining, and biopharmaceutical manufacturing.
6. Hydraulic Cylinders
- Hydraulic cylinders generate mechanical force using pressurized fluid, commonly used in heavy machinery, construction equipment, and industrial automation.
- Carbon steel and alloy steel ensure high load capacity and impact resistance.
- Found in excavators, cranes, and hydraulic presses.
7. Petrochemical Components
- The petrochemical industry requires durable, heat-resistant materials to withstand harsh environments and corrosive substances.
- Stainless steel and alloy steel are used in pipes, reactors, and storage tanks.
- Found in oil refineries, gas processing plants, and offshore drilling.
8. Chemical and Food Processing Equipment
- Food-grade stainless steel is used in mixers, conveyors, and storage tanks for its resistance to corrosion and ease of cleaning.
- Carbon and alloy steel are used in chemical reactors, pumps, and storage vessels.
- Found in dairy processing, beverage production, and pharmaceutical industries.
9. Pump and Valve Components
- Industrial pumps and valves handle high-pressure fluids, requiring strong, wear-resistant materials.
- Stainless steel and cast iron are commonly used due to their durability and chemical resistance.
- Used in power plants, water treatment, and industrial pipelines.
10. Pulp and Paper Suction Rolls
- Suction rolls are used in the papermaking process to remove water and shape paper sheets.
- Cast iron and stainless steel ensure high wear resistance and long lifespan.
- Used in paper mills and printing industries.
11. Turbine Engine Components
- Turbine engines in aircraft and power plants require high-temperature-resistant metals.
- Alloy steels and stainless steels ensure durability, corrosion resistance, and mechanical stability.
- Used in jet engines, power generation, and steam turbines.
12. Medical Equipment
- Stainless steel is widely used in surgical instruments, implants, and medical devices due to its biocompatibility and corrosion resistance.
- Found in hospital equipment, dental tools, and orthopedic implants.
13. Forming Rolls
- Forming rolls shape sheet metal in industrial manufacturing.
- High-speed steel and alloy steel provide durability and wear resistance.
- Used in automotive, aerospace, and heavy machinery manufacturing.
These applications highlight the versatility of ferrous metals in industries requiring strength, heat resistance, and longevity.
Application Industries for Ferrous Metals
1. Automotive Industry
- Used in engine components, suspension systems, gears, and axles.
- Stainless steel and alloy steel provide high strength and heat resistance.
2. Aerospace Industry
- Alloy steels and stainless steels are used in aircraft fuselages, landing gears, and turbine engines.
- Provides high strength-to-weight ratio and resistance to extreme conditions.
3. Construction & Infrastructure
- Carbon steel and reinforced steel are used in bridges, skyscrapers, and railway tracks.
- Offers load-bearing capacity and durability.
4. Energy and Power Generation
- Alloy steels are used in steam turbines, nuclear reactors, and wind turbines.
- Provides heat resistance and mechanical stability.
5. Medical and Pharmaceutical Industry
- Stainless steel is used in surgical tools, implants, and medical devices.
- Ensures biocompatibility and corrosion resistance.
6. Manufacturing and Heavy Machinery
- Cast iron, alloy steel, and carbon steel are used in machinery frames, cutting tools, and factory equipment.
- Provides shock resistance and durability.
7. Oil & Gas Industry
- Stainless steel and alloy steel are used in drilling equipment, pipelines, and refineries.
- Ensures corrosion resistance and high-pressure tolerance.
Ferrous metals are used in nearly every industry, proving their importance in modern manufacturing and infrastructure.
Conclusion: Why Ferrous Metals Are Essential in Industry
- Ferrous metals are the backbone of industrial manufacturing, offering high strength, durability, and versatility.
- Used in automotive, aerospace, medical, construction, and heavy machinery applications, ferrous metals provide structural integrity and long-term reliability.
- While ferrous metals require corrosion protection, their superior mechanical properties make them indispensable in engineering and CNC machining.
Looking for high-precision ferrous metal CNC machining? Contact us today for expert solutions!
What Are Non-Ferrous Metals?
Non-ferrous metals are metals that do not contain iron (Fe), making them lighter, more corrosion-resistant, and non-magnetic compared to ferrous metals. These metals are widely used in industries where lightweight, conductivity, and corrosion resistance are essential, such as aerospace, electronics, marine, and medical applications.
Unlike ferrous metals, non-ferrous metals are more malleable, easier to machine, and highly recyclable, making them an ideal choice for high-precision CNC machining parts.
Examples of non-ferrous metals include aluminum, copper, brass, zinc, titanium, silver, and gold.
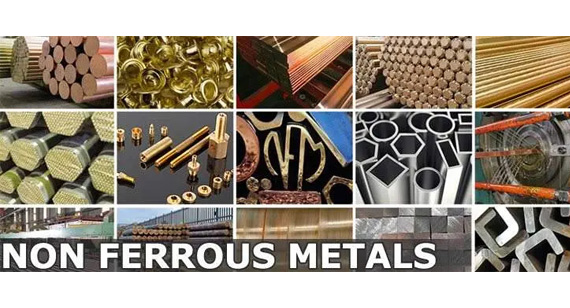
Advantages and Disadvantages of Non-Ferrous Metals
Non-ferrous metals offer several benefits over ferrous metals, including superior corrosion resistance, lightweight properties, and electrical conductivity. However, they also have certain drawbacks, such as lower strength and higher costs.
In this section, we will explore the key advantages and disadvantages of non-ferrous metals to help determine their best applications in CNC machining, manufacturing, and industrial use.
