Imagine pouring your heart and soul into designing a groundbreaking product, only to realize that its first prototype is riddled with flaws, leading to costly delays and frustrated stakeholders. This scenario is all too common in the world of industrial design, where the gap between concept and execution can make or break a product’s success. The frustration of iterating through multiple prototypes without achieving the desired outcome can stifle innovation, delay market entry, and erode profit margins. However, there is a strategic approach that can transform this daunting challenge into a streamlined, efficient process: mastering the fundamentals of Industrial Design Prototyping. By understanding the core principles, utilizing advanced techniques, and leveraging expert CNC machining services, you can create prototypes that not only meet but exceed expectations, paving the way for successful product launches and sustained market success.
Industrial Design Prototyping involves creating tangible models of product designs to evaluate functionality, aesthetics, and feasibility before mass production. Utilizing methods such as CNC machining, 3D printing, and vacuum casting, this process streamlines design validation, reduces production costs, and ensures that prototypes accurately reflect the final product's quality and performance standards.
Understanding the fundamental concepts and methodologies of industrial design prototyping is just the beginning. To fully harness the power of prototyping, it is essential to explore its various applications, benefits, and the advanced techniques that can elevate your product development process. Let’s delve deeper into what industrial design prototypes are, their purposes, and how you can effectively implement prototyping strategies to achieve exceptional product outcomes.
Preface
In the competitive landscape of industrial design, the ability to translate innovative ideas into functional and aesthetically pleasing products is paramount. Industrial design prototypes serve as the critical bridge between concept and production, enabling designers and manufacturers to test, refine, and perfect their creations before committing to large-scale manufacturing. This basic guide provides a comprehensive overview of industrial design prototyping, covering its definition, purposes, common methods, benefits, and applications across various industries. Whether you are a seasoned designer or new to the field, understanding the nuances of prototyping is essential for developing successful and market-ready products.
What is an Industrial Design Prototype?
Industrial Design Prototype Definition
An industrial design prototype is a preliminary model or sample of a product created to evaluate its design, functionality, and feasibility before proceeding to mass production. It serves as a tangible representation of the product concept, allowing designers, engineers, and stakeholders to interact with and assess the product’s features, ergonomics, and overall design aesthetics. Prototypes can range from simple mock-ups to highly functional models that closely resemble the final product in terms of materials, dimensions, and performance capabilities.
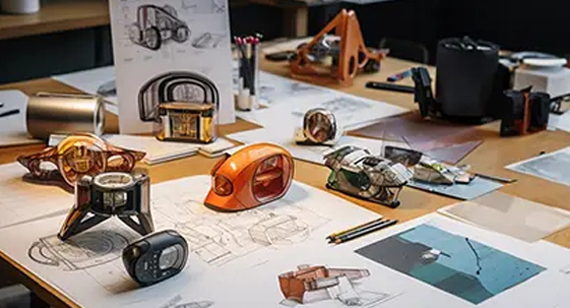
Key Characteristics of Industrial Design Prototypes
- Tangible Representation: Prototypes provide a physical form of the product, enabling hands-on evaluation and interaction.
- Functional Testing: They allow for the testing of the product’s functionality, ensuring that it performs as intended under real-world conditions.
- Design Validation: Prototypes help in validating design decisions, identifying any flaws or areas for improvement before finalizing the design.
- Stakeholder Communication: They facilitate better communication and understanding among team members, investors, and potential customers by providing a clear visual and functional representation of the product.
Role in Product Development
Industrial design prototypes play a crucial role in the product development lifecycle by serving as the first physical manifestation of a product idea. They enable iterative testing and refinement, allowing designers to make informed decisions based on real-world feedback and performance data. This iterative process helps in minimizing risks, reducing costs associated with design changes during later stages of production, and ensuring that the final product meets both aesthetic and functional requirements.
What is the Purpose of the Prototype in Industrial Design?
Prototyping is an indispensable step in the industrial design process, serving multiple purposes that collectively enhance the quality and viability of the final product. By creating prototypes, designers can explore design concepts, test functionalities, gather user feedback, and validate their ideas before moving to full-scale production. This foundational step ensures that the product not only meets the intended specifications but also aligns with market demands and user expectations.
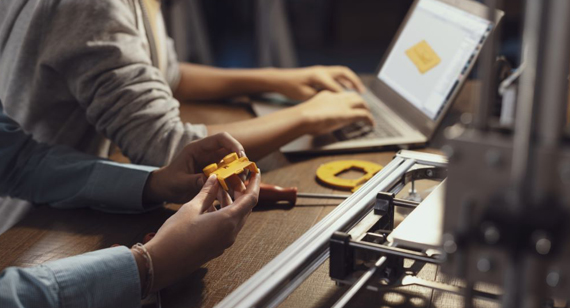
Mainly Used Prototypes
Prototypes in industrial design come in various forms, each serving a specific purpose in the product development process. Understanding the different types of prototypes and their applications is essential for selecting the right approach based on your project’s objectives and requirements. The primary types of prototypes used in industrial design include proof of concept, visual prototypes, working prototypes, and pre-production prototypes or factory samples.
Proof of Concept
A proof of concept (PoC) prototype is created to demonstrate the feasibility of a product idea or a specific aspect of its design. This type of prototype focuses on verifying that the core idea is viable and can be translated into a functional product.
Characteristics:
- Basic Functionality: PoC prototypes often include minimal features necessary to demonstrate the concept.
- Low Cost: They are usually inexpensive and quick to produce, allowing for rapid testing of ideas.
- Limited Aesthetics: The primary focus is on functionality rather than visual design.
Applications:
Feasibility Studies: Assessing whether a particular design or technology can be implemented effectively.
Innovation Testing: Exploring new ideas and innovations without significant investment.
Visual Prototype
A visual prototype, also known as a mock-up, emphasizes the aesthetic aspects of a product. It provides a realistic representation of the product’s appearance, including shape, color, texture, and overall design, without necessarily incorporating full functionality.
Characteristics:
- Aesthetic Focus: Highlights the visual design elements of the product.
- Non-Functional: May not include working components or operational features.
- High Detail: Often includes fine details to accurately represent the final product’s look and feel.
Applications:
- Design Validation: Evaluating the visual appeal and ergonomic design of the product.
- Stakeholder Presentations: Showcasing the product concept to investors, partners, and potential customers.
Working Prototype
A working prototype is a fully functional model of the product that demonstrates its core functionalities and operational capabilities. Unlike visual prototypes, working prototypes are designed to mimic the actual performance and usability of the final product.
Characteristics:
- Functional Representation: Replicates the intended functions and operations of the final product.
- Performance Testing: Allows for the assessment of the product’s performance, efficiency, and reliability.
- Iterative Refinement: Facilitates the identification and resolution of functional flaws and design inefficiencies through testing and feedback.
Applications:
- Engineering Validation: Testing the mechanical and technical aspects of the product.
- User Experience Testing: Evaluating how users interact with the product and identifying areas for improvement.
Pre-production Prototype or Factory Sample
A pre-production prototype, also known as a factory sample, is the final prototype created before mass production begins. It closely resembles the final product in terms of materials, dimensions, and performance, ensuring that the design is fully optimized for manufacturing.
Characteristics:
- High Fidelity: Closely matches the final product in terms of appearance and functionality.
- Manufacturing Readiness: Designed to identify any last-minute adjustments needed before full-scale production.
- Quality Assurance: Ensures that the product meets all quality and performance standards required for market release.
Applications:
- Final Testing: Conducting thorough testing to confirm that the product is ready for mass production.
- Production Setup: Finalizing manufacturing processes and tooling based on the pre-production prototype.
3 Methods of Industrial Design Prototyping
Industrial design prototyping encompasses a variety of methods, each suited to different stages of product development and specific project needs. The choice of prototyping method can significantly impact the efficiency, cost, and quality of the final prototype. Three widely recognized methods in industrial design prototyping are iterative prototyping, concurrent prototyping, and rapid prototyping. Each method offers unique advantages and can be strategically employed to enhance the prototyping process.
