Are you struggling to choose between CNC turning and CNC milling for your manufacturing needs? Confused about which process is more suitable for your specific project, leading to potential inefficiencies and increased costs? You're not alone. Many manufacturers grapple with understanding the distinct differences between these two fundamental CNC machining processes. But what if you could gain a clear understanding of both CNC turning and milling, enabling you to make informed decisions that optimize production, enhance precision, and reduce expenses?
CNC turning and CNC milling are distinct machining processes: CNC turning rotates the workpiece while a stationary cutting tool shapes it, ideal for producing cylindrical parts; CNC milling keeps the workpiece stationary while rotating cutting tools move around it to create complex shapes, making it suitable for parts with intricate geometries.
Understanding the key differences between CNC turning and milling is crucial for selecting the right process for your project. Let's delve deeper into what each process entails, their advantages and limitations, and how to choose the most appropriate method for your specific manufacturing needs.
Preface
In the world of precision manufacturing, Computer Numerical Control (CNC) machining stands as a cornerstone technology, enabling the production of complex and high-precision parts. Two of the most fundamental CNC machining processes are CNC turning and CNC milling. While both are essential in creating a wide array of components, they operate on different principles and are suited for different types of parts. This comprehensive guide aims to elucidate the differences between CNC turning and milling, providing insights into their processes, advantages, limitations, and applications. Whether you're involved in custom CNC machining, operate a CNC machining factory, or seek CNC machining services, understanding these differences will empower you to optimize your production processes.
What Is CNC Turning?
CNC turning is a machining process where a cutting tool, typically a non-rotary tool bit, moves linearly while the workpiece rotates. The operation is performed on a CNC lathe or turning center, where the raw material is held in a chuck and rotated at high speeds. The cutting tool removes material from the outer diameter or inner diameter (in the case of boring) of the workpiece, shaping it into the desired form.
Key characteristics of CNC turning include:
- Rotation of the Workpiece: The workpiece spins around its axis.
- Stationary Cutting Tool: The cutting tool moves in a linear path along the workpiece.
- Cylindrical Parts Production: Ideal for creating components with rotational symmetry.
- High Precision and Speed: Capable of producing precise CNC turned parts efficiently.
Common products made through CNC turning are shafts, bushings, knobs, pulleys, and other cylindrical components.
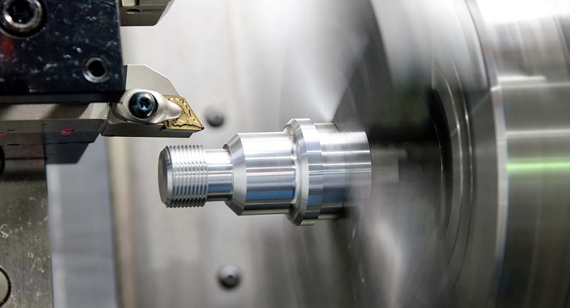
How CNC Turning Works?
In CNC turning, the process begins with securing the workpiece in the chuck of a CNC lathe. The lathe spins the workpiece at a predetermined speed, while a stationary single-point cutting tool moves along axes to remove material and shape the part.
Process Steps:
- Mounting the Workpiece: The raw material is clamped into the chuck.
- Programming the CNC Machine: Instructions are fed into the CNC control unit, dictating tool paths, speeds, and feeds.
- Rotating the Workpiece: The lathe spins the workpiece at high speeds.
- Material Removal: The cutting tool advances along the workpiece, removing material to achieve the desired diameter and shape.
- Finishing Operations: Additional processes like threading, knurling, or drilling may be performed.
- Part Removal: Once machining is complete, the part is removed for inspection and finishing.
Key Points:
- Axes Movement: Typically involves X and Z axes; some advanced lathes include Y-axis movement.
- Tool Turret: Holds multiple tools for various operations without the need to change setups.
- Precision Control: CNC systems allow for tight tolerances and repeatability.