Advantages of Non-Ferrous Metals
1. Corrosion Resistance
- Non-ferrous metals do not rust because they lack iron (Fe), making them perfect for marine, aerospace, and outdoor applications.
- Aluminum, copper, brass, and titanium are highly resistant to oxidation, making them ideal for structural components exposed to harsh environments.
- Example: Aluminum is commonly used in aircraft bodies and marine vessels due to its corrosion resistance.
2. Lightweight Properties
- Non-ferrous metals are significantly lighter than ferrous metals, making them essential in aerospace, automotive, and portable electronic applications.
- Aluminum and titanium are widely used for high-strength, lightweight components in automotive and aerospace industries.
- Example: Aluminum car frames reduce vehicle weight and improve fuel efficiency.
3. High Electrical and Thermal Conductivity
- Copper and silver are among the best conductors of electricity, making them ideal for electrical wiring and electronic components.
- Aluminum is widely used in heat exchangers and radiators due to its superior heat dissipation properties.
- Example: Copper is used in electrical motors, while aluminum is used in cooling systems.
4. Non-Magnetic Properties
- Most non-ferrous metals are non-magnetic, making them ideal for applications where magnetism is a concern, such as electronic devices and precision instruments.
- Aluminum, copper, brass, and titanium are used in MRI machines, aerospace navigation systems, and sensitive electronic equipment.
5. High Malleability and Machinability
- Non-ferrous metals are easier to shape, bend, and machine than most ferrous metals, making them ideal for custom CNC machining and intricate designs.
- Brass and aluminum are commonly used in precision CNC machining, jewelry making, and artistic metalwork.
- Example: Brass is preferred for machining small, complex components like watch gears and musical instrument parts.
6. High Recyclability and Sustainability
- Non-ferrous metals are highly recyclable, reducing environmental impact and production costs.
- Aluminum and copper retain their properties after recycling, making them a sustainable choice for manufacturing and industrial use.
Non-ferrous metals provide superior corrosion resistance, lightweight properties, and excellent machinability, making them ideal for specialized applications.
Disadvantages of Non-Ferrous Metals
1. Lower Strength Compared to Ferrous Metals
- Non-ferrous metals are generally softer and less durable than ferrous metals like steel or cast iron.
- They are not suitable for heavy load-bearing applications, such as construction beams or industrial machine frames.
- However, titanium and some aluminum alloys offer excellent strength-to-weight ratios.
2. Higher Cost
- Non-ferrous metals are more expensive than most ferrous metals due to limited availability and complex refining processes.
- Copper, titanium, silver, and gold are significantly more costly than steel and iron.
- However, their superior properties often justify the higher price in specialized applications.
3. Susceptibility to Wear and Deformation
- Non-ferrous metals like aluminum and copper are softer than steel, making them more prone to scratches, dents, and wear over time.
- Brass and bronze alloys improve wear resistance but may still be weaker than hardened steels.
4. Lower Heat Resistance
- Some non-ferrous metals, such as aluminum and copper, have lower melting points than ferrous metals, making them less suitable for high-temperature applications.
- Titanium is an exception, as it maintains strength even at high temperatures.
5. Limited Availability for Certain Applications
- Certain non-ferrous metals, such as gold and platinum, are rare and expensive, limiting their widespread industrial use.
- They are primarily used in specialized applications like electronics, aerospace, and luxury goods.
While non-ferrous metals offer many advantages, they come with trade-offs in terms of strength, cost, and heat resistance.
Conclusion: When to Use Non-Ferrous Metals?
- Use non-ferrous metals when corrosion resistance, lightweight properties, and high conductivity are required.
- Choose aluminum or titanium for aerospace, automotive, and weight-sensitive applications.
- Use copper and brass for electrical wiring, plumbing, and decorative elements.
- Select non-ferrous metals for CNC machining projects that require high precision and custom designs.
Looking for precision CNC machining for non-ferrous metal components? Contact us today for expert solutions!
Properties of Non-Ferrous Metals
Non-ferrous metals are essential in modern engineering and manufacturing due to their lightweight nature, corrosion resistance, and excellent conductivity. These metals do not contain iron (Fe), making them ideal for aerospace, automotive, medical, and electronic applications where rust resistance and electrical properties are crucial.
Understanding the key properties of non-ferrous metals helps manufacturers determine which metal is best suited for CNC machining, industrial applications, and high-performance components.
Key Properties of Non-Ferrous Metals
1. Corrosion Resistance
- Non-ferrous metals are naturally resistant to rust and oxidation, making them perfect for marine, aerospace, and outdoor applications.
- Aluminum, brass, copper, and titanium resist moisture and chemical corrosion, extending their lifespan in harsh environments.
2. Lightweight
- Non-ferrous metals like aluminum, titanium, and magnesium are significantly lighter than steel or iron, reducing the overall weight of manufactured components.
- This property makes them ideal for aerospace, automotive, and portable electronic devices.
3. High Electrical and Thermal Conductivity
- Copper and silver are among the best electrical conductors, making them essential for wiring, circuit boards, and power transmission.
- Aluminum is widely used in heat exchangers and cooling systems due to its superior thermal conductivity.
4. Non-Magnetic Properties
- Most non-ferrous metals are non-magnetic, making them essential for precision instruments, MRI machines, and sensitive electronic equipment.
- Brass, aluminum, and copper are used in applications where magnetism needs to be avoided.
5. High Malleability and Machinability
- Non-ferrous metals are softer and more ductile than ferrous metals, making them easier to shape, machine, and form into complex parts.