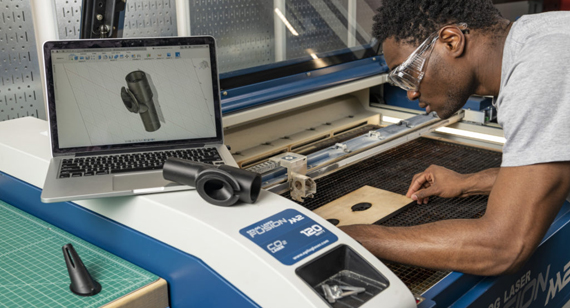
Iterative Prototyping
Iterative prototyping is a cyclic approach where prototypes are continuously developed, tested, and refined based on feedback and testing results. This method emphasizes gradual improvement and allows designers to make incremental changes, ensuring that the final product is well-optimized and free from significant flaws.
Characteristics:
- Cyclic Process: Involves repeated cycles of prototyping, testing, and refinement.
- Continuous Feedback: Incorporates feedback from testing and user evaluations at each iteration.
- Incremental Improvements: Focuses on making small, manageable changes rather than large, sweeping modifications.
Benefits:
- Enhanced Design Quality: Continuous refinement leads to a more polished and functional final product.
- Risk Mitigation: Identifies and addresses potential issues early in the development process, reducing the risk of costly errors later on.
- User-Centric Development: Ensures that the product evolves based on user feedback and real-world testing.
Applications:
- Complex Products: Ideal for products with intricate designs and multiple functionalities that require thorough testing.
- User Experience Optimization: Enhances the usability and user satisfaction of the final product through continuous feedback and adjustments.
Concurrent Prototyping
Concurrent prototyping involves developing multiple prototypes simultaneously, each focusing on different aspects or components of the product. This method allows for parallel testing and refinement of various design elements, accelerating the overall prototyping process and enabling comprehensive evaluation of the product’s functionalities.
Characteristics:
- Parallel Development: Multiple prototypes are developed at the same time, each addressing different components or features.
- Comprehensive Testing: Enables simultaneous testing of various aspects of the product, providing a holistic evaluation.
- Time Efficiency: Reduces the overall time required for prototyping by overlapping development stages.
Benefits:
- Accelerated Development: Speeds up the prototyping process by tackling multiple aspects concurrently.
- Comprehensive Evaluation: Ensures that all components and functionalities are thoroughly tested and optimized.
- Enhanced Collaboration: Promotes teamwork and collaboration among different departments or teams working on separate prototypes.
Applications:
- Multifaceted Products: Suitable for products with diverse functionalities that require specialized testing and development.
- Integrated Systems: Ideal for products that integrate multiple systems or technologies, ensuring seamless interaction and performance.
Rapid Prototyping
Rapid prototyping is an advanced method that utilizes digital technologies such as 3D printing, CNC machining, and vacuum casting to quickly create prototypes. This method emphasizes speed and efficiency, enabling the swift production of prototypes that closely resemble the final product in terms of design and functionality.
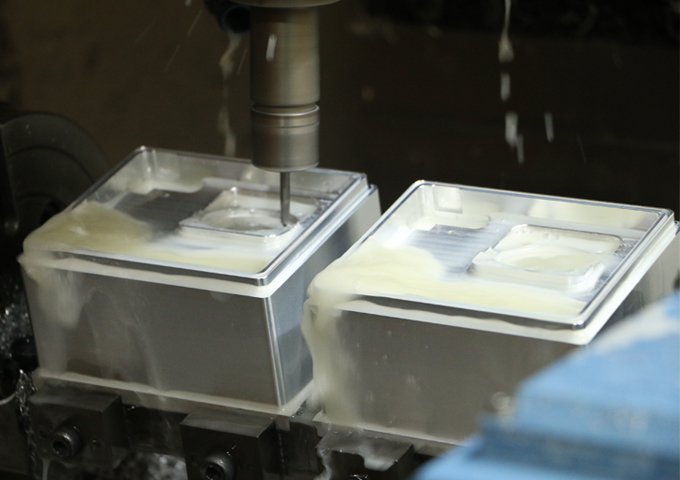
Characteristics:
- High Speed: Significantly reduces the time required to produce prototypes compared to traditional methods.
- Digital Integration: Leverages digital design tools and manufacturing technologies for precise and accurate prototype creation.
- Flexibility: Supports a wide range of materials and design complexities, accommodating various project requirements.
Benefits:
- Speed and Efficiency: Rapidly produces prototypes, allowing for faster iteration and development cycles.
- Precision and Accuracy: Ensures that prototypes are highly accurate and closely match the digital design specifications.
- Cost-Effectiveness: Reduces costs associated with prototyping by minimizing material waste and production time.
Applications:
- Quick Turnaround Projects: Ideal for projects that require fast development and rapid testing.
- Complex Designs: Suitable for prototypes with intricate geometries and detailed features that demand high precision.
- Customization: Facilitates the creation of customized prototypes tailored to specific design requirements and user needs.
What are the Benefits of Industrial Prototyping?
Industrial prototyping offers a multitude of benefits that significantly enhance the product development process. By creating physical models of product designs, manufacturers can gain invaluable insights into design effectiveness, functionality, and market readiness. These benefits not only streamline the development process but also contribute to the overall success and competitiveness of the final product. The primary advantages of industrial prototyping include eliminating design errors, fostering better communication among project stakeholders, and saving time and money.
Eliminating Design Errors
One of the most critical benefits of industrial prototyping is the ability to identify and eliminate design errors before mass production begins. Prototypes serve as the first physical manifestation of a product concept, allowing designers and engineers to test and evaluate the design’s functionality, usability, and overall performance. By rigorously testing prototypes, manufacturers can uncover flaws, inconsistencies, and inefficiencies that may not be apparent in digital models or theoretical designs.
Key Points:
- Early Detection: Prototyping enables the identification of design flaws early in the development process, preventing costly revisions during production.
- Functional Testing: Prototypes allow for the testing of product functionalities under real-world conditions, ensuring that the design meets performance standards.
- Iterative Refinement: Continuous testing and refinement of prototypes lead to a more robust and reliable final product, free from major design issues.
Applications:
- Structural Integrity: Testing prototypes for strength, durability, and reliability to ensure they can withstand intended use and environmental conditions.
- Ergonomics: Evaluating the product’s ease of use and comfort, ensuring that it meets user needs and expectations.
- Performance Metrics: Assessing specific performance metrics, such as speed, efficiency, and responsiveness, to ensure that the product performs as intended.
Better Communication Between Project Stakeholders
Industrial prototyping facilitates enhanced communication and collaboration among various project stakeholders, including designers, engineers, manufacturers, investors, and potential customers. A tangible prototype serves as a common reference point, enabling stakeholders to visualize the product, provide constructive feedback, and make informed decisions based on a shared understanding of the product’s design and functionality.
Key Points:
- Visual Aid: Prototypes provide a clear visual and physical representation of the product, making it easier to convey design concepts and ideas.
- Feedback Mechanism: Enables stakeholders to interact with the prototype, providing valuable feedback that can inform design improvements and refinements.
- Consensus Building: Helps in aligning the vision and expectations of all stakeholders, ensuring that everyone is on the same page regarding the product’s design and functionality.
Applications:
- Design Reviews: Conducting design reviews and presentations with stakeholders using prototypes to illustrate key design elements and functionalities.
- Investor Pitches: Showcasing prototypes to investors to demonstrate the product’s viability and potential for success, enhancing the likelihood of securing funding.
- User Testing: Engaging potential users with prototypes to gather feedback on usability, functionality, and overall user experience, informing further design iterations.