CNC Turning Processes
CNC turning encompasses a variety of processes that can be performed on a lathe. Each process serves a specific purpose in shaping the workpiece to meet precise specifications.
Drilling
- Purpose: Create holes along the axis of the workpiece.
- Process: A drill bit advances into the rotating workpiece, forming a concentric hole.
- Applications: Creating bores for shafts, fasteners, or fluid channels.
Boring
- Purpose: Enlarge an existing hole or cavity.
- Process: A boring tool removes material from the inside diameter to achieve the desired size and finish.
- Applications: Precision fitting of mating parts, like bearings or bushings.
Slotting
- Purpose: Cut slots or grooves into the workpiece.
- Process: A specialized tool removes material in a linear path, forming slots.
- Applications: Keyways, splines, or retaining features.
Parting
- Purpose: Separate a finished part from the raw material.
- Process: A parting tool cuts into the workpiece until it severs the finished piece.
- Applications: Mass production where multiple parts are machined from a single bar.
Facing
- Purpose: Create a flat surface perpendicular to the workpiece's axis.
- Process: The cutting tool moves across the end of the rotating workpiece.
- Applications: Preparing the end of a part for further machining or as a finished surface.
Knurling
- Purpose: Produce a textured pattern on the surface for grip.
- Process: A knurling tool presses into the rotating workpiece, forming a pattern.
- Applications: Handles, knobs, or any part requiring enhanced grip.
Threading
- Purpose: Create helical grooves for fastening purposes.
- Process: A threading tool follows a precise path along the rotating workpiece to form threads.
- Applications: Screws, bolts, threaded shafts, and nuts.
What Makes Up a CNC Lathe?
A CNC lathe is a complex machine composed of various components that work in harmony to perform precise turning operations. Understanding these components is essential for optimizing performance and maintenance.
Chuck
- Function: Holds and rotates the workpiece.
- Types: Three-jaw chucks (self-centering), four-jaw chucks (independent adjustment), collet chucks.
Tool Holder
- Function: Secures the cutting tools.
- Features: Mounted on a turret or tool post for rapid tool changes.
Carriage
- Function: Supports and moves the tool holder along the bed.
- Components: Includes cross-slide and saddle for X and Z-axis movement.
Lateral Slide
- Function: Allows the cutting tool to move laterally (perpendicular to the workpiece axis).
- Purpose: Enables precise control over cutting depth.
Spindle Box (Headstock)
- Function: Houses the main spindle that rotates the workpiece.
- Components: Includes gears, bearings, and drive systems.
Tailstock
- Function: Provides additional support for the workpiece, especially long or slender parts.
- Uses: Can hold tools like drills or reamers for axial operations.
Bed
- Function: The base of the lathe, providing structural support and alignment.
- Characteristics: Must be rigid and precisely machined for accuracy.
Control Panel
- Function: Interface for operating the CNC machine.
- Features: Displays, keypads, and emergency stop controls.
Advantages and Limitations of CNC Turning
CNC tuning offers numerous benefits but also has certain limitations. Understanding these can help in selecting the appropriate machining process for your project.
Advantages of CNC Turning
- High Precision: Capable of achieving tight tolerances.
- Efficiency: Faster production rates due to automated tool changes and rapid movement.
- Versatility: Handles a wide range of materials and part sizes.
- Repeatability: Consistent production of identical parts.
- Reduced Labor Costs: Automation reduces the need for manual intervention.
Limitations of CNC Turning
- Geometric Constraints: Primarily suited for parts with rotational symmetry.
- Initial Setup Cost: CNC lathes can be expensive to acquire and set up.
- Complexity Limitations: Less effective for parts with intricate non-cylindrical features.
- Material Waste: CNC Turning operations can produce significant waste material.
Different Types of Materials That Can Be Used for CNC Turning
CNC turning accommodates a wide array of materials, allowing for flexibility in manufacturing. Material selection depends on the application, required properties, and cost considerations.
Plastics
- Examples: ABS, Nylon, Polycarbonate.
- Properties: Lightweight, corrosion-resistant, easy to machine.