- Brass and aluminum are widely used in custom CNC machining and precision manufacturing.
6. High Recyclability
- Non-ferrous metals can be recycled without losing their properties, making them an eco-friendly and sustainable choice for industrial applications.
- Aluminum and copper recycling significantly reduce energy consumption in manufacturing.
Non-ferrous metals are chosen for their corrosion resistance, lightweight properties, excellent conductivity, and ease of machining, making them ideal for specialized applications.
Examples and Uses of Non-Ferrous Metals
Non-ferrous metals have diverse applications across multiple industries, from aerospace and construction to electronics and medical devices. Their unique properties, such as rust resistance, conductivity, and lightweight strength, make them critical materials for modern technology and engineering.
Below are some of the most commonly used non-ferrous metals and their applications.
Common Non-Ferrous Metals and Their Applications
1. Aluminum (Al)
- Lightweight, corrosion-resistant, and highly conductive.
- Easily machinable and used in CNC machining, aerospace, and automotive applications.
Uses:
- Aerospace Industry – Aircraft frames, fuselage components, and wing structures.
- Automotive Industry – Lightweight car bodies, wheels, and engine blocks.
- Electronics – Heat sinks, laptop casings, and smartphone frames.
- Construction – Window frames, roofing materials, and structural panels.
Aluminum is the go-to choice for lightweight, corrosion-resistant CNC machining applications.
2. Copper (Cu)
- Best electrical conductor after silver, making it essential for wiring and electronics.
- Excellent heat conductivity and corrosion resistance.
Uses:
- Electrical Industry – Wiring, electrical motors, power grids, and transformers.
- Plumbing – Pipes, fittings, and water supply systems.
- HVAC Systems – Air conditioning coils and heat exchangers.
- CNC Machining – High-precision components for aerospace and electronics.
Copper is preferred for its electrical and thermal conductivity in power transmission and precision machining.
3. Lead (Pb)
- Soft, dense, and corrosion-resistant.
- Excellent radiation shielding properties.
Uses:
- Battery Manufacturing – Lead-acid batteries for automobiles and industrial power backup.
- Radiation Shielding – Medical X-ray protection and nuclear shielding.
- Construction – Roofing materials and waterproofing applications.
Lead is primarily used for its high density, radiation shielding, and corrosion resistance.
4. Tin (Sn)
- Non-toxic, corrosion-resistant, and often used as a protective coating.
- Highly malleable and used in soldering applications.
Uses:
- Electronics – Soldering materials for circuit boards and electrical connections.
- Food Packaging – Tin plating in cans for food preservation.
- Anti-Corrosion Coatings – Used in steel plating to prevent rust.
Tin is widely used in electronics and as a corrosion-resistant coating for food packaging.
5. Silver (Ag)
- Best electrical conductor of all metals.
- Naturally antimicrobial, making it useful for medical applications.
Uses:
- Electronics – High-performance circuit boards and semiconductor components.
- Medical Applications – Antibacterial coatings for medical instruments and implants.
- Jewelry and Luxury Goods – Rings, watches, and silverware.
Silver is essential in electronics, medical applications, and high-end jewelry.
6. Brass (Copper + Zinc Alloy)
- Stronger than pure copper, corrosion-resistant, and highly machinable.
- Attractive golden appearance, making it ideal for decorative applications.
Uses:
- Musical Instruments – Trumpets, saxophones, and trombones.
- Plumbing Fixtures – Fittings, valves, and connectors.
- Aerospace and Marine Applications – Bearings, gears, and bushings.
- CNC Machining – Precision parts for industrial machinery and automotive components.
Brass is valued for its durability, machinability, and corrosion resistance in high-performance applications.
7. Gold (Au)
- High corrosion resistance, excellent electrical conductivity, and non-reactive.
- Used in high-end electronics and luxury goods.
Uses:
- Electronics – Circuit boards, connectors, and semiconductor applications.
- Jewelry and Watches – High-end accessories and gold-plated components.
- Medical Industry – Implants, dental crowns, and cancer treatment technology.
Gold is widely used for its conductivity, corrosion resistance, and luxurious appearance.
8. Zinc (Zn)
- Essential in galvanizing steel for rust prevention.
- High corrosion resistance and used in die-casting applications.
Uses:
- Galvanization – Coating steel and iron to prevent rust.
- Die-Casting – Automotive and industrial parts.
- Battery Components – Zinc-air and alkaline batteries.
Zinc is primarily used to enhance the durability and longevity of steel through galvanization.
Conclusion: Choosing the Right Non-Ferrous Metal
- Use aluminum for lightweight, high-strength applications in aerospace and automotive industries.
- Choose copper for electrical and thermal conductivity in electronics and power grids.
- Select brass for corrosion resistance, machinability, and decorative applications.
- Opt for silver or gold in high-end electronics, medical devices, and jewelry.
- Use zinc for protective coatings and die-casting applications.
Looking for precision CNC machining for non-ferrous metal components? Contact us today for expert solutions!
Common Applications of Non-Ferrous Metals
Non-ferrous metals play a critical role in modern manufacturing, engineering, and CNC machining due to their corrosion resistance, lightweight properties, and high conductivity. They are widely used in high-performance industries such as aerospace, automotive, medical, electronics, and marine applications, where durability, precision, and reliability are essential.
This section explores the key applications of non-ferrous metals, focusing on bushings, bearings, gears, sleeves, wear rings, and pump and valve parts, followed by an overview of major industries that rely on non-ferrous materials.
Applications of Non-Ferrous Metals
1. Bushings
- Bushings reduce friction and wear between moving components in machinery.