Saving Time and Money
Industrial prototyping is a cost-effective strategy that can lead to substantial savings in both time and money during the product development process. By identifying and addressing design flaws early on, manufacturers can avoid costly redesigns and production delays that may arise from issues discovered during mass production. Additionally, prototyping allows for the optimization of design and manufacturing processes, enhancing efficiency and reducing overall production costs.
Key Points:
- Reduced Redesign Costs: Prototyping minimizes the need for extensive redesigns during production, saving significant time and financial resources.
- Efficient Iterations: Enables rapid iterations and refinements, accelerating the development cycle and reducing time-to-market.
- Material Optimization: Prototyping allows for the testing and optimization of material usage, minimizing waste and lowering material costs.
Applications:
- Cost Analysis: Using prototypes to conduct cost analysis and identify opportunities for material and process optimization, enhancing cost-efficiency.
- Production Planning: Facilitating more accurate production planning and forecasting based on insights gained from prototype testing and evaluation.
- Risk Reduction: Reducing the financial risks associated with product development by ensuring that designs are thoroughly tested and validated before committing to large-scale production.
When Should Prototyping Be Used?
Prototyping is a versatile tool that can be employed at various stages of the product development process, each serving a specific purpose and providing distinct benefits. Understanding the optimal timing for prototyping is essential for maximizing its effectiveness and ensuring that the product development process remains efficient and cost-effective. Prototyping should be considered an integral part of the design and development lifecycle, offering critical insights and validation at key milestones.
Early Stages of Design
Prototyping should begin early in the design process, as it allows designers to explore and validate their ideas before committing to detailed design and development efforts. Creating early prototypes helps in visualizing the product concept, assessing its feasibility, and identifying potential design challenges.
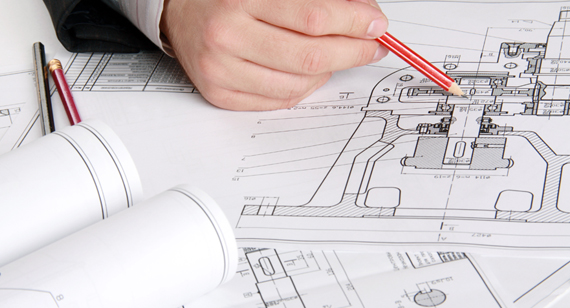
Benefits:
- Concept Visualization: Transforms abstract ideas into tangible models, enhancing the understanding and communication of design concepts.
- Feasibility Assessment: Evaluates the practicality of design ideas, ensuring that they can be implemented effectively.
- Design Iteration: Facilitates the exploration of multiple design alternatives, promoting creativity and innovation.
Mid-Development Phase
During the mid-development phase, prototyping plays a crucial role in testing and refining specific design elements and functionalities. At this stage, more detailed and functional prototypes are created to evaluate the product’s performance, usability, and integration of various components.
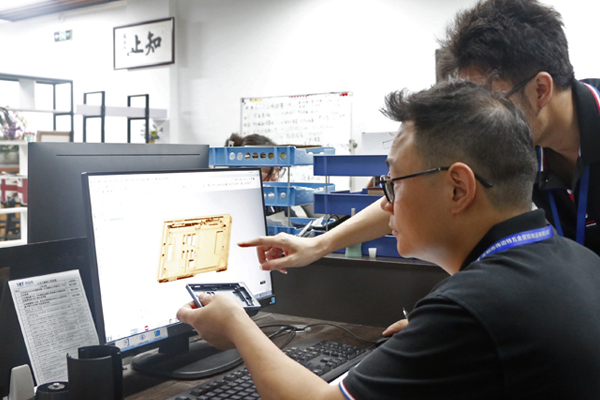
Benefits:
- Functional Testing: Allows for the assessment of the product’s functionality and performance under simulated real-world conditions.
- Design Refinement: Identifies areas for improvement, enabling designers to make informed decisions and optimize the product design.
- Integration Testing: Ensures that different components and systems work together seamlessly, preventing integration issues during production.
Pre-Production Phase
Prototyping is essential in the pre-production phase, where the final design is validated and prepared for mass production. Pre-production prototypes closely resemble the final product in terms of materials, dimensions, and performance, ensuring that the design is fully optimized and ready for manufacturing.

Benefits:
- Manufacturing Validation: Confirms that the product can be manufactured efficiently and meets all quality and performance standards.
- Final Adjustments: Identifies any last-minute design tweaks or adjustments needed before transitioning to full-scale production.
- Quality Assurance: Ensures that the product meets all required standards and specifications, reducing the risk of defects and issues during production.
Continuous Iteration and Improvement
Prototyping should be an ongoing process throughout the product development lifecycle, allowing for continuous iteration and improvement. By regularly creating and testing prototypes, manufacturers can stay agile and responsive to feedback, ensuring that the product evolves to meet changing market demands and user needs.
Benefits:
- Adaptive Design: Enables the product to adapt to new insights, technologies, and market trends, enhancing its competitiveness and relevance.
- User-Centric Development: Ensures that the product remains aligned with user expectations and preferences, fostering higher user satisfaction and adoption.
- Continuous Feedback Loop: Establishes a feedback loop that drives ongoing enhancements and refinements, ensuring that the product remains at the forefront of innovation and quality.
Why is Prototyping Essential for Good Product Design?
Prototyping is a fundamental aspect of good product design, serving as a critical tool for transforming ideas into tangible, functional products. It enables designers and manufacturers to test and refine their designs, ensuring that the final product is not only aesthetically pleasing but also functional, reliable, and aligned with user needs. Prototyping fosters innovation, enhances communication, and facilitates the discovery of unforeseen challenges, making it indispensable for achieving excellence in product design.
Design Evaluation and Testing
Prototyping provides a means for thorough evaluation and testing of product designs, allowing designers to assess the functionality, usability, and performance of their creations before committing to mass production.
Key Points:
- Functional Testing: Prototypes enable the testing of the product’s functionalities, ensuring that they perform as intended and meet design specifications.
- Usability Assessment: Allows for the evaluation of the product’s ease of use, ergonomics, and user experience, ensuring that it meets user needs and expectations.
- Performance Validation: Facilitates the assessment of the product’s performance under real-world conditions, identifying any weaknesses or areas for improvement.
Benefits:
- Identifying Flaws: Uncovers design flaws and inefficiencies, allowing for timely corrections and enhancements.
- Optimizing Design: Informs design optimization, ensuring that the final product is both functional and user-friendly.
- Ensuring Reliability: Validates the product’s reliability and durability, enhancing its marketability and user satisfaction.
Enhancing Communication and Collaboration
Prototyping enhances communication and collaboration among project stakeholders by providing a tangible representation of the product design. It serves as a common reference point that facilitates better understanding, feedback, and decision-making.
Key Points:
- Visual Communication: Prototypes provide a clear visual and physical representation of the product, making it easier to convey design concepts and ideas.
- Stakeholder Engagement: Engages stakeholders in the design process, allowing them to interact with and provide feedback on the prototype.
- Facilitating Feedback: Encourages constructive feedback and collaborative problem-solving, enhancing the overall design process.
Benefits:
- Aligned Vision: Ensures that all stakeholders share a common understanding of the product’s design and functionality.
- Informed Decision-Making: Enables informed decision-making based on tangible evidence and user feedback.
- Enhanced Collaboration: Promotes teamwork and collaboration, leading to more innovative and effective product designs.
Reducing Risks and Costs
Prototyping plays a vital role in risk management and cost reduction by identifying and addressing potential issues early in the product development process. By testing and refining prototypes, manufacturers can mitigate risks associated with design flaws, material inefficiencies, and manufacturing complexities.
Key Points:
- Early Issue Identification: Prototypes help in identifying design and functionality issues before they escalate into costly production problems.
- Cost-Effective Iterations: Allows for cost-effective iterations and refinements, minimizing the financial impact of design changes during later stages.
- Optimizing Materials and Processes: Facilitates the optimization of materials and manufacturing processes, enhancing cost-efficiency and reducing waste.