- Applications: Prototypes, bushings, insulators.
Iron
- Properties: Strong, durable, good wear resistance.
- Applications: Engine components, heavy machinery parts.
Titanium
- Properties: High strength-to-weight ratio, corrosion-resistant.
- Applications: Aerospace components, medical implants.
Aluminum
- Properties: Lightweight, excellent machinability, good thermal conductivity.
- Applications: Automotive parts, aerospace components, CNC machined parts.
Stainless Steel
- Properties: Corrosion-resistant, strong, heat-resistant.
- Applications: Medical devices, food processing equipment.
Copper
- Properties: Excellent electrical and thermal conductivity.
- Applications: Electrical components, heat exchangers.
Brass
- Properties: Good machinability, corrosion-resistant, aesthetic appeal.
- Applications: Fittings, valves, decorative parts.
Steel
- Properties: Strong, versatile, available in various alloys.
- Applications: Shafts, gears, structural components.
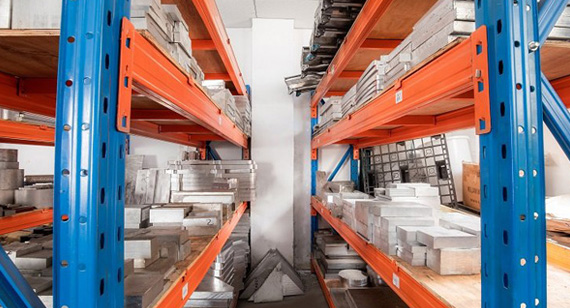
What Is CNC Milling?
CNC milling is a machining process where a rotating cutting tool moves around a stationary workpiece, removing material to create the desired shape. Unlike turning, the workpiece does not rotate. CNC milling machines can move the cutting tool along multiple axes, allowing for complex and intricate part geometries.
Key characteristics of CNC milling include:
- Stationary Workpiece: The material remains fixed on the machine table.
- Rotating Cutting Tool: The cutting tool spins and moves along various axes.
- Complex Shapes: Capable of producing parts with intricate features and geometries.
- Multi-Axis Movement: Machines can operate along X, Y, Z axes and beyond.
Common products made through CNC milling are brackets, housings, molds, and components with complex surfaces.
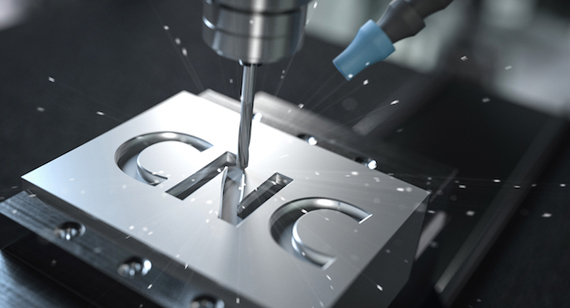
How CNC Milling Works?
In CNC milling, the process involves securing the workpiece on the machine table and using a rotating cutting tool to remove material.
Process Steps:
- Mounting the Workpiece: The raw material is clamped onto the machine table.
- Programming the CNC Machine: Instructions are inputted into the CNC system, defining tool paths, speeds, and feeds.
- Tool Selection: Appropriate cutting tools are chosen based on the material and desired features.
- Material Removal: The rotating cutting tool moves along programmed paths, removing material.
- Multiple Operations: Tools can be changed automatically to perform various operations like drilling, tapping, and engraving.
- Part Removal: After machining, the part is removed for inspection and finishing.
Key Points:
- Axes Movement: Typically involves movement along X, Y, and Z axes; advanced machines include additional axes (A, B).
- Tool Changer: Automated systems switch tools as needed without manual intervention.
- Precision Control: CNC systems enable high precision and repeatability.
CNC Milling Processes
CNC milling encompasses various processes, each suited for specific tasks and features.
Face CNC Milling
- Purpose: Produce flat surfaces on the workpiece.
- Process: The cutting tool moves perpendicular to its axis, removing material from the surface.