- Non-ferrous materials like bronze, brass, and aluminum are preferred because they resist corrosion, wear, and deformation.
- Used in automotive suspension systems, aerospace landing gear, hydraulic machinery, and industrial presses.
Bushings made from non-ferrous metals offer long-lasting performance in high-load, high-temperature environments.
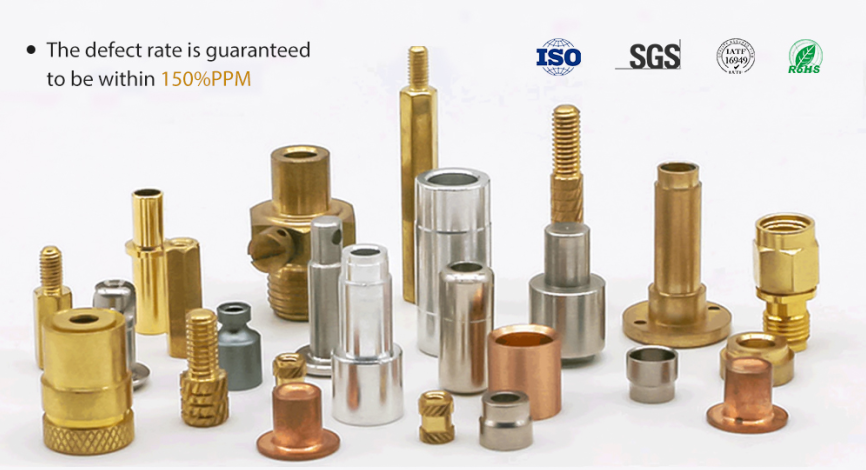
2. Bearings
- Bearings facilitate smooth rotational movement in mechanical systems.
- Brass, bronze, and aluminum bearings provide low friction, heat dissipation, and corrosion resistance.
- Found in electric motors, automotive engines, turbines, conveyor systems, and aircraft landing gear.
Non-ferrous bearings are essential for reducing wear and improving efficiency in industrial and automotive applications.
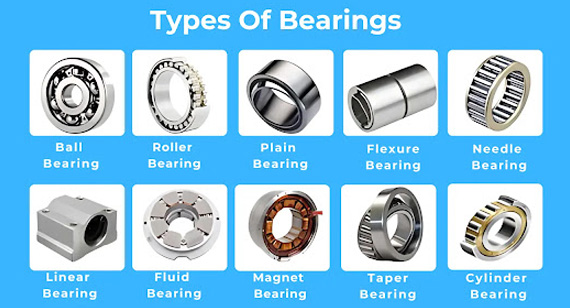
3. Gears
- Gears transmit mechanical power in machinery and require high durability, low friction, and resistance to wear.
- Brass, bronze, and aluminum gears are used in precision instruments, marine applications, and aerospace components.
- Common in industrial gear systems, automotive transmissions, medical devices, and clock mechanisms.
Non-ferrous gears enhance efficiency and longevity in precision engineering applications.
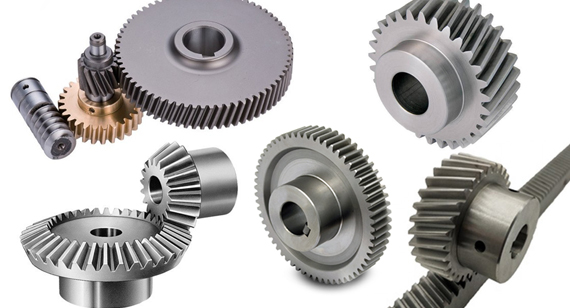
4. Sleeves
- Sleeves protect rotating or sliding shafts from wear, reducing maintenance needs.
- Non-ferrous sleeves made of aluminum, copper, and bronze resist heat, corrosion, and impact.
- Used in hydraulic systems, industrial pumps, marine engines, and aerospace actuators.
Non-ferrous sleeves improve mechanical durability while preventing excessive shaft wear.
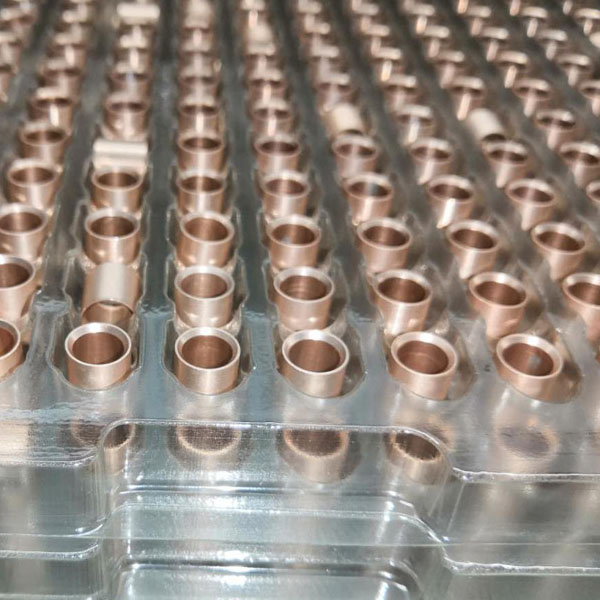
5. Wear Rings
- Wear rings reduce friction between components in high-speed rotating systems.
- Brass, bronze, and titanium wear rings ensure precision, efficiency, and wear resistance.
- Used in turbines, compressors, pumps, and industrial rotating equipment.
Non-ferrous wear rings enhance efficiency and extend the lifespan of rotating machinery.
6. Pump and Valve Parts
- Pump and valve parts control the flow of liquids and gases in industrial, medical, and energy sectors.