Benefits:
- Minimized Redesign Costs: Reduces the need for extensive redesigns during production, saving time and resources.
- Enhanced Efficiency: Streamlines the product development process, ensuring that resources are allocated effectively.
- Increased ROI: Maximizes return on investment by ensuring that the final product is optimized for market success and cost-effectiveness.
Industrial Prototyping and Part Manufacturing Capabilities
Industrial prototyping is closely intertwined with part manufacturing capabilities, as the quality and precision of manufactured parts significantly influence the effectiveness of prototypes. Advanced manufacturing technologies, such as CNC machining, vacuum casting, rapid tooling, and 3D printing, play a crucial role in producing high-quality prototype parts that accurately reflect the final product’s design and functionality. Understanding the various part manufacturing capabilities available is essential for selecting the right prototyping method and ensuring that the prototypes meet the desired standards of quality and performance.
CNC Machining
CNC (Computer Numerical Control) machining is a highly precise and versatile manufacturing process used to create detailed and accurate prototype parts from a variety of materials, including metals, plastics, and composites. CNC machining involves the use of computer-controlled machines to remove material from a solid block, shaping it into the desired form based on CAD (Computer-Aided Design) models.
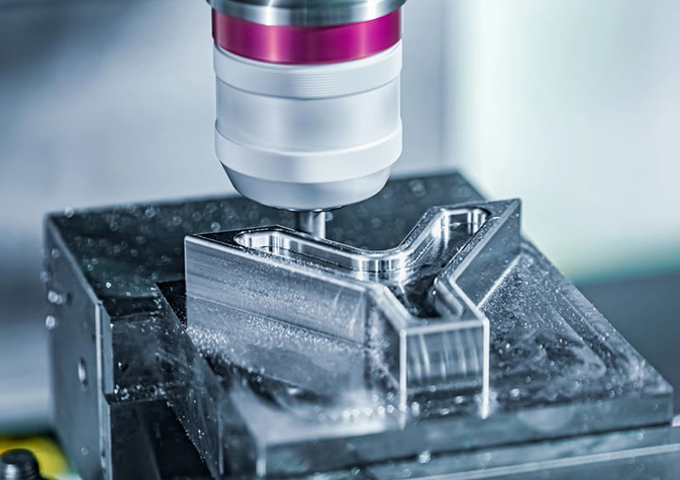
Key Features:
- Precision and Accuracy: CNC machining offers exceptional precision and repeatability, ensuring that prototype parts closely match the design specifications.
- Material Versatility: Capable of working with a wide range of materials, allowing for the creation of prototypes that reflect the final product’s material properties.
- Complex Geometries: Supports the creation of intricate and complex geometries that are difficult to achieve with manual machining methods.
Benefits:
- High Quality: Produces high-quality prototype parts with smooth finishes and tight tolerances, enhancing the prototype’s accuracy and reliability.
- Efficiency: Streamlines the prototyping process by enabling rapid and consistent production of parts, reducing lead times and costs.
- Customization: Allows for easy customization and modifications, facilitating iterative design and testing.
Applications:
- Mechanical Components: Ideal for creating precise mechanical parts, such as gears, housings, and brackets, that require high accuracy and durability.
- Functional Prototypes: Suitable for producing working prototypes that demonstrate the product’s functionality and performance under real-world conditions.
- Complex Assemblies: Enables the creation of complex assemblies with multiple interconnected parts, ensuring seamless integration and functionality.
Vacuum Casting
Vacuum casting is an advanced prototyping technique that involves creating molds from master models and using them to produce high-quality prototype parts. This process is particularly useful for producing multiple copies of a prototype with consistent quality and detail.
Key Features:
- High Precision: Produces prototypes with fine details and accurate dimensions, closely resembling the final product.
- Material Diversity: Supports a wide range of materials, including elastomers, resins, and thermoplastics, allowing for the creation of prototypes with varied material properties.
- Cost-Effective for Multiple Copies: Ideal for producing small batches of prototypes, making it cost-effective for testing and validation purposes.
Benefits:
- Consistency: Ensures uniformity and consistency across multiple prototype parts, enhancing the reliability of testing and evaluation.
- Detail and Quality: Delivers high-quality prototypes with detailed features and smooth surface finishes, reflecting the final product’s design aesthetics.
- Speed: Accelerates the prototyping process by enabling the rapid production of multiple parts from a single mold.
Applications:
- Consumer Products: Used for creating detailed and visually accurate prototypes of consumer products, such as electronics, appliances, and household items.
- Medical Devices: Facilitates the production of precise and reliable prototypes for medical devices, ensuring compliance with stringent regulatory standards.
- Automotive Components: Ideal for producing high-quality prototypes of automotive parts, such as dashboards, panels, and interior components, that require precise fit and finish.
Rapid Tooling
Rapid tooling is a prototyping method that involves the quick creation of tooling components, such as molds and dies, using advanced manufacturing technologies. This approach enables manufacturers to produce prototype parts and test production processes without the need for traditional, time-consuming tooling methods.
Key Features:
- Speed: Significantly reduces the time required to produce tooling components, accelerating the prototyping and testing phases.
- Flexibility: Allows for easy modifications and adjustments to tooling designs, facilitating iterative design and testing.
- Cost-Effective: Minimizes the costs associated with traditional tooling methods, making it accessible for small-scale prototyping and testing.
Benefits:
- Accelerated Development: Enables faster development and testing of prototype parts, reducing overall project timelines.
- Enhanced Flexibility: Supports iterative design processes by allowing for quick adjustments to tooling components based on testing results and feedback.
- Cost Savings: Reduces the financial burden of producing and modifying tooling components, making it a cost-effective option for prototype production.
Applications:
- Injection Molding: Used for creating rapid molds for injection molding processes, enabling the swift production of plastic prototypes.
- Metal Casting: Facilitates the production of rapid molds for metal casting, allowing for the creation of precise and detailed metal prototype parts.
- Composite Manufacturing: Ideal for producing tooling components used in composite manufacturing processes, ensuring accurate and reliable prototype production.
3D Printing
3D printing, also known as additive manufacturing, is a versatile and widely used prototyping technology that builds physical models layer by layer based on digital designs. This method supports a wide range of materials and is known for its ability to produce complex and intricate designs with high precision.
Key Features:
- Additive Process: Creates prototypes by adding material layer by layer, enabling the production of complex and detailed geometries.
- Material Variety: Supports a diverse range of materials, including plastics, metals, ceramics, and composites, allowing for the creation of prototypes with varied properties.
- Customization: Facilitates easy customization and modifications to prototypes, supporting iterative design and testing processes.
Benefits:
- Speed: Rapidly produces prototypes, significantly reducing the time from design to physical model.
- Cost-Effective for Complex Designs: Offers a cost-effective solution for producing complex and intricate designs without the need for specialized tooling.
- Flexibility and Versatility: Accommodates a wide range of design requirements and materials, enhancing the versatility of prototype production.
Applications:
- Functional Prototypes: Ideal for creating fully functional prototypes that demonstrate the product’s operational capabilities and performance.
- Visual Prototypes: Used for producing visually accurate prototypes that showcase the product’s design aesthetics and ergonomics.
- Custom Parts: Facilitates the production of customized parts tailored to specific design requirements and user needs, enhancing the overall flexibility of the prototyping process.
Ballistic Particle Manufacturing (BPM)
Ballistic Particle Manufacturing (BPM) is an advanced additive manufacturing technique that utilizes high-speed particle deposition to create detailed and precise prototypes. This method is particularly useful for producing lightweight and durable parts with complex geometries.
Key Features:
- High-Speed Deposition: Uses high-speed particles to build prototypes layer by layer, ensuring rapid and efficient production.
- Material Efficiency: Minimizes material waste by precisely depositing only the necessary amount of material required for the prototype.
- Lightweight and Durable: Produces lightweight prototypes without compromising on strength and durability, making it ideal for high-performance applications.