- Applications: Creating smooth finishes on large, flat areas.
Angle CNC Milling
- Purpose: Create angled features or surfaces.
- Process: The cutting tool is tilted relative to the workpiece.
- Applications: Bevels, chamfers, and angled surfaces.
Plane CNC Milling
- Purpose: Remove material across a plane parallel to the workpiece.
- Process: The tool moves along a flat plane, cutting horizontally.
- Applications: Leveling surfaces, reducing thickness.
End CNC Milling
- Purpose: Produce pockets, slots, and complex contours.
- Process: An end mill cuts into the workpiece vertically and horizontally.
- Applications: Cavities, profiles, CNC milled parts with intricate details.
Contour CNC Milling
- Purpose: Follow a curved path to create complex shapes.
- Process: The tool moves along a predefined contour.
- Applications: 3D surfaces, molds, and dies.
Drilling and Tapping
- Purpose: Create holes and threads.
- Process: Drills and taps are used to form holes and internal threads.
- Applications: Bolt holes, threaded inserts.
Engraving
- Purpose: Add text or designs onto the workpiece.
- Process: A fine cutting tool etches patterns onto the surface.
- Applications: Branding, part identification.
What Makes Up a CNC Milling Machine?
A CNC milling machine consists of various components that work together to perform precise milling operations.
Spindle
- Function: Holds and rotates the cutting tool.
- Features: High-speed rotation, precision bearings.
Table
- Function: Supports and secures the workpiece.
- Features: Movable along the X and Y axes.
Ram
- Function: Supports the spindle head.
- Features: Allows vertical movement (Z-axis).
Arbor
- Function: Holds the cutting tool when it's not directly mounted in the spindle.
- Uses: Accommodates larger tools or those requiring additional support.
Column
- Function: Supports the machine's components and houses the spindle motor.
- Features: Provides structural integrity.
Knee
- Function: Supports the table and allows vertical movement.
- Features: Adjusts the table's position relative to the spindle.
Saddle
- Function: Sits atop the knee and moves the table along the Y-axis.
- Features: Enables precise positioning.
Cutting Tool
- Function: Removes material from the workpiece.
- Types: End mills, face mills, drills, taps.
Control Panel
- Function: Interface for operating the CNC machine.
- Features: Displays, keypads, programming interfaces.
Advantages and Limitations of CNC Milling
CNC milling offers numerous advantages but also has certain limitations that should be considered.
Advantages of CNC Milling
Precision and Accuracy
- High Tolerances: Achieves tight dimensional accuracy.
- Complex Geometries: Capable of producing intricate shapes.
Versatility
- Material Range: Works with metals, plastics, and composites.
- Various Operations: Drilling, tapping, contouring, and more.
Efficiency
- Automated Tool Changes: Reduces downtime.
- High-Speed Machining: Increases production rates.
Reduced Labor Intensity
- Automation: Minimizes manual intervention.
- Consistency: Produces uniform parts.
Repeatability
- Consistency Across Batches: Ensures identical parts in mass production.
Complexity
- Multi-Axis Capability: Creates parts with undercuts and complex surfaces.
Limitations of CNC Milling
- Cost: High initial investment for machinery.
- Material Waste: Subtractive process can result in significant waste.
- Size Limitations: Workpiece size is limited by machine dimensions.
- Setup Time: Complex setups can be time-consuming.
Different Types of Materials That Can Be Used for CNC Milling
CNC milling's versatility extends to a broad range of materials.
Plastics
- Examples: Acrylic, Delrin, PVC.
- Properties: Lightweight, machinable, insulating.
Iron
- Properties: Durable, good wear resistance.
- Applications: Heavy machinery parts.
Titanium
- Properties: Strong, lightweight, corrosion-resistant.
- Applications: Aerospace, medical implants.
Aluminum
- Properties: Excellent machinability, lightweight.
- Applications: Automotive parts, enclosures, CNC machined parts.
Stainless Steel
- Properties: Corrosion-resistant, strong.