- Non-ferrous metals like brass, bronze, aluminum, and titanium resist chemical corrosion, pressure, and temperature extremes.
- Found in water treatment plants, oil and gas pipelines, medical devices, and hydraulic systems.
Non-ferrous pump and valve parts ensure reliability and longevity in fluid control applications.
Application Industries for Non-Ferrous Metals
Non-ferrous metals are essential in various industries where lightweight materials, corrosion resistance, and high precision are required.
1. Aerospace Industry
- Aluminum and titanium are widely used in aircraft components, fuselage parts, and structural frames due to their lightweight and high strength.
- Copper and brass are used in electrical wiring and avionics systems.
Non-ferrous metals help reduce aircraft weight, improve fuel efficiency, and enhance structural integrity.
2. Automotive Industry
- Aluminum is extensively used in vehicle frames, wheels, and engine blocks to reduce weight and increase efficiency.
- Brass and bronze are used in gears, bushings, and electrical connectors.
Non-ferrous metals improve fuel economy, durability, and corrosion resistance in modern automobiles.
3. Medical and Pharmaceutical Industry
- Titanium and stainless steel are used for medical implants, surgical tools, and prosthetics due to their biocompatibility and strength.
- Silver and copper provide antimicrobial properties for medical instruments and hospital equipment.
Non-ferrous metals enhance hygiene, precision, and safety in medical applications.
4. Electronics and Electrical Industry
- Copper and silver are essential for electrical wiring, circuit boards, and power transmission systems due to their high conductivity.
- Aluminum is used in heat sinks, connectors, and LED lighting components.
Non-ferrous metals improve electrical efficiency, thermal management, and reliability in electronic devices.
5. Marine Industry
- Brass, bronze, and aluminum are used in shipbuilding, propellers, and marine fittings due to their corrosion resistance in saltwater environments.
- Titanium is used in deep-sea exploration equipment for its strength and durability.
Non-ferrous metals ensure longevity and performance in harsh marine conditions.
6. Construction and Architecture
- Aluminum and copper are used for roofing, facades, window frames, and decorative elements due to their aesthetic appeal and corrosion resistance.
- Brass and bronze are commonly used in ornamental fixtures and plumbing systems.
Non-ferrous metals provide architectural durability, sustainability, and a modern aesthetic.
7. Energy and Power Generation
- Copper is essential in power grids, wind turbines, and electrical substations.
- Aluminum is used in high-voltage power transmission lines for its lightweight properties.
Non-ferrous metals improve energy efficiency and reliability in power systems.
8. Industrial Machinery and Heavy Equipment
- Brass, bronze, and aluminum components are used in CNC machining, robotic automation, and hydraulic machinery.
- Titanium and high-performance alloys are used in industrial cutting tools and wear-resistant coatings.
Non-ferrous metals enhance durability and efficiency in industrial production.
Conclusion: Why Non-Ferrous Metals Are Essential in Modern Industries
- Non-ferrous metals provide corrosion resistance, lightweight properties, and excellent conductivity, making them vital for high-performance industries.
- Used in aerospace, automotive, medical, and electronics sectors, these metals improve efficiency, durability, and safety.
- For CNC machining, non-ferrous metals offer high precision and superior machinability for complex components.
Looking for expert CNC machining services for non-ferrous metal components? Contact us today for precision manufacturing solutions!
Comparison of the Properties of Ferrous and Non-Ferrous Metals
Ferrous and non-ferrous metals play critical roles in modern manufacturing, construction, and engineering. While ferrous metals are strong, durable, and magnetic, non-ferrous metals offer corrosion resistance, lightweight properties, and high conductivity. Choosing between ferrous and non-ferrous metals depends on factors such as rust resistance, machinability, weight, and cost.
This section provides a detailed comparison of their key properties, followed by a tabular representation for easy reference.
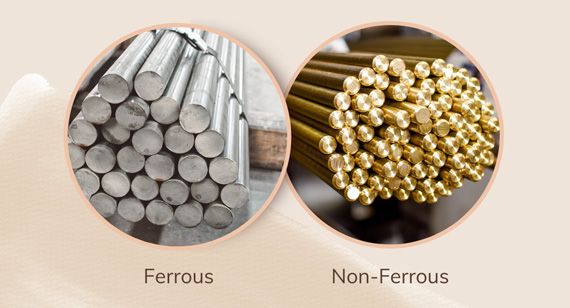
Key Property Comparisons
1. Iron Content
- Ferrous metals contain iron (Fe), which gives them high strength and magnetism but makes them prone to rust.
- Non-ferrous metals do not contain iron, which enhances their corrosion resistance and lightweight properties.
2. Rust and Corrosion Resistance
- Ferrous metals, except stainless steel, are highly prone to rust and oxidation when exposed to moisture.
- Non-ferrous metals resist rust naturally, making them ideal for marine, aerospace, and outdoor applications.
3. Magnetism
- Most ferrous metals are magnetic, making them suitable for motors, transformers, and power tools.
- Non-ferrous metals are non-magnetic, making them essential in electronics, medical equipment, and aerospace navigation systems.
4. Corrosion Sensitivity
- Ferrous metals require protective coatings (galvanization, painting, or plating) to resist corrosion.
- Non-ferrous metals like aluminum, copper, and titanium naturally resist oxidation, reducing maintenance costs.
5. Density
- Ferrous metals are generally denser and heavier, making them ideal for structural applications.
- Non-ferrous metals are lightweight, improving fuel efficiency and portability in automotive and aerospace applications.