Benefits:
- Efficiency: Accelerates the prototyping process by enabling the rapid production of lightweight and durable parts.
- Precision: Ensures high precision and accuracy in prototype production, enhancing the reliability and functionality of the final product.
- Material Optimization: Optimizes material usage, reducing costs and enhancing the sustainability of the prototyping process.
Applications:
- Aerospace Components: Used for creating lightweight and durable prototypes of aerospace components, ensuring optimal performance and reliability.
- Automotive Parts: Facilitates the production of high-performance automotive prototypes, enhancing the design and functionality of vehicle parts.
- Medical Devices: Ideal for producing precise and reliable prototypes of medical devices, ensuring compliance with stringent regulatory standards.
Directed Light Fabrication (DLF)
Directed Light Fabrication (DLF) is an advanced additive manufacturing technique that employs directed energy, such as lasers or electron beams, to fuse material powders into solid objects. This method is known for its ability to produce high-strength and highly detailed prototypes with exceptional surface finishes.
Key Features:
- Directed Energy: Uses focused energy sources to precisely fuse material powders, ensuring high accuracy and detail in prototype production.
- High-Strength Prototypes: Produces prototypes with superior mechanical properties, making them suitable for high-performance applications.
- Exceptional Surface Finishes: Delivers smooth and refined surface finishes, enhancing the aesthetic and functional quality of prototypes.
Benefits:
- Precision and Accuracy: Ensures highly accurate and precise prototype production, meeting stringent design specifications.
- Mechanical Performance: Produces prototypes with high strength and durability, making them suitable for rigorous testing and evaluation.
- Surface Quality: Enhances the visual and functional quality of prototypes through exceptional surface finishes, improving user experience and aesthetic appeal.
Applications:
- Aerospace: Used for creating high-strength prototypes of aerospace components, ensuring they meet performance and safety standards.
- Medical Implants: Facilitates the production of precise and reliable prototypes of medical implants, enhancing patient outcomes and device reliability.
- High-Performance Electronics: Ideal for producing prototypes of high-performance electronic components, ensuring functionality and durability in demanding applications.
Direct Shell Production Casting (DSPC)
Direct Shell Production Casting (DSPC) is a specialized prototyping technique that combines 3D printing with traditional casting methods to produce highly detailed and accurate metal and ceramic prototypes. This hybrid approach leverages the strengths of additive manufacturing and casting to create prototypes that closely resemble the final product in terms of material properties and design intricacies.
Key Features:
- Hybrid Manufacturing: Integrates 3D printing with casting, enabling the production of detailed and precise prototypes with complex geometries.
- Material Accuracy: Ensures that prototypes are made from materials that closely match the final product’s specifications, enhancing realism and functionality.
- Detailed Replication: Delivers highly detailed prototypes with intricate design features, accurately reflecting the final product’s aesthetics and functionality.
Benefits:
- High Fidelity: Produces prototypes with high fidelity to the final product’s design, ensuring accurate representation and functionality.
- Versatility: Supports a wide range of materials, including metals and ceramics, enhancing the versatility of prototype production.
- Efficiency: Streamlines the prototyping process by combining additive manufacturing and casting, reducing production time and costs.
Applications:
- Automotive Prototypes: Used for creating detailed and functional prototypes of automotive components, ensuring they meet design and performance standards.
- Aerospace Parts: Facilitates the production of precise and durable aerospace prototypes, enhancing design validation and testing.
- Industrial Machinery: Ideal for producing prototypes of industrial machinery components, ensuring functionality and reliability in operational environments.
Fused Deposition Modeling (FDM)
Fused Deposition Modeling (FDM) is a widely used 3D printing technology that involves the extrusion of thermoplastic filaments through a heated nozzle to build prototypes layer by layer. FDM is known for its affordability, simplicity, and versatility, making it a popular choice for rapid prototyping across various industries.
Key Features:
- Additive Process: Builds prototypes by adding material layer by layer, allowing for the creation of complex and intricate designs.
- Material Variety: Supports a wide range of thermoplastic materials, including ABS, PLA, PETG, and specialized engineering plastics.
- Ease of Use: Offers a straightforward and user-friendly prototyping process, making it accessible for designers and manufacturers.
Benefits:
- Cost-Effective: Provides an affordable solution for producing prototypes, particularly for simple to moderately complex designs.
- Speed: Enables rapid production of prototypes, reducing lead times and accelerating the design iteration process.
- Customization: Facilitates easy customization and modifications, allowing for flexible and adaptive prototyping.
Applications:
- Functional Prototypes: Ideal for creating functional prototypes that demonstrate the product’s operational capabilities and performance.
- Visual Models: Used for producing visually accurate prototypes that showcase the product’s design aesthetics and ergonomics.
- Educational Models: Facilitates the creation of prototypes for educational purposes, enhancing learning and design understanding.
Laminated Object Manufacturing (LOM)
Laminated Object Manufacturing (LOM) is an additive manufacturing process that builds prototypes by laminating layers of material, such as paper, plastic, or metal, and then cutting them to the desired shape using a laser or knife. LOM is a cost-effective and efficient technique for producing large and lightweight prototypes with moderate precision and surface finish.
Key Features:
- Layered Construction: Builds prototypes by layering and cutting materials, allowing for the creation of 3D structures from 2D sheets.
- Cost-Effective: Offers a low-cost prototyping solution, particularly for large-scale and lightweight models.
- Material Flexibility: Supports a variety of materials, including paper, plastic, and metal laminates, enhancing versatility.
Benefits:
- Affordability: Reduces prototyping costs by utilizing inexpensive materials and efficient production processes.
- Large Prototypes: Enables the creation of large-scale prototypes that are difficult to produce with other additive manufacturing techniques.
- Speed: Facilitates rapid production of prototypes, making it suitable for projects that require quick turnaround times.
Applications:
- Architectural Models: Used for creating large-scale architectural prototypes, enabling detailed visualization of building designs and structures.
- Packaging Prototypes: Facilitates the production of packaging prototypes, ensuring that designs meet aesthetic and functional requirements.
- Educational Models: Ideal for producing prototypes for educational and training purposes, enhancing understanding and demonstration of complex concepts.
Laminated Resin Printing (LRP)
Laminated Resin Printing (LRP) is a specialized form of Laminated Object Manufacturing (LOM) that uses resin-based materials to create prototypes with enhanced mechanical properties and surface finishes. LRP combines the layering and cutting processes of LOM with resin curing, enabling the production of high-quality prototypes that closely resemble the final product in terms of material properties and design intricacies.
Key Features:
- Resin-Based Materials: Utilizes resin-coated materials, enhancing the mechanical properties and surface finish of the prototypes.
- Hybrid Process: Combines additive manufacturing and resin curing, ensuring detailed and durable prototypes.
- Enhanced Detail: Delivers prototypes with improved detail and surface quality compared to traditional LOM techniques.
Benefits:
- Improved Strength: Produces prototypes with enhanced mechanical strength and durability, making them suitable for rigorous testing and evaluation.
- Superior Surface Finish: Achieves smoother and more refined surface finishes, enhancing the visual and tactile quality of the prototypes.
- Versatility: Supports a wide range of resin-based materials, allowing for the creation of prototypes with varied material properties and design complexities.
Applications:
- Medical Device Prototypes: Used for creating precise and durable prototypes of medical devices, ensuring compliance with regulatory standards and enhancing functionality.
- Industrial Components: Facilitates the production of high-quality prototypes of industrial components, ensuring reliability and performance in operational environments.
- Consumer Electronics: Ideal for producing detailed and functional prototypes of consumer electronic devices, enhancing design validation and user testing.
Benefits of Prototyping in Industrial Design
Prototyping offers a myriad of benefits that significantly enhance the industrial design process, ensuring that the final product is both innovative and market-ready. By creating tangible models of product designs, manufacturers can engage in detailed design discussions, optimize designs, test functionalities, and verify overall design integrity. These benefits collectively contribute to the creation of high-quality, reliable, and user-centric products that meet market demands and exceed user expectations.
Design Discussion
Prototyping facilitates comprehensive design discussions among team members, stakeholders, and clients by providing a physical model to reference. This tangible representation of the product allows for more effective communication, enabling participants to visualize and interact with the design, thereby fostering a deeper understanding and more informed decision-making.
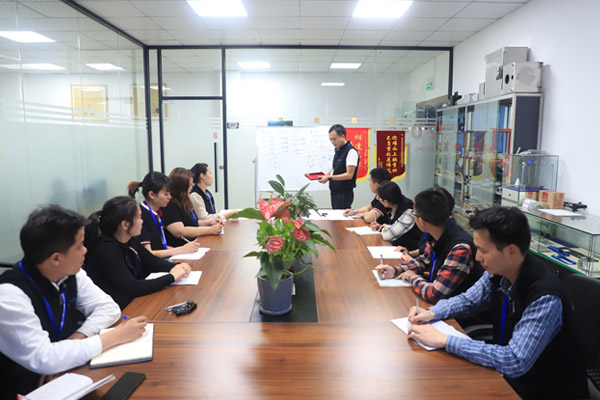
Key Points:
- Visual Aid: Prototypes serve as visual aids that enhance the clarity of design concepts, making it easier for stakeholders to grasp complex ideas.
- Interactive Feedback: Provides opportunities for interactive feedback, allowing team members to suggest improvements and modifications based on hands-on experience with the prototype.
- Collaborative Refinement: Encourages collaborative refinement of the design, leveraging diverse perspectives to enhance the overall product quality.
Benefits:
- Enhanced Understanding: Ensures that all team members have a clear and consistent understanding of the product design and its intended functionalities.
- Informed Decision-Making: Enables informed decision-making by providing tangible evidence and insights into the design’s strengths and weaknesses.
- Innovation Promotion: Fosters an environment of innovation and creativity, encouraging the exploration of new ideas and solutions to design challenges.
Applications:
- Design Workshops: Conducting design workshops and brainstorming sessions using prototypes to explore and refine design concepts.
- Stakeholder Meetings: Presenting prototypes to stakeholders to facilitate discussions and gather feedback on design elements and functionalities.
- Client Presentations: Showcasing prototypes to clients to demonstrate design progress and gather input for further refinements.
Design Optimization
Prototyping is instrumental in the optimization of product designs, allowing designers to identify and address inefficiencies, enhance functionalities, and improve overall product performance. By testing and refining prototypes, manufacturers can ensure that the final product is both effective and efficient, meeting all design requirements and user expectations.
Key Points:
- Functional Refinement: Identifies areas where the product’s functionality can be enhanced or streamlined, ensuring optimal performance.
- Ergonomic Improvements: Evaluates and improves the product’s ergonomics, ensuring ease of use and user comfort.
- Material and Process Optimization: Tests different materials and manufacturing processes to identify the most effective and cost-efficient options.
Benefits:
- Enhanced Performance: Optimizes the product’s performance by refining design elements and ensuring that all components function seamlessly together.
- Cost Efficiency: Reduces production costs by identifying and eliminating design inefficiencies and optimizing material usage.
- User Satisfaction: Improves user satisfaction by ensuring that the product is intuitive, comfortable, and meets user needs effectively.
Applications:
- Performance Testing: Conducting performance tests to assess and enhance the product’s operational capabilities and reliability.
- Ergonomic Assessments: Evaluating the product’s ergonomics through user testing, ensuring that it is comfortable and easy to use.
- Material Trials: Testing different materials and manufacturing processes to identify the most suitable and cost-effective options for production.
Design Testing
Prototyping provides a platform for comprehensive design testing, enabling manufacturers to evaluate the product’s functionality, performance, and user experience under various conditions. This testing is crucial for ensuring that the product meets all design specifications and operates reliably in real-world scenarios.
Key Points:
- Functional Testing: Assessing the product’s functionality and performance to ensure that it meets the intended design criteria.
- Durability Testing: Evaluating the product’s durability and reliability, ensuring that it can withstand the conditions it will encounter in use.
- User Testing: Gathering user feedback through interactive testing to evaluate the product’s usability, ergonomics, and overall user experience.
Benefits:
- Quality Assurance: Ensures that the product meets high-quality standards, enhancing its marketability and user satisfaction.
- Issue Identification: Identifies and addresses any design or functionality issues before mass production, reducing the risk of defects and recalls.
- Performance Validation: Confirms that the product performs as intended, ensuring reliability and consistency in its operation.
Applications:
- Stress Testing: Conducting stress tests to evaluate the product’s performance under extreme conditions and identify any structural weaknesses.
- Usability Testing: Engaging users in testing the prototype to gather insights into the product’s usability and user experience.
- Environmental Testing: Assessing the product’s performance in various environmental conditions, such as temperature, humidity, and exposure to elements.
Design Verification
Design verification involves confirming that the product design meets all specified requirements and standards before proceeding to mass production. Prototyping plays a critical role in design verification by providing a physical model that can be rigorously tested and evaluated against design criteria.
Key Points:
- Compliance Testing: Ensuring that the product meets all relevant industry standards and regulatory requirements.
- Specification Matching: Verifying that the product design aligns with the initial specifications and design objectives.
- Performance Benchmarks: Assessing the product’s performance against established benchmarks to ensure it meets or exceeds expectations.
Benefits:
- Regulatory Compliance: Ensures that the product adheres to all necessary regulatory standards, preventing legal and compliance issues.
- Design Accuracy: Confirms that the product design accurately reflects the intended specifications and requirements.
- Market Readiness: Validates that the product is ready for market entry, ensuring a smooth transition from prototyping to mass production.
Applications:
- Regulatory Submissions: Preparing prototypes for submission to regulatory bodies to obtain necessary certifications and approvals.
- Final Design Reviews: Conducting comprehensive design reviews using prototypes to ensure that all design elements are accurate and compliant.
- Performance Benchmarking: Comparing the prototype’s performance against industry benchmarks to assess its competitiveness and readiness for market release.
Application of Prototyping in Industrial Design
Prototyping is a versatile tool that finds application across various industries, each leveraging its unique advantages to enhance product development and innovation. From automotive and medical sectors to aerospace, military, and consumer products, prototyping plays a pivotal role in creating high-quality, functional, and reliable products that meet stringent industry standards and user expectations. Understanding the diverse applications of prototyping in industrial design highlights its significance in driving technological advancements and market success.
Automotive
In the automotive industry, prototyping is essential for developing and testing new vehicle designs, components, and technologies. Prototypes undergo rigorous testing to evaluate performance, safety, and durability, ensuring that the final product meets the high standards required in the competitive automotive market.
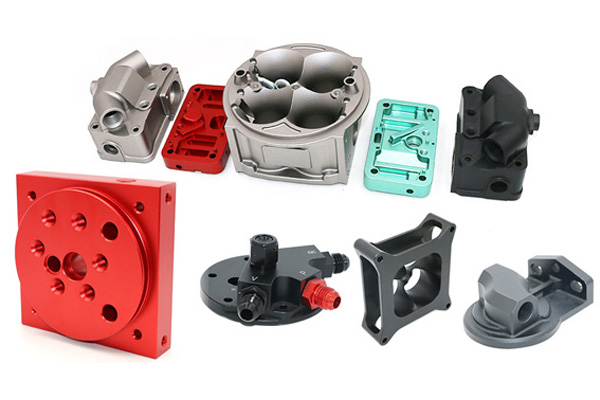
Key Applications:
- Engine Components: Prototyping engine parts to test their efficiency, performance, and durability under various operating conditions.
- Vehicle Bodies: Creating full-scale prototypes of vehicle bodies to assess aerodynamics, structural integrity, and crash safety.