- Applications: Food processing equipment, medical devices.
Copper
- Properties: Excellent conductivity.
- Applications: Electrical components, heat sinks.
Brass
- Properties: Good machinability, aesthetic appeal.
- Applications: Musical instruments, fittings.
Steel
- Properties: Strong, versatile.
- Applications: Structural components, gears.
CNC Milling vs. CNC Turning: What's the Difference?
While both CNC milling and turning are essential machining processes, they differ fundamentally in operation and application.
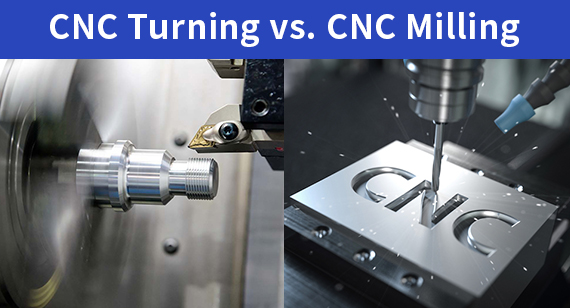
Key Differences:
Workpiece Movement:
- CNC Turning: Workpiece rotates.
- CNC Milling: Workpiece remains stationary.
Tool Movement:
- CNC Turning: Cutting tool moves linearly.
- CNC Milling: Cutting tool rotates and moves around the workpiece.
Suitable Shapes:
- CNC Turning: Ideal for cylindrical parts.
- CNC Milling: Suitable for complex, non-cylindrical geometries.
Some Other Notable Differences Between CNC Turning and CNC Milling:
Direction
- CNC Turning: Circular motion of the workpiece.
- CNC Milling: Multi-directional movement of the cutting tool.
Tool Function
- CNC Turning: Single-point cutting tool removes material.
- CNC Milling: Multi-point cutting tools remove material.
Machining Operation
- CNC Turning: Primarily reduces diameter.
- CNC Milling: Can remove material from various planes and angles.
Shapes Created
- CNC Turning: Cylindrical, conical, and spherical shapes.
- CNC Milling: Complex 3D shapes, flat surfaces, slots.
Material Selection
- CNC Turning: Best for materials that can withstand rotational forces.
- CNC Milling: Suitable for a wider range of materials.
Tool Features
- CNC Turning: Simpler tool geometry.
- CNC Milling: More complex tool designs.
Purpose
- CNC Turning: Reducing external diameter or boring internal surfaces.
- CNC Milling: Creating complex shapes and features.
Cutting
- CNC Turning: Continuous cutting.
- CNC Milling: Intermittent cutting due to tool rotation.
Chip Cutting
- CNC Turning: Produces continuous chips.
- CNC Milling: Produces discontinuous chips.
Thinning Volume
- CNC Turning: Material removal is along the length.
- CNC Milling: Material removal can be localized or across surfaces.
CNC Milling vs. CNC Turning: When to Choose the Right Process?
Selecting between CNC milling and turning depends on the part's design, material, and production requirements.
When to Choose CNC Milling?
- Complex Geometries: Parts with intricate shapes and features.
- Flat Surfaces and Slots: Components requiring precise flatness.
- Multiple Features: When drilling, tapping, and contouring are needed.
- Prototyping: Quick setup for CNC prototype machining.
When to Choose CNC Turning?
- Cylindrical Parts: Shafts, rods, and similar shapes.
- High Volume: Efficient for mass production of turned parts.
- Symmetrical Objects: Parts requiring rotational symmetry.
- Tight Tolerances on Diameters: Precision in external and internal diameters.
Multi-Axis CNC Milling and CNC Turning
Advancements in CNC technology have led to multi-axis machines, enhancing capabilities and efficiency.
Multi-Axis CNC Milling
Multi-axis milling machines can move the cutting tool or the workpiece along multiple axes beyond the standard three.
Advanced Motion
- Five-Axis Machines: Add rotation around the X and Y axes.
- Complex Tool Paths: Enable undercuts and complex surfaces.