6. Strength and Durability
- Ferrous metals (especially carbon steel and alloy steel) have high tensile strength, making them ideal for construction and heavy machinery.
- Non-ferrous metals like aluminum and titanium have excellent strength-to-weight ratios, allowing for lighter yet durable structures.
7. Weight
- Ferrous metals are heavier, limiting their use in weight-sensitive applications.
- Non-ferrous metals are significantly lighter, making them essential in aerospace, transportation, and consumer electronics.
8. Cost
- Ferrous metals are cheaper and widely available, making them cost-effective for mass production.
- Non-ferrous metals, especially titanium, copper, and gold, are more expensive due to their rarity and specialized applications.
9. Recycling
- Both ferrous and non-ferrous metals are recyclable, but non-ferrous metals (aluminum, copper) retain their properties better after recycling.
- Ferrous metals are more widely recycled, contributing to sustainable manufacturing.
Comparison Table: Ferrous vs. Non-Ferrous Metals
Property |
Ferrous Metals |
Non-Ferrous Metals |
Iron Content |
Contains iron (Fe) |
Does not contain iron (Fe) |
Rust Resistance |
Prone to rust (except stainless steel) |
Highly resistant to rust and oxidation |
Corrosion Sensitivity |
Requires coatings for protection |
Naturally corrosion-resistant
|
Magnetism |
Magnetic (except stainless steel and some alloys) |
Non-magnetic (except nickel-based alloys) |
Density |
Generally high density and heavier |
Lighter and lower density |
Strength |
High tensile strength and durability |
Strength varies (titanium and brass offer high strength) |
Weight |
Heavier, making transportation more costly |
Lightweight, ideal for portable applications |
Cost |
Cheaper and widely available |
More expensive due to rarity and refining processes |
Recyclability |
Widely recycled but may degrade in quality |
Highly recyclable with minimal degradation |
Common Applications |
Construction, heavy machinery, tools, automotive parts |
Aerospace, electronics, marine, medical, jewelry |
Conclusion: Choosing Between Ferrous and Non-Ferrous Metals
- Use ferrous metals when high strength, durability, and cost-efficiency are required, such as in construction, bridges, and industrial machinery.
- Choose non-ferrous metals for applications needing corrosion resistance, lightweight properties, and high conductivity, such as aerospace, electronics, and medical equipment.
- Both ferrous and non-ferrous metals are recyclable, making them sustainable choices for various industries.
Need high-precision CNC machining for ferrous or non-ferrous metals? Contact us for expert solutions today!
Why Is It Important Whether the Metal Contains Iron?
The presence of iron (Fe) in a metal significantly affects its strength, durability, corrosion resistance, and magnetic properties. This distinction is crucial for engineering, manufacturing, and CNC machining, where choosing the right material impacts performance, longevity, and cost-efficiency.
Understanding why iron content matters helps industries select materials that best suit construction, aerospace, automotive, electronics, and medical applications.
Key Reasons Why Iron Content Matters
1. Corrosion and Rust Resistance
- Ferrous metals, except stainless steel, are prone to rust when exposed to moisture and oxygen.
- Non-ferrous metals like aluminum, copper, and brass naturally resist oxidation, making them ideal for marine, aerospace, and outdoor environments.
2. Magnetic Properties
- Iron-based metals are magnetic, making them essential for motors, transformers, and electrical components.
- Non-ferrous metals are non-magnetic, making them ideal for electronic devices, MRI machines, and aerospace applications.
3. Strength and Load-Bearing Capacity
- Ferrous metals (especially carbon steel and alloy steel) are incredibly strong, making them suitable for structural applications, bridges, and heavy machinery.
- Non-ferrous metals, like titanium and aluminum, offer a high strength-to-weight ratio, making them valuable in aviation, automotive, and precision engineering.
4. Weight Considerations
- Ferrous metals are typically denser and heavier, increasing transportation costs and limiting their use in weight-sensitive industries.
- Non-ferrous metals are lighter, improving fuel efficiency and ease of handling in automotive and aerospace applications.
5. Conductivity and Heat Resistance
- Non-ferrous metals like copper and silver have superior electrical conductivity, making them crucial for wiring, circuit boards, and power transmission.
- Aluminum and copper have excellent thermal conductivity, making them ideal for radiators, heat sinks, and cooling systems.
Iron content affects corrosion resistance, magnetism, strength, and weight, making it a critical factor in material selection for different industries.
Why Isn't Every Metal That Contains Iron Ferrous?
While the presence of iron (Fe) is the defining characteristic of ferrous metals, some iron-containing alloys are classified as non-ferrous due to their unique properties, composition, and applications.
This section explains why certain iron-containing metals are not considered ferrous and how their chemical structure and alloying elements influence their classification.
Key Reasons Why Some Iron-Containing Metals Are Not Considered Ferrous
1. Alloy Composition
- Ferrous metals primarily contain iron as the main element (e.g., carbon steel, stainless steel, cast iron).
- Some alloys contain iron but are dominated by non-ferrous metals, such as nickel-based superalloys, cobalt alloys, and specific titanium alloys.
2. Corrosion Resistance and Rust Prevention
- Stainless steel (which contains iron) is highly resistant to rust, thanks to its high chromium content (at least 10.5%).
- Nickel and cobalt-based alloys with iron are engineered for extreme corrosion resistance, making them more similar to non-ferrous materials in function.
3. Magnetic Properties
- Ferrous metals are typically magnetic, but some iron-containing alloys (such as austenitic stainless steel) are non-magnetic due to their crystalline structure.