- Interior Components: Developing prototypes of interior elements, such as dashboards, seats, and infotainment systems, to enhance ergonomics and user experience.
Benefits:
- Performance Validation: Ensures that engine components and other critical parts perform optimally, enhancing vehicle performance and reliability.
- Safety Assurance: Validates the safety features and structural integrity of vehicle bodies, ensuring compliance with safety regulations.
- User Experience Enhancement: Improves the design and functionality of interior components, enhancing overall user satisfaction and comfort.
Medical
Prototyping is crucial in the medical industry, where precision, reliability, and compliance with regulatory standards are paramount. Medical prototypes undergo extensive testing to ensure that they meet stringent requirements for functionality, safety, and usability, facilitating the development of life-saving and life-enhancing medical devices.
Key Applications:
- Surgical Instruments: Creating precise prototypes of surgical tools to ensure accuracy, ergonomics, and sterilization compatibility.
- Implants and Prosthetics: Developing reliable and comfortable prototypes of implants and prosthetic devices to enhance patient outcomes and device performance.
- Diagnostic Equipment: Prototyping diagnostic devices to ensure accuracy, reliability, and ease of use in clinical settings.
Benefits:
- Regulatory Compliance: Ensures that medical devices meet all necessary regulatory standards, preventing compliance issues and enhancing patient safety.
- Functionality and Reliability: Validates the functionality and reliability of medical devices, ensuring they perform effectively in critical applications.
- Patient-Centric Design: Enhances the usability and comfort of medical devices, improving patient experience and satisfaction.
Aerospace
In the aerospace industry, prototyping is indispensable for developing and testing aircraft, spacecraft, and related technologies. Prototypes undergo extensive testing to evaluate performance, safety, and compliance with stringent industry standards, ensuring that aerospace products meet the highest levels of quality and reliability.
Key Applications:
- Aircraft Components: Prototyping components such as wings, fuselages, and propulsion systems to assess aerodynamics, structural integrity, and performance.
- Spacecraft Systems: Developing prototypes of spacecraft components to ensure functionality and reliability in extreme environments.
- Avionics: Prototyping avionics systems to evaluate their performance, reliability, and compliance with aerospace standards.
Benefits:
- Performance Validation: Ensures that aircraft and spacecraft components perform optimally, enhancing safety and operational efficiency.
- Safety Assurance: Validates the safety features and structural integrity of aerospace products, ensuring compliance with safety regulations.
- Technological Advancement: Facilitates the development of innovative aerospace technologies, enhancing the competitiveness and capability of aerospace products.
Military
Prototyping plays a critical role in the military sector, where the development of advanced weapons systems, equipment, and technologies requires precision, reliability, and adherence to strict performance standards. Military prototypes undergo rigorous testing to ensure that they meet the operational and tactical requirements necessary for successful deployment.
Key Applications:
- Weapons Systems: Prototyping advanced weapons systems to evaluate their performance, accuracy, and reliability in various operational scenarios.
- Protective Gear: Developing prototypes of protective gear, such as helmets and body armor, to enhance safety and comfort for military personnel.
- Communication Equipment: Creating prototypes of communication devices to ensure reliability and functionality in diverse and challenging environments.
Benefits:
- Operational Readiness: Ensures that military equipment and weapons systems are fully functional and ready for deployment, enhancing operational effectiveness.
- Safety and Reliability: Validates the safety and reliability of military equipment, ensuring the protection and effectiveness of military personnel.
- Technological Superiority: Facilitates the development of cutting-edge military technologies, maintaining technological superiority and strategic advantage.
Consumer Products
Prototyping is vital in the development of consumer products, enabling manufacturers to create and test new devices, appliances, and everyday items that meet user needs and market demands. Prototypes undergo usability testing, aesthetic evaluation, and functionality assessment to ensure that they are both appealing and effective, enhancing their marketability and user satisfaction.
Key Applications:
- Home Appliances: Creating prototypes of home appliances, such as refrigerators, washing machines, and kitchen gadgets, to test functionality and design aesthetics.
- Personal Gadgets: Developing prototypes of personal gadgets, such as smartphones, smartwatches, and fitness trackers, to evaluate usability, ergonomics, and performance.
- Furniture and Lifestyle Products: Prototyping furniture and lifestyle products to assess design, ergonomics, and user experience, ensuring that they meet consumer preferences and market trends.
Benefits:
- User-Centric Design: Ensures that consumer products are designed with user needs and preferences in mind, enhancing usability and satisfaction.
- Market Readiness: Validates the marketability and appeal of consumer products, increasing their chances of success upon release.
- Aesthetic and Functional Balance: Balances aesthetic design with functionality, ensuring that products are both visually appealing and highly functional.
Get Help from Prototyping Experts to Help Your Industrial Design
Navigating the complexities of industrial design prototyping requires specialized expertise and advanced manufacturing capabilities. Partnering with prototyping experts can significantly enhance the efficiency and effectiveness of your prototyping process, ensuring that your prototypes are manufactured with precision, quality, and speed. Expert prototyping services offer comprehensive support, from initial design consultation to the final production of high-quality prototypes, enabling manufacturers and designers to bring their visions to life with confidence and excellence.
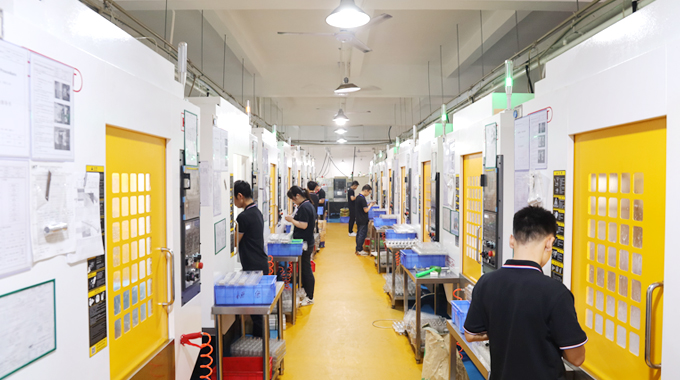
Why Choose Prototyping Experts?
Expertise in CNC Machining Parts
Prototyping experts possess extensive knowledge and experience in CNC machining parts, enabling them to produce highly accurate and detailed prototypes that closely match your design specifications. Their proficiency in operating advanced CNC machinery ensures that every aspect of your prototype is meticulously crafted, enhancing the overall quality and reliability of the final product.
Key Benefits:
- Precision and Accuracy: Ensures that prototype parts are manufactured with exact dimensions and tolerances, reflecting the design intent accurately.
- Material Versatility: Capable of working with a wide range of materials, providing flexibility to create prototypes that match the final product’s material properties.
- Complex Geometries: Expertise in creating intricate and complex designs that may be challenging to produce using traditional manufacturing methods.
Custom CNC Machining Solutions
Prototyping experts offer custom CNC processing solutions tailored to your specific prototyping needs. Whether you require single parts, small batches, or complex assemblies, they can provide the necessary machining services to produce prototypes that meet your unique requirements and project timelines.
Key Benefits:
- Tailored Services: Custom CNC processing ensures that your prototypes are manufactured to meet your specific design and functional requirements.
- Scalability: Ability to scale prototyping efforts based on project demands, accommodating both small-scale and large-scale prototyping needs.
- Efficiency: Streamlined CNC machining processes enhance the speed and efficiency of prototype production, reducing lead times and accelerating the design iteration process.
Advanced CNC Prototype Machining
Prototyping experts leverage advanced CNC prototype processing techniques to enhance the quality and functionality of your prototypes. By utilizing state-of-the-art CNC machinery and cutting-edge machining technologies, they can produce prototypes that not only meet but exceed your design expectations, ensuring that your final product is both innovative and reliable.
Key Benefits:
- High-Fidelity Prototypes: Produces high-fidelity prototypes that accurately replicate the design and functionality of the final product, providing a reliable basis for testing and evaluation.
- Innovative Techniques: Utilizes innovative CNC machining techniques to address complex design challenges, enhancing the overall quality and performance of the prototype.
- Quality Assurance: Implements stringent quality control measures to ensure that every prototype meets the highest standards of precision and craftsmanship.
Comprehensive CNC Machining Services
Prototyping experts offer a full spectrum of CNC machining services, covering every aspect of the prototyping process from design consultation to final production. Their comprehensive services ensure that your prototypes are developed seamlessly, with every detail meticulously attended to, enhancing the overall efficiency and effectiveness of the product development cycle.
Key Services:
- Design Consultation: Provides expert design consultation to refine and optimize your product designs for CNC machining, ensuring that they are manufacturable and meet your project goals.
- CAD/CAM Integration: Utilizes advanced CAD/CAM software to translate your digital designs into precise machining instructions, enhancing the accuracy and efficiency of the prototyping process.
- Rapid Prototyping: Offers rapid prototyping services to quickly produce prototypes, enabling faster design iterations and reducing time-to-market.
- Functional Testing: Facilitates functional testing of prototypes, ensuring that they perform as intended and meet all design and performance criteria.
- Final Production Support: Provides support for the transition from prototype to mass production, ensuring that the final product is manufactured with consistency and quality.
Benefits of Partnering with Prototyping Experts
Cost Efficiency
Partnering with prototyping experts can lead to significant cost savings by optimizing the prototyping process and minimizing material waste. Their expertise in CNC machining ensures that prototypes are manufactured efficiently, reducing the need for multiple iterations and minimizing overall development costs.
Key Points:
- Optimized Material Usage: Expertise in selecting and utilizing materials efficiently, reducing waste and lowering material costs.
- Efficient Processes: Streamlined CNC machining processes enhance production efficiency, reducing labor and operational costs.
- Iterative Refinement: Enables cost-effective iterative design and testing, ensuring that design flaws are identified and addressed early in the development process.
Enhanced Quality and Precision
Prototyping experts ensure that every prototype is manufactured with the highest levels of quality and precision. Their advanced CNC machining capabilities allow for the creation of prototypes that closely match your design specifications, enhancing the reliability and functionality of the final product.
Key Points:
- High-Quality Prototypes: Ensures that prototypes are free from defects and meet all design and performance requirements.
- Tight Tolerances: Ability to produce prototypes with tight tolerances, ensuring that all components fit and function correctly.
- Consistency: Maintains consistency across multiple prototype iterations, ensuring that each version accurately reflects the design intent.
Faster Time-to-Market
Expert prototyping services can accelerate your product development cycle, enabling you to bring your products to market more swiftly. By leveraging rapid prototyping techniques and advanced CNC machining processes, prototyping experts reduce lead times and facilitate faster design iterations, enhancing your competitive edge in the market.
Key Points:
- Rapid Production: Enables the swift production of prototypes, reducing overall development time and allowing for faster testing and refinement.
- Iterative Testing: Facilitates rapid design iterations based on testing and feedback, ensuring that the final product is optimized for market readiness.
- Market Agility: Enhances your ability to respond quickly to market demands and changes, maintaining your product’s relevance and competitiveness.
Conclusion
Industrial design prototyping is a critical component of the product development lifecycle, offering numerous benefits that enhance design quality, functionality, and market readiness. By leveraging advanced prototyping methods such as iterative, concurrent, and rapid prototyping, manufacturers and designers can optimize their products, reduce risks, and achieve significant cost savings. Prototyping enables comprehensive design discussions, facilitates design optimization, and ensures that products meet user needs and industry standards through thorough testing and verification.
Partnering with prototyping experts, especially those specializing in CNC machining parts and services, can further elevate your prototyping process. These experts provide precision, quality, and efficiency, ensuring that your prototypes accurately reflect your design intent and are manufactured to the highest standards. Whether you are developing automotive components, medical devices, aerospace parts, military equipment, or consumer products, industrial design prototyping is essential for creating innovative, reliable, and market-ready products.
Embrace the power of industrial design prototyping to drive innovation, enhance product quality, and achieve market success. By integrating robust prototyping strategies and collaborating with prototyping experts, you can transform your product ideas into tangible, functional, and high-quality solutions that meet the demands of today’s competitive markets.
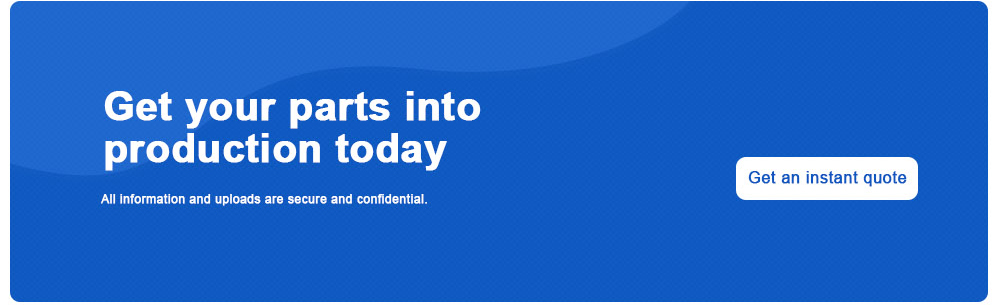
FAQs
1. What is the goal of prototyping?
The primary goal of prototyping is to transform product ideas into tangible models that can be tested and evaluated. Prototyping aims to validate design concepts, identify and eliminate design flaws, optimize functionality, and enhance user experience before moving to mass production. By creating and testing prototypes, manufacturers can ensure that the final product meets all design specifications, performs reliably, and aligns with user needs and market demands.
2. What are the 4 different types of product prototypes?
The four different types of product prototypes are:
- Proof of Concept Prototype: Demonstrates the feasibility of a product idea or a specific aspect of its design.
- Visual Prototype: Focuses on the aesthetic aspects of the product, providing a realistic representation of its appearance.
- Working Prototype: A fully functional model that replicates the core functionalities and operational capabilities of the final product.
- Pre-Production Prototype or Factory Sample: The final prototype created before mass production, closely resembling the final product in terms of materials, dimensions, and performance.
3. How is prototyping used in the technology industry?
In the technology industry, prototyping is used to develop and test new devices, software applications, and electronic systems. Prototypes allow engineers and designers to evaluate the functionality, usability, and performance of technological products under real-world conditions. This process enables rapid iteration and refinement, ensuring that the final product is both innovative and reliable. Prototyping in the technology industry encompasses a wide range of methods, including 3D printing, CNC machining, and rapid prototyping techniques, to create detailed and functional models for testing and validation.
4. Why is prototyping used in industry?
Prototyping is used in industry to validate and refine product designs, ensuring that they meet functional, aesthetic, and market requirements before mass production. It serves as a critical tool for identifying and addressing design flaws, optimizing functionality, enhancing user experience, and reducing development costs. Prototyping also facilitates better communication and collaboration among project stakeholders, enabling informed decision-making and fostering innovation. By using prototypes, manufacturers can ensure that their products are reliable, cost-effective, and aligned with user needs and market demands.
5. What is CAD prototyping?
CAD prototyping involves using Computer-Aided Design (CAD) software to create detailed digital models of a product, which are then translated into physical prototypes using manufacturing technologies such as CNC machining and 3D printing. CAD prototyping allows for precise and accurate representation of design concepts, enabling thorough testing and evaluation of product functionalities and aesthetics. This method facilitates rapid iterations and modifications, ensuring that the final prototype closely matches the intended design and meets all necessary specifications.
By adhering to the comprehensive principles and strategies outlined in this guide, manufacturers can harness the full potential of industrial design prototyping to optimize their design processes, reduce costs, and deliver high-quality products that meet market demands and exceed user expectations. Leveraging advanced prototyping methods and partnering with expert CNC machining services ensures that your prototypes are manufactured with precision, quality, and efficiency, paving the way for successful product launches and sustained market presence.