Complex Geometry
- Applications: Aerospace components, medical implants.
- Benefits: Reduced setups, increased accuracy.
Applications
- Mold Making: Complex molds and dies.
- Automotive: Engine components with intricate designs.
Multi-Axis CNC Turning
Multi-axis turning centers combine milling and turning capabilities.
Extended Motion
- Y-Axis Addition: Allows off-center milling and drilling.
- Sub-Spindles: Enable machining on both ends without re-clamping.
Multi-Function Operations
- Benefits: Consolidates multiple operations into one machine.
- Efficiency: Reduces handling and setup times.
Applications
- Complex Turned Parts: With milled features.
- Medical Devices: Screws and implants requiring both turning and milling.
CNC Milling vs. CNC Turning – Applications in Custom Part Manufacturing
Both CNC milling and turning play pivotal roles in custom CNC machining, catering to various industries and applications.
CNC Milling Applications
- Aerospace: Structural components, brackets, housings.
- Automotive: Engine parts, gears, prototypes.
- Engine Parts: Pistons, cylinder heads.
- Gears: Complex gear profiles.
- Accessories: Custom fixtures and tools.
- Medical Devices: Surgical instruments, implants.
- Brackets: Mounting components.
- Housings: Enclosures for electronics.
- Pumps: Impellers, casings.
- Electronics: Heat sinks, circuit board housings.
- Mold Making: Injection molds, casting patterns.
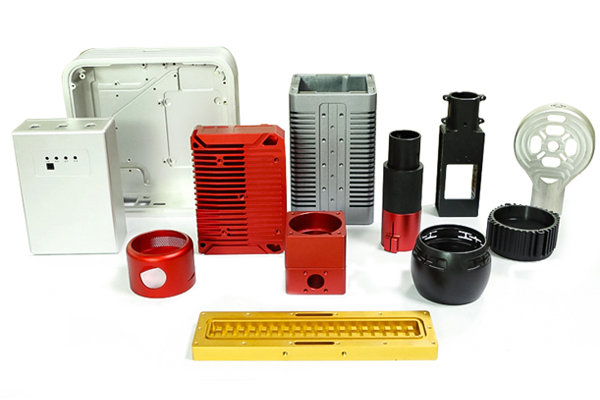
CNC Turning Applications
- Automotive: Shafts, axles, hubs.
- Medical: Orthopedic implants, surgical screws.
- Aerospace: Turbine components, bushings.
- Oil & Gas: Valves, fittings.
- Consumer Goods: Pens, knobs.
- Round Shafts: Drive shafts, rollers.
- Nozzles: Spray nozzles, jet components.
- Firearms: Barrels, suppressors.
- Ball Joints: Automotive suspension parts.
- Rollers: Conveyor components.
- Turbines: Rotors, blades.
- Flanges: For beams, pipes, and more.
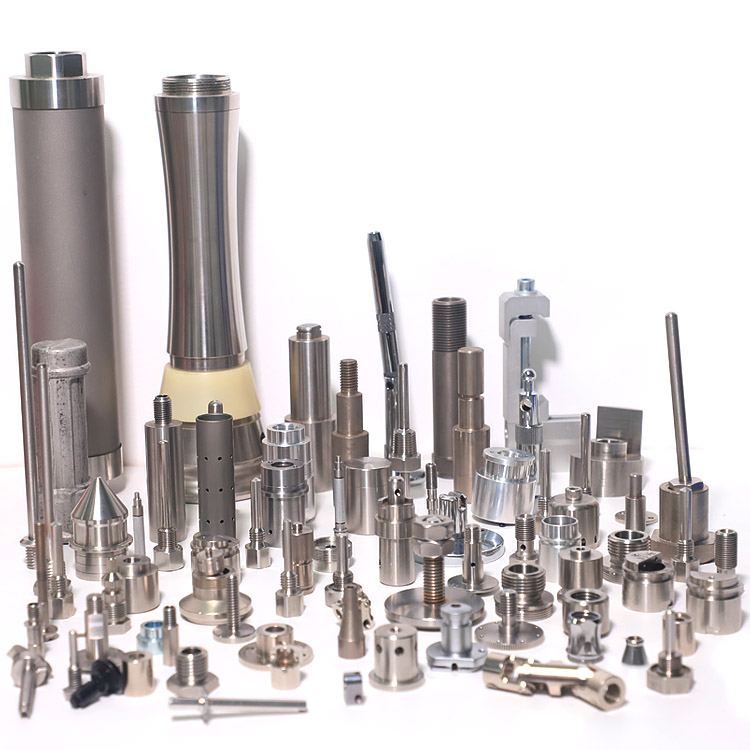
Need CNC Milling or Need CNC Turning: VMT Can Handle Both
At VMT, we specialize in providing comprehensive CNC machining services, offering both CNC milling and turning capabilities. Our state-of-the-art CNC machining factory is equipped to handle projects of any complexity.