- Nickel and cobalt-based superalloys, despite containing iron, behave more like non-ferrous metals in applications such as aerospace and medical implants.
Not all iron-containing metals are classified as ferrous due to differences in alloy composition, corrosion resistance, and magnetism.
When Did Ferrous and Non-Ferrous Metals Begin to Be Used?
The history of metal use dates back thousands of years, shaping civilizations, technological advancements, and industrial progress. The distinction between ferrous and non-ferrous metals has evolved based on material properties, availability, and application needs.
Understanding when and how ferrous and non-ferrous metals began to be used helps us appreciate their impact on modern engineering and CNC machining.
Historical Timeline of Ferrous and Non-Ferrous Metal Use
1. Early Use of Non-Ferrous Metals (6000 BCE – 1000 BCE)
- Copper was one of the first metals used by ancient civilizations (around 6000 BCE) for tools, weapons, and decorative items.
- Gold and silver were highly valued for jewelry and currency due to their natural beauty and corrosion resistance.
- Bronze (an alloy of copper and tin) led to the Bronze Age (3300 BCE – 1200 BCE), revolutionizing weaponry, tools, and construction materials.
2. The Rise of Ferrous Metals (1200 BCE – 500 CE)
- The Iron Age (starting around 1200 BCE) marked the widespread use of iron and steel, replacing bronze in tools and weaponry due to their superior strength and durability.
- By the Roman era (500 BCE – 500 CE), ferrous metals were extensively used for weapons, armor, infrastructure, and construction.
3. The Industrial Revolution and Steel Advancements (18th – 19th Century)
- The Industrial Revolution (1750–1850) saw a massive increase in steel production, enabling advancements in railroads, bridges, skyscrapers, and heavy machinery.
- Cast iron and wrought iron became dominant materials for industrial infrastructure, revolutionizing manufacturing.
4. The 20th Century: Aerospace, Electronics, and High-Performance Alloys
- The 1900s saw advancements in aluminum, titanium, and stainless steel, enabling innovations in aviation, automotive, and medical industries.
- Copper and aluminum became essential for electrical wiring and power transmission.
- Nickel-based superalloys and titanium alloys became crucial for space exploration and high-performance engineering.
5. The 21st Century: CNC Machining and Advanced Metal Applications
- Modern CNC machining allows for ultra-precise manufacturing of both ferrous and non-ferrous metal components, enabling custom fabrication for aerospace, medical devices, and industrial machinery.
- Sustainable manufacturing prioritizes recyclable non-ferrous metals, reducing environmental impact.
Ferrous metals became dominant in the Iron Age, while non-ferrous metals shaped early civilizations and continue to be essential in modern industries.
Conclusion: The Importance of Ferrous and Non-Ferrous Metals
- Ferrous metals offer high strength and durability, making them ideal for construction, automotive, and heavy machinery.
- Non-ferrous metals provide corrosion resistance, lightweight properties, and electrical conductivity, making them essential for electronics, aerospace, and medical applications.
- The historical evolution of metal use has shaped industrial progress, with CNC machining enabling precision manufacturing for both ferrous and non-ferrous metals.
Looking for expert CNC machining services for ferrous or non-ferrous metal components? Contact us today for precision manufacturing solutions!
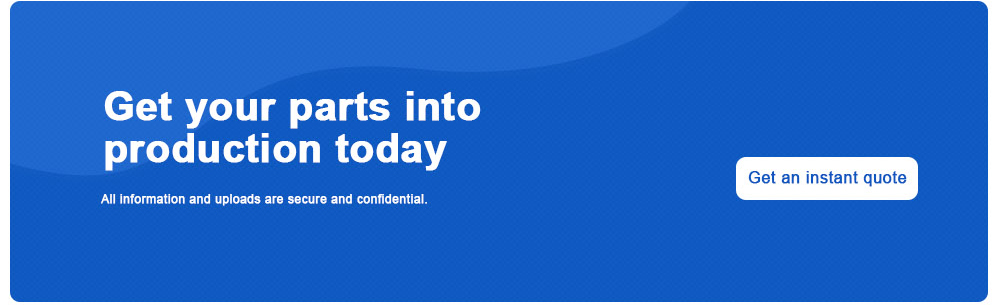
Frequently Asked Questions (FAQs) About Ferrous and Non-Ferrous Metals
Are Ferrous Metals Stronger Than Non-Ferrous Metals?
- Ferrous metals are generally stronger and more durable than non-ferrous metals, particularly carbon steel and alloy steel.
- However, certain non-ferrous metals like titanium and some aluminum alloys have high strength-to-weight ratios, making them suitable for aerospace and high-performance applications.
Ferrous metals are typically stronger, but some non-ferrous metals offer strength with lightweight properties.
Is Stainless Steel a Ferrous or Non-Ferrous Metal?
- Stainless steel is a ferrous metal because it contains iron (Fe).
- However, stainless steel resists rust better than other ferrous metals due to its high chromium (Cr) content.
- Some stainless steels (like austenitic grades) are non-magnetic, while others (like ferritic and martensitic grades) are magnetic.
Stainless steel is ferrous but has enhanced corrosion resistance compared to traditional ferrous metals.
Is Copper a Ferrous or Non-Ferrous Metal?
- Copper is a non-ferrous metal because it does not contain iron (Fe).
- It is widely used for electrical wiring, plumbing, and heat exchangers due to its high conductivity and corrosion resistance.
Copper is non-ferrous and valued for its excellent electrical and thermal conductivity.
Is Gold a Ferrous or Non-Ferrous Metal?
