Are you seeking a method to machine steel with unparalleled precision and efficiency? Frustrated by traditional machining techniques that limit your production quality and output? You're not alone. Many manufacturers grapple with achieving high-quality steel components while keeping costs and lead times in check. But what if there was a solution that could revolutionize your machining processes, offering exceptional accuracy and versatility? Enter CNC steel machining—a cutting-edge approach that can transform your manufacturing operations.
CNC steel machining is a computer-controlled manufacturing process that precisely cuts, shapes, and finishes steel parts using various machining operations. This method offers high accuracy, repeatability, and the ability to produce complex geometries, making it ideal for industries requiring precise steel components.
Now that we've highlighted the transformative potential of CNC steel machining, let's delve deeper into how this technology works, the key operations involved, and how it can be leveraged to meet your specific project requirements. Understanding these aspects will empower you to make informed decisions and optimize your manufacturing processes.
What Is CNC Steel Machining?
CNC steel machining refers to the use of Computer Numerical Control (CNC) machines to manufacture steel parts with high precision and efficiency. By utilizing pre-programmed software and code, CNC machines control complex machinery, such as lathes, mills, routers, and grinders, to cut and shape steel into desired forms. This automated process reduces human error, increases production speed, and allows for the creation of intricate designs that would be challenging with manual machining.

Key characteristics of CNC steel machining include:
- High Precision and Accuracy: Achieving tolerances as tight as ±0.001 inches.
- Repeatability: Consistent production of identical parts.
- Complex Geometries: Ability to machine intricate shapes and features.
- Versatility: Applicable to a wide range of steel grades and alloys.
- Efficiency: Faster production times compared to traditional methods.
CNC steel machining is essential in industries such as automotive, aerospace, medical devices, and industrial machinery, where precision and reliability are paramount.
How Does CNC Steel Machining Work?
CNC steel machining operates by converting computer-aided design (CAD) models into numerical code that controls the movement and operation of machining tools. Here's an overview of the process:
- Design and Programming: Engineers create a 3D model of the part using CAD software. This model is then imported into computer-aided manufacturing (CAM) software, which generates the G-code—a series of commands that direct the CNC machine's movements and operations.
- Machine Setup: Operators prepare the CNC machine by installing the appropriate cutting tools and fixtures. The steel workpiece is secured in place, ensuring stability during machining.
- Machining Operations: The CNC machine executes the programmed instructions, performing various operations such as cutting, drilling, milling, and turning to shape the steel part.
- Quality Inspection: After machining, the part undergoes inspection using precision measuring tools or coordinate measuring machines (CMM) to verify that it meets the specified dimensions and tolerances.
- Finishing Processes: Depending on the requirements, the part may receive additional treatments like surface finishing, heat treatment, or coating to enhance its properties.
By automating the machining process, CNC technology minimizes human intervention, reduces errors, and increases production efficiency, making it a vital component of modern manufacturing.
What Are the Key Operations in CNC Steel Machining?
CNC steel machining encompasses a variety of operations, each serving a specific purpose in shaping and finishing steel components. Understanding these operations helps in selecting the most appropriate methods for your project.
Cutting Processes
CNC Turning
Turning is a machining process where a cutting tool moves linearly while the workpiece rotates. It's typically performed on a lathe and is used to create cylindrical parts by removing material from the outer diameter.
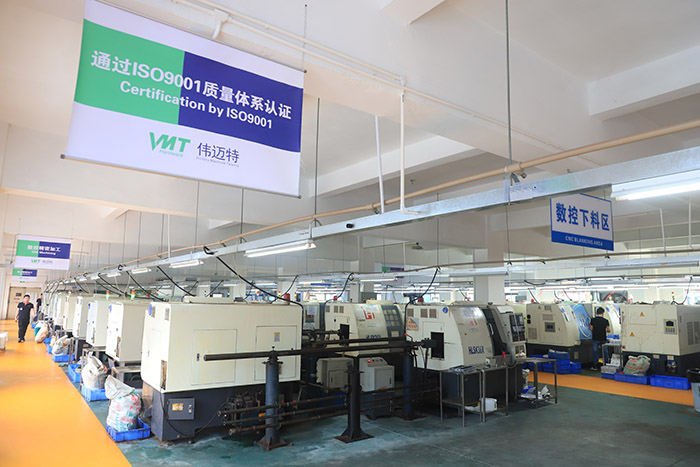
Advantages
- High precision and excellent surface finish.
- Suitable for producing symmetrical parts.
- Efficient for high-volume production.
Applications
- Shafts and axles.
- Rollers and cylinders.
- Threaded components.
CNC Milling
Milling involves the use of rotating multi-point cutting tools to remove material from a stationary workpiece. CNC mills can move the tool and/or the workpiece in multiple axes to create complex shapes and features.
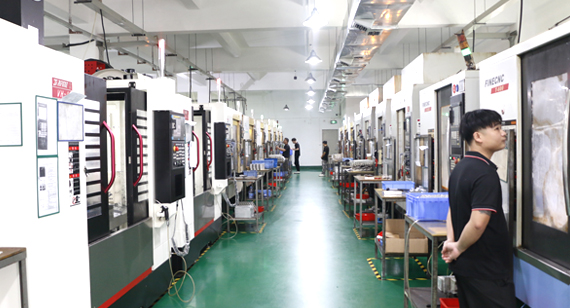
Advantages
- Capable of producing complex geometries.
- High versatility and flexibility.
- Suitable for both small and large production runs.
Applications
- Engine components.
- Mold and die manufacturing.
- Precision machinery parts.
CNC Drilling
Drilling is the process of creating round holes in a workpiece using a rotating drill bit. CNC drilling machines can precisely position and drill holes of various sizes and depths.
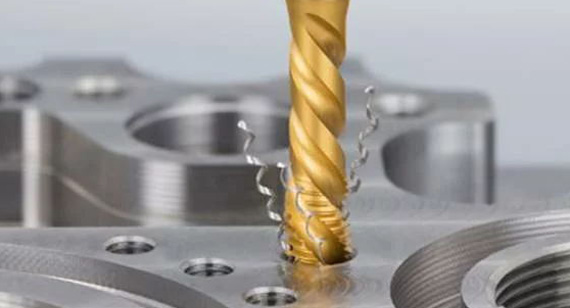
Advantages
- High-speed operation increases productivity.
- Accurate hole placement and dimensions.
- Suitable for mass production.
Applications
- Bolt holes and fastener points.
- Fluid and gas passages.
- Assembly and mounting features.
Tapping
Tapping creates internal threads within a pre-drilled hole using a tool called a tap. CNC tapping ensures consistent thread quality and pitch.
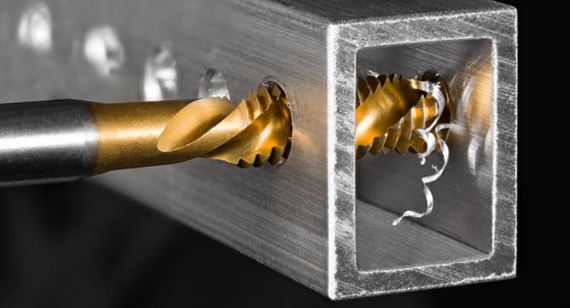
Advantages
- Precise and uniform threading.
- Increased production speed.
- Reduced risk of tap breakage due to controlled feed rates.
Applications
- Threaded holes for screws and bolts.
- Mechanical assemblies.
- Hydraulic and pneumatic components.
Grinding
Grinding uses an abrasive wheel to remove material and achieve a high surface finish and tight tolerances. It's ideal for finishing operations on hardened steel parts.
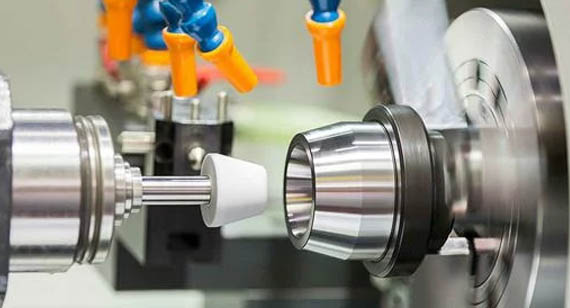
Advantages
- Achieves extremely tight tolerances.
- Produces superior surface finishes.
- Capable of machining hard materials.
Applications
- Precision shafts and spindles.
- Bearing surfaces.
- Tool and die components.
Electrical Discharge Machining (EDM)
EDM is a non-contact machining process that removes material using electrical discharges (sparks) between an electrode and the workpiece submerged in a dielectric fluid.
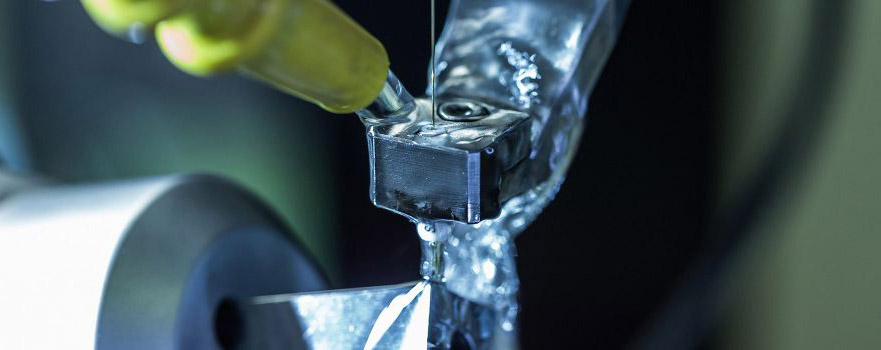
Advantages
- Machines complex shapes and hard materials.
- No mechanical stresses on the part.
- High precision and fine detail capabilities.
Applications
- Injection molds and dies.
- Intricate cavities and thin walls.
- Aerospace and medical components.
Laser Cutting
Laser cutting employs a high-powered laser beam to melt, burn, or vaporize material, creating precise cuts in steel plates and sheets.
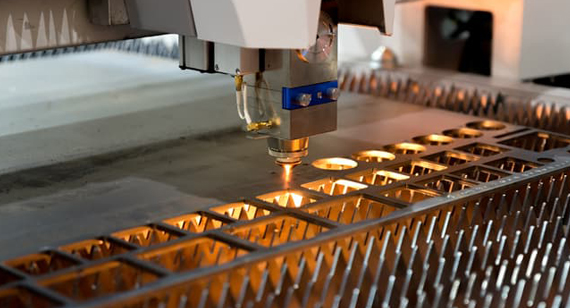
Advantages
- High precision and minimal material waste.
- Non-contact process reduces workpiece distortion.
- Capable of cutting complex shapes and small features.
Applications
- Sheet metal fabrication.
- Decorative metalwork.
- Electronic enclosures.
Waterjet Cutting
Waterjet cutting uses a high-pressure stream of water mixed with abrasive particles to cut materials without generating heat.
Advantages
- No heat-affected zones prevent material distortion.
- Can cut virtually any material, including hardened steel.
- Environmentally friendly with no hazardous fumes.
Applications
- Architectural components.
- Custom machine parts.
- Automotive and aerospace parts.
Forming Processes
Bending
Bending is a forming process where force is applied to a steel workpiece to create a desired angle or curvature without removing material.
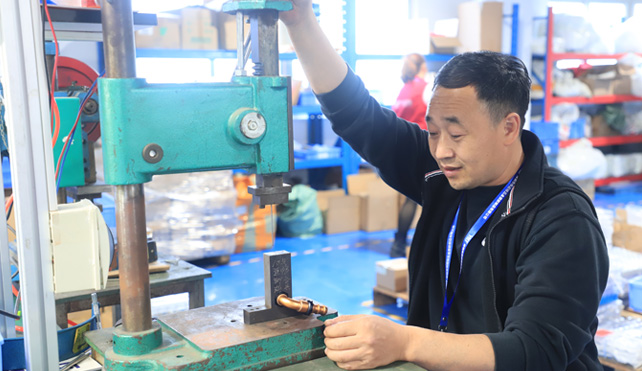
Advantages
- Maintains material integrity with no seams.
- Produces a variety of angles and shapes.
- Cost-effective for high-volume production.
Applications
- Structural frames.
- Brackets and supports.
- Tubing and piping systems.
Stamping
Stamping uses a press and die to shape or cut steel sheets into specific forms. It's ideal for producing large quantities of parts with consistent quality.
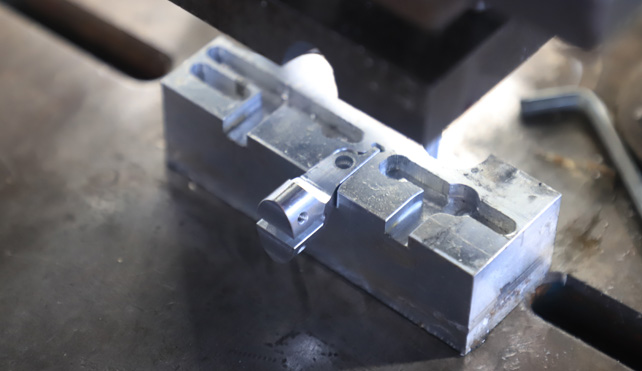
Advantages
- High-speed production.
- Precise and consistent part dimensions.
- Suitable for thin materials.
Applications
- Automotive body panels.
- Electronic components.
- Household appliances.
Rolling
Rolling involves passing steel through one or more pairs of rolls to reduce thickness, improve uniformity, or impart a specific cross-sectional shape.
Advantages
- Enhances mechanical properties.
- Produces continuous lengths of material.
- Reduces material waste.
Applications
- Steel plates and sheets.
- Structural beams.
- Pipes and tubing.
Forging
Forging shapes steel by applying compressive forces through hammering, pressing, or rolling, often at high temperatures.
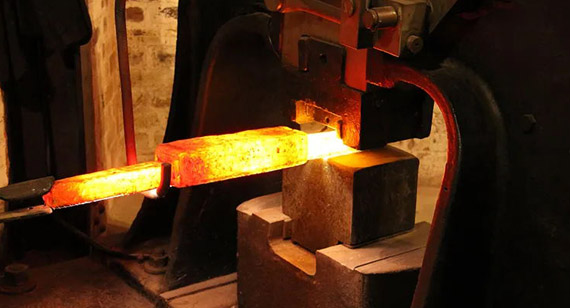
Advantages
- Produces parts with superior strength.
- Refines grain structure for improved mechanical properties.
- Suitable for high-stress applications.
Applications
- Crankshafts and connecting rods.
- Gears and bearings.
- Aerospace components.
Extrusion
Extrusion pushes heated steel through a die to create objects with a fixed cross-sectional profile, such as rods, bars, and complex shapes.
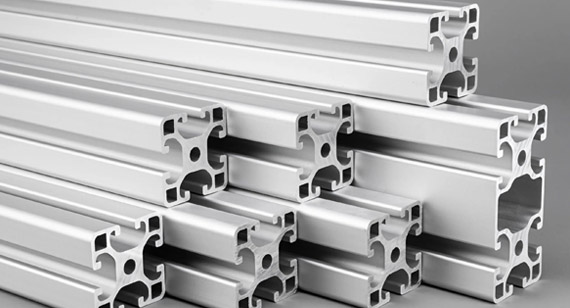
Advantages
- Produces long lengths with consistent cross-sections.
- Capable of creating complex profiles.
- Efficient material utilization.
Applications
- Railings and frames.
- Heat sinks.
- Industrial machinery components.
Deep Drawing
Deep drawing forms flat steel sheets into hollow shapes by pulling the material into a die cavity using a punch.
Advantages
- Creates seamless, hollow parts.
- Suitable for complex shapes and deep cavities.
- High production efficiency.
Applications
- Pressure vessels and tanks.
- Automotive fuel tanks.
- Kitchen sinks and cookware.
What Are the Types of Surface Finishes in CNC Steel Machining?
Surface finish plays a crucial role in the performance, aesthetics, and durability of steel parts. Various finishing processes are available to meet specific requirements.
As-Machined Finish
An as-machined finish refers to the surface condition of a part immediately after CNC machining, without any additional processing.
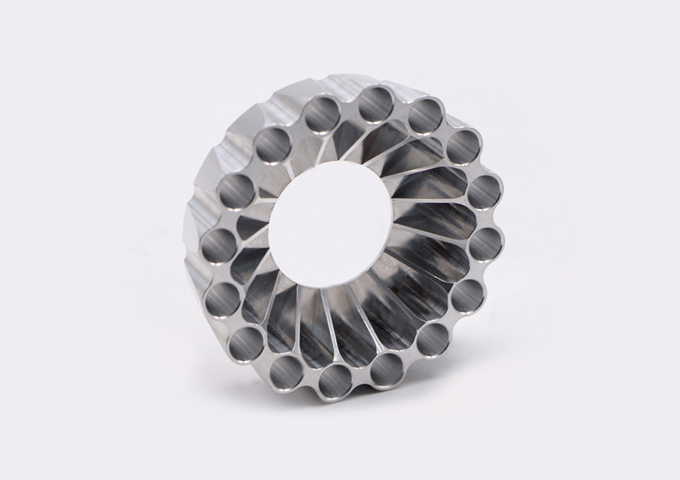
Features
- Visible tool marks and minor imperfections.
- Surface roughness typically ranges from Ra 1.6 to Ra 3.2 μm.
- Economical with no additional processing time or cost.
Applications
- Internal components.
- Parts not requiring high cosmetic appeal.
- Further processing or coating anticipated.
Bead Blasting
Bead blasting propels fine glass beads or other abrasive media against the surface to create a smooth, matte finish.
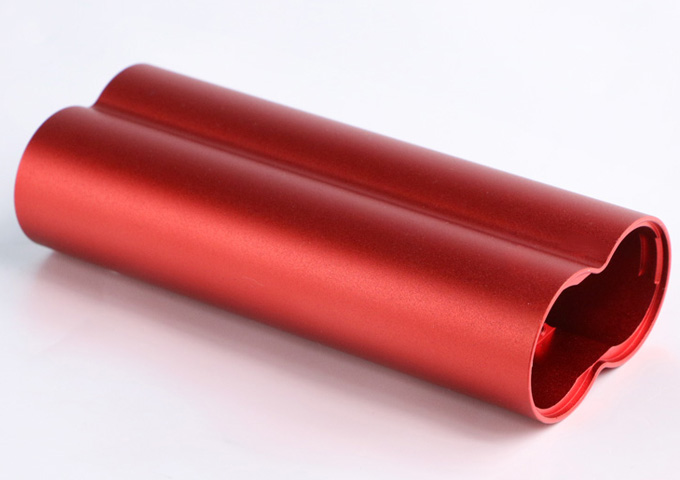
Features
- Uniform matte texture.
- Removes surface imperfections and contaminants.
- Enhances adhesion for coatings.
Applications
- Aesthetic improvement.
- Pre-treatment for painting or coating.
- Non-reflective surfaces.
Anodizing (Type II and Type III Hardcoat)
While anodizing is primarily associated with aluminum, steel can undergo similar processes like black oxide coating to enhance surface properties.

Features
- Type II: Provides corrosion resistance and can be dyed in various colors.
- Type III: Creates a thicker, harder layer for wear resistance.
- Not commonly used on steel; alternative treatments like black oxide are preferred.
Applications
- Decorative finishes.
- Enhanced wear and corrosion resistance.
- Military and aerospace components.
Powder Coating
Powder coating applies a dry powder electrostatically to the steel part, which is then cured under heat to form a durable, protective layer.
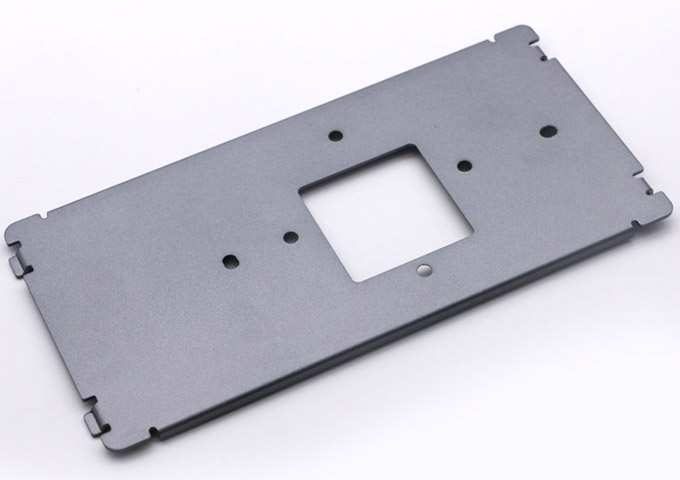
Features
- Thick, uniform coating resistant to chipping and scratching.
- Wide range of colors and textures.
- Environmentally friendly with minimal volatile organic compounds (VOCs).
Applications
- Automotive parts.
- Outdoor equipment.
- Appliances and furniture.
Electroplating
Electroplating deposits a thin layer of metal, such as nickel or chromium, onto the steel surface using an electric current.
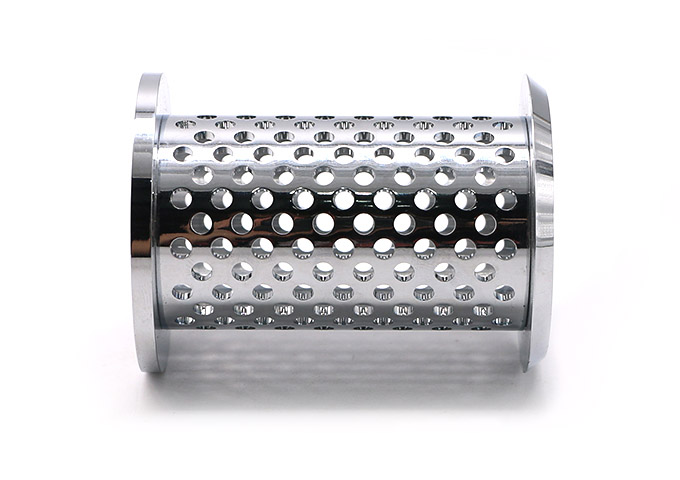
Features
- Improved corrosion resistance.
- Enhanced surface hardness.
- Decorative finish with options for brightness and color.
Applications
- Decorative hardware.
- Electrical components.
- Wear-resistant surfaces.
What Tools Are Needed When Machining Steel in CNC?
Selecting the right tools is essential for successful CNC steel machining. The tools must withstand the hardness and toughness of steel while delivering precision and efficiency.
Cutting Tools
- End Mills: Used for milling operations to create slots, contours, and profiles.
- Drill Bits: Specialized bits for drilling holes in steel, often coated for durability.
- Reamers: Precisely enlarge holes to exact dimensions with a smooth finish.
- Taps and Dies: Create internal and external threads.
- Boring Tools: Enlarge holes with high accuracy.
- Inserts: Replaceable cutting edges made from carbide or ceramic materials.
Tool Holders
- Collets: Securely clamp cutting tools with high concentricity.
- End Mill Holders: Rigidly hold end mills for stable machining.
- Drill Chucks: Versatile holders for various drill bit sizes.
Workholding Devices
- Vices: Clamp smaller workpieces securely.
- Chucks: Hold rotational parts on lathes.
- Fixture Plates: Provide a modular platform for custom fixtures.
- Jigs and Fixtures: Custom-designed to hold parts in specific orientations.
Measuring and Inspection Tools
- Calipers: Measure dimensions with high precision.
- Micrometers: Provide accurate measurements of small distances.
- Gauges: Verify dimensions and tolerances.
- CMM (Coordinate Measuring Machines): Offer precise 3D measurements.
Support Equipment
- CNC Controllers: Manage machine operations and execute G-code.
- CAD/CAM Software: Design parts and generate machining programs.
- Coolant Systems: Provide lubrication and cooling to extend tool life.
- Chip Management Systems: Remove chips from the work area to prevent damage.
Additional Tools and Accessories
- Tool Presetters: Calibrate tool dimensions before machining.
- Deburring Tools: Remove sharp edges and burrs from parts.
- Spindle Speeders: Increase spindle RPM for high-speed machining.
What Types of Steel and Different Steel Grades Are Used in CNC Machining?
Steel comes in various grades and alloys, each offering specific mechanical properties and suitability for different applications. Choosing the right steel type is crucial for achieving desired performance.
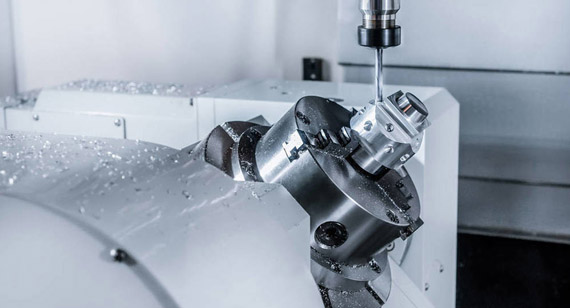
Stainless Steel
Stainless steel contains at least 10.5% chromium, offering excellent corrosion resistance and strength.
- 304 and 316 (Austenitic): Non-magnetic with high corrosion resistance; used in food processing and medical devices.