Why Choose VMT?
- Expertise: Skilled technicians proficient in both milling and turning.
- Advanced Equipment: Multi-axis machines for complex parts.
- Quality Assurance: Strict quality control for CNC turned parts and CNC milled parts.
- Custom Solutions: Tailored services for custom CNC machining needs.
- Rapid Prototyping: Efficient CNC prototype machining for quick turnaround.
Whether you require precision-turned components or intricately milled parts, VMT has the capabilities and experience to deliver exceptional results.
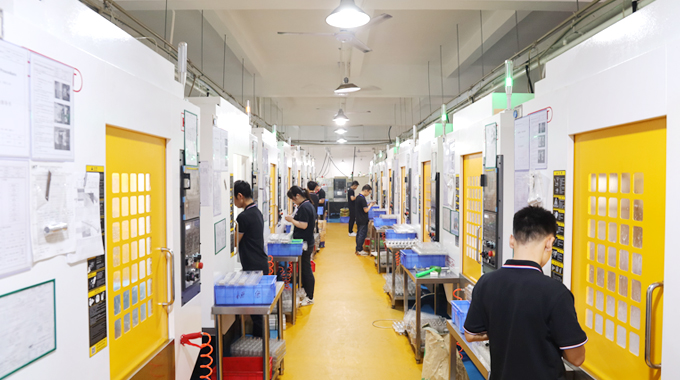
Conclusion
Understanding the differences between CNC turning and milling is essential for selecting the appropriate machining process for your project. CNC turning is ideal for producing cylindrical parts with rotational symmetry, offering high precision and efficiency. In contrast, CNC milling excels at creating complex, non-cylindrical geometries with intricate features.
Both processes have their advantages and limitations, but advancements in multi-axis machines have expanded their capabilities. By leveraging the strengths of each method, manufacturers can optimize production, reduce costs, and achieve superior quality in CNC machined parts.
Whether you're in aerospace, automotive, medical, or any industry requiring precision components, knowing when to use CNC turning or milling will enhance your manufacturing outcomes.
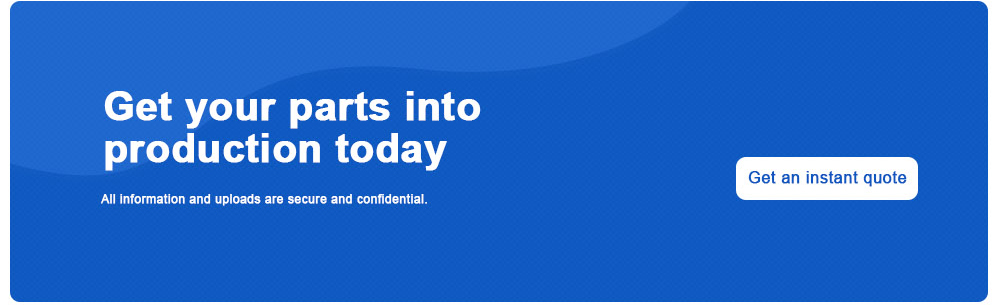
FAQs
What Is the Difference Between CNC Turning and Grinding?