- Gold is a non-ferrous metal because it does not contain iron (Fe).
- It is used in electronics, jewelry, and high-end industrial applications due to its resistance to corrosion and oxidation.
Gold is a non-ferrous metal with high conductivity and corrosion resistance.
Is Iron a Ferrous or Non-Ferrous Metal?
- Iron is a ferrous metal because it is the primary element in all ferrous alloys like steel and cast iron.
- It is widely used for construction, automotive parts, and machinery due to its high strength and durability.
Iron is a ferrous metal and the foundation of all ferrous alloys.
Is Steel a Ferrous or Non-Ferrous Metal?
- Steel is a ferrous metal because it is primarily composed of iron (Fe).
- Different types of steel (carbon steel, stainless steel, and alloy steel) have varying properties depending on their carbon and alloy content.
Steel is a ferrous metal and one of the most widely used materials in industrial applications.
Which Metals Are Ferrous?
Common ferrous metals include:
- Iron (Fe)
- Carbon Steel
- Stainless Steel
- Cast Iron
- Wrought Iron
- Tool Steel
Ferrous metals contain iron and are known for their strength and durability.
Which Metals Are Non-Ferrous?
Common non-ferrous metals include:
- Aluminum (Al)
- Copper (Cu)
- Brass (Cu-Zn Alloy)
- Bronze (Cu-Sn Alloy)
- Zinc (Zn)
- Titanium (Ti)
- Nickel (Ni)
- Lead (Pb)
- Gold (Au)
- Silver (Ag)
Non-ferrous metals do not contain iron and are used for corrosion resistance, conductivity, and lightweight applications.
What Is the Main Difference Between Ferrous and Non-Ferrous Metals?
- Ferrous metals contain iron (Fe), making them stronger but more prone to rust.
- Non-ferrous metals do not contain iron and are more resistant to corrosion but usually softer and lighter.
The primary difference is the presence of iron, affecting properties like strength, rust resistance, and magnetism.
What Are the 5 Types of Non-Ferrous Metals?
The five most commonly used non-ferrous metals are:
- Aluminum – Lightweight, corrosion-resistant, used in aerospace and automotive.
- Copper – High electrical conductivity, used in wiring and plumbing.
- Brass – Strong, corrosion-resistant, used in fittings and instruments.
- Zinc – Used in galvanization to protect steel from rust.
- Titanium – High strength-to-weight ratio, used in aerospace and medical implants.
Non-ferrous metals are diverse and used in various industries based on their unique properties.
What Is the Difference Between Ferrous Stainless Steel and Non-Ferrous Stainless Steel?
- All stainless steel contains iron (Fe), making it a ferrous metal.
- However, some stainless steel grades (like austenitic stainless steel) are non-magnetic due to their crystalline structure.
- Stainless steel is corrosion-resistant due to high chromium (Cr) content but is still classified as a ferrous metal.
Stainless steel is ferrous but has properties that make it more resistant to corrosion than regular steel.
What Are the Three Types of Ferrous Metals?
The three primary types of ferrous metals are:
- Carbon Steel – Used in construction, machinery, and automotive industries.
- Stainless Steel – Corrosion-resistant, used in medical, food processing, and marine applications.
- Cast Iron – Used in heavy machinery, cookware, and engine components.
Ferrous metals are categorized based on their carbon content and alloying elements.
How Do You Tell If a Metal Contains Iron?
- Use a magnet: If the metal is magnetic, it likely contains iron (Fe).
- Check for rust: Ferrous metals (except stainless steel) rust when exposed to moisture.
- Perform a spark test: Grinding ferrous metals produces bright, long sparks, while non-ferrous metals produce minimal or no sparks.
Simple tests like magnetism, rust, and spark tests can determine iron content in metals.
Is Aluminum a Ferrous Metal?
- No, aluminum is a non-ferrous metal because it does not contain iron (Fe).
- It is lightweight, corrosion-resistant, and widely used in aerospace, automotive, and electronics industries.
Aluminum is non-ferrous and valued for its lightweight and corrosion resistance.
How Do You Detect Non-Ferrous Metals?
- Use a magnet: Non-ferrous metals are not magnetic.
- Conduct a density test: Non-ferrous metals like aluminum and titanium are lighter than steel.
- Perform an electrical conductivity test: Copper and silver have high conductivity, distinguishing them from ferrous metals.
Non-ferrous metals are detected using magnetism, density, and conductivity tests.
How Do You Identify Metal Types?
- Magnet Test: Ferrous metals are magnetic; non-ferrous metals are not.
- Spark Test: Ferrous metals produce bright, long sparks when ground.
- Weight Test: Non-ferrous metals are lighter than ferrous metals.
- Rust Observation: Ferrous metals rust; non-ferrous metals resist corrosion.
A combination of tests helps accurately identify different metals.
How Do You Identify Non-Metals?
- Non-metals do not conduct electricity or heat well (e.g., sulfur, carbon, and phosphorus).
- They are usually brittle and lack metallic luster.
- Unlike metals, non-metals cannot be shaped or machined easily.
Non-metals are primarily used in insulation, semiconductors, and chemical applications.
What Is the Difference Between Ferrous and Non-Ferrous Metal Blades?
- Ferrous metal blades (like carbon steel) are stronger but more prone to rust.
- Non-ferrous metal blades (like titanium or ceramic-coated blades) are corrosion-resistant and lightweight.
Non-ferrous metal blades offer rust resistance, while ferrous metal blades provide higher strength.
Looking for custom CNC machining services for ferrous and non-ferrous metals? Contact us today for precision manufacturing solutions!