- 410 (Martensitic): Magnetic and heat-treatable; used in cutlery and valves.
- 430 (Ferritic): Magnetic with moderate corrosion resistance; used in appliances.
- Duplex Stainless Steel: Combines austenitic and ferritic properties; high strength and corrosion resistance.
- 17-4 PH (Precipitation Hardening): High strength and hardness after heat treatment; used in aerospace and chemical processing.
Alloy Steel
Alloy steel includes additional alloying elements like chromium, nickel, and molybdenum to enhance mechanical properties.
- 4130: Chromium-molybdenum alloy with good strength and weldability; used in aircraft structures.
- 4140: High-strength alloy steel suitable for heavy-duty parts; used in shafts and gears.
- 4340: High toughness and fatigue strength; used in aerospace and automotive components.
Carbon Steel
Carbon steel's primary alloying element is carbon, affecting its hardness and strength.
- 1018 (Low Carbon Steel): Good formability and weldability; used in shafts and rods.
- 1020 (Medium Carbon Steel): Balanced strength and ductility; used in mechanical parts.
- 1045 (High Carbon Steel): Higher strength and hardness; used in gears and axles.
Tool Steel
Tool steel is designed for making cutting tools and dies, offering high hardness and wear resistance.
- D2: High-carbon, high-chromium steel; excellent wear resistance; used in dies.
- A2: Air-hardening steel with good dimensional stability; used in punches and tools.
- O1: Oil-hardening steel; easy to machine and heat-treat; used in knives and cutting tools.
High-Speed Steel (HSS)
HSS retains hardness at high temperatures, suitable for cutting tools.
- M2: General-purpose HSS; used in drills and taps.
- T1: High red hardness; used in cutting tools requiring high-temperature resistance.
Specialty Steels
Specialty steels are tailored for specific applications with unique properties.
- A36: Common structural steel; good weldability and mechanical properties.
- A572: High-strength, low-alloy steel; used in construction and bridges.
Steel Grades for CNC Machining
Understanding specific steel grades helps in selecting materials that meet mechanical and performance requirements for CNC machining.
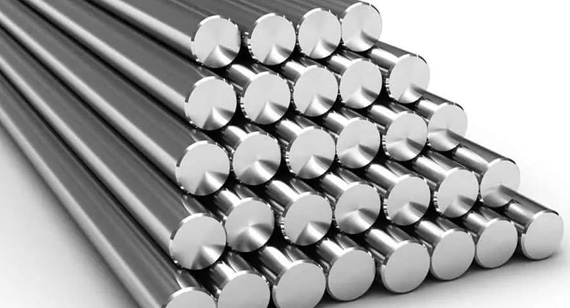
4140 Steel
4140 steel is a chromium-molybdenum alloy known for its high tensile strength and toughness.
Applications
- Shafts and axles.
- Gears and couplings.
- Tooling and fixtures.
Mechanical Properties
- Yield Tensile Strength: 655 MPa
- Shear Modulus: 80 GPa
- Elongation at Break: 20%
- Hardness (Brinell): 197 HB
- Density: 7.85 g/cm³
4130 Steel
4130 steel is a low-alloy steel with good weldability and strength, commonly used in the aerospace industry.
Applications
- Aircraft frames.
- Roll cages.
- Pressure vessels.
Mechanical Properties
- Yield Tensile Strength: 435 MPa
- Shear Modulus: 80 GPa
- Elongation at Break: 25%
- Hardness (Brinell): 156 HB
- Density: 7.85 g/cm³
1018 Steel
1018 steel is a low-carbon steel offering good balance between strength, ductility, and machinability.
Applications
- Fasteners and pins.
- Machine parts.
- Gears and shafts.
Mechanical Properties
- Yield Tensile Strength: 370 MPa
- Shear Modulus: 80 GPa
- Elongation at Break: 15%
- Hardness (Brinell): 126 HB
- Density: 7.85 g/cm³
1045 Steel
1045 steel is a medium-carbon steel known for its strength and hardness after heat treatment.
Applications
- Bolts and studs.
- Crankshafts and connecting rods.
- Machine parts requiring high strength.
Mechanical Properties
- Yield Tensile Strength: 450 MPa
- Shear Modulus: 80 GPa
- Elongation at Break: 12%
- Hardness (Brinell): 163 HB
- Density: 7.85 g/cm³
1215 Steel
1215 steel is a free-machining steel with added sulfur and lead to improve machinability.
Applications
- High-volume screw machine products.
- Fasteners and fittings.
- Components requiring extensive machining.
Mechanical Properties
- Yield Tensile Strength: 350 MPa
- Shear Modulus: 80 GPa
- Elongation at Break: 10%
- Hardness (Brinell): 121 HB
- Density: 7.85 g/cm³
Steel Grades
|
Yield Tensile Strength
|
Shear Modulus
|
Elongation at Break
|
Hardness (Brinell)
|
Density
|
Applications
|
4140 Steel
|
655 MPa
|
80 GPa
|
20%
|
197 HB
|
7.85 g/cm³
|
Shafts and axles.
Gears and couplings.
Tooling and fixtures.
|
4130 Steel
|
435 MPa
|
80 GPa
|
25%
|
156 HB
|
7.85 g/cm³
|
Aircraft frames.
Roll cages.
Pressure vessels.
|
1018 Steel
|
370 MPa
|
80 GPa
|
15%
|
126 HB
|
7.85 g/cm³
|
Fasteners and pins.
Machine parts.
Gears and shafts.
|
1045 Steel
|
450 MPa
|
80 GPa
|
12%
|
163 HB
|
7.85 g/cm³
|
Bolts and studs.
Crankshafts and connecting rods.
Machine parts requiring high strength.
|
1215 Steel
|
350 MPa
|
80 GPa
|
10%
|
121 HB
|
7.85 g/cm³
|
High-volume screw machine products.
Fasteners and fittings.
Components requiring extensive machining.
|
How to Choose the Right Steel for Your Project?
Selecting the appropriate steel grade is critical for meeting performance, cost, and manufacturing requirements.
Application Requirements
- Environmental Conditions: Corrosive environments may require stainless steel.
- Mechanical Stress: Determine the load and stress the part will endure.
- Regulatory Compliance: Adherence to industry standards and certifications.
Mechanical Properties
- Strength: Yield and tensile strength for load-bearing applications.
- Hardness: Resistance to wear and abrasion.
- Toughness: Ability to absorb energy without fracturing.
Corrosion Resistance
- Material Composition: Stainless steels offer superior corrosion resistance.
- Surface Treatments: Coatings and platings can enhance resistance.
Machinability
- Ease of Machining: Free-machining steels reduce production time and cost.
- Tool Wear: Harder materials may require specialized tooling.
Heat Treatment Needs
- Hardening Requirements: Some applications require specific hardness levels.
- Dimensional Stability: Consider potential distortion during heat treatment.
Cost-Effectiveness
- Material Cost: Balance performance with budget constraints.
- Manufacturing Cost: Factor in machining time and tool wear.
What Are the Applications and Use Cases of CNC Steel Machining?
CNC steel machining is pivotal across numerous industries, providing precision and efficiency in producing critical components.
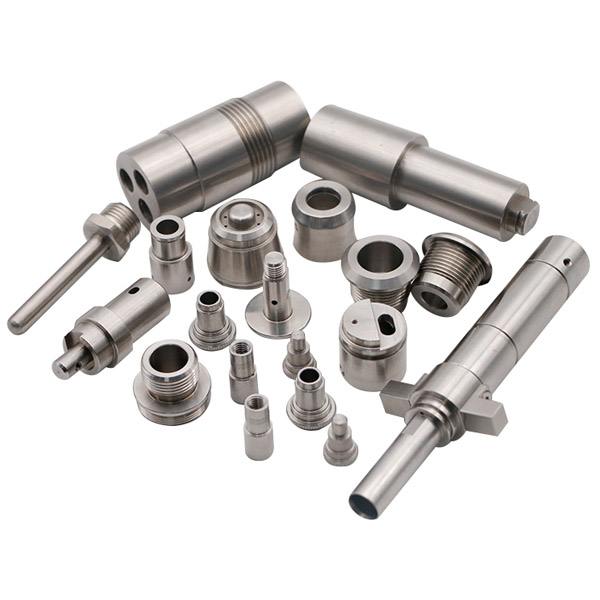
Automotive Industry
- Engine Components: Pistons, crankshafts, and camshafts.
- Transmission Parts: Gears and shafts.
- Structural Elements: Frames and suspension components.
Aerospace