CNC Turning:
- Process: Involves rotating the workpiece while a stationary cutting tool removes material.
- Purpose: Shapes the workpiece into a desired form, typically cylindrical.
Grinding:
- Process: Uses a rotating abrasive wheel to remove material from the workpiece's surface.
- Purpose: Achieves a high-quality surface finish and tight tolerances.
Difference:
- Material Removal: CNC Turning removes larger amounts of material; grinding is for fine finishing.
- Applications: CNC Turning shapes the part; grinding refines the surface.
Which Is Better? Lathe or CNC Milling?
Lathe (CNC Turning):
- Advantages: Ideal for cylindrical parts, faster for round components.
- Limitations: Limited to parts with rotational symmetry.
CNC Milling Machine:
- Advantages: Capable of producing complex shapes and features.
- Limitations: May be slower for simple cylindrical parts.
Conclusion: Neither is inherently better; the choice depends on the part geometry and production needs.
Is CNC Turning Cheaper Than CNC Milling?
CNC Turning:
- Cost-Effective: Generally faster for cylindrical parts, reducing labor costs.
CNC Milling:
- Complexity Costs: More suitable for complex parts, which may increase machining time and costs.
- Overall: For simple, round parts, turning is often cheaper. For complex geometries, milling may be more cost-effective despite longer machining times.
What Are the Similarities Between CNC Milling and CNC Turning?
- CNC Control: Both use computer numerical control for precision.
- Material Removal: Both are subtractive processes removing material to shape the part.
- Tooling: Require cutting tools appropriate for the material and operation.
- Automation: Capable of automated production with minimal manual intervention.
Which Is Better, CNC Lathe or CNC Milling?
CNC Lathe:
- Best For: Cylindrical parts requiring rotational symmetry.
CNC Milling Machine:
- Best For: Complex parts with various features and geometries.
- Decision: Depends on the part's design and required features.
What Are Two Disadvantages of CNC Milling or CNC Turning Compared to Producing Parts by Hand?
- High Initial Investment: CNC machines are expensive to purchase and set up.
- Less Flexibility for One-Offs: Not cost-effective for very small production runs or highly customized, unique parts that may be quicker to produce by hand.
What Is the CNC Turning Process?
CNC turning involves rotating the workpiece while a cutting tool removes material along the desired profile. The CNC system controls the movement of the tool and rotation speed, allowing for precise shaping of cylindrical parts.
What Is Grinding in CNC Machines?
Grinding in CNC machines uses a rotating abrasive wheel to remove material and achieve a high surface finish and tight tolerances. It's typically used for finishing operations after initial shaping processes like turning or milling.
What Are the Alternatives to CNC Milling?
- 3D Printing: Additive manufacturing for complex geometries.
- Laser Cutting: For flat sheet materials.
- Waterjet Cutting: Cold cutting process suitable for various materials.
- Manual Machining: For simple parts or very low-volume production.
What Is the Biggest Disadvantage of Using CNC?
The most significant disadvantage is the high initial cost of CNC machinery and the need for skilled operators and programmers, which can be a barrier for small businesses.
What Materials Cannot Be CNC Machined?
- Brittle Materials: Such as glass or some ceramics, which may crack under machining forces.
- Soft Rubbers: May deform rather than cut cleanly.
- Composite Materials: With varying hardness may pose challenges.
What Is the Life Expectancy of a CNC Milling Machine?
With proper maintenance, a CNC milling machine can last 15 to 20 years or more. Longevity depends on usage intensity, maintenance practices, and technological advancements.
Why Are CNC Milling Machines So Expensive?
CNC milling machines are expensive due to their complex mechanical components, precision engineering, advanced control systems, and the integration of high-quality materials to ensure accuracy and durability.
By comprehensively understanding CNC turning and milling, you can make informed decisions that optimize your manufacturing processes, whether you're producing CNC turned parts, CNC milled parts, or seeking expert CNC machining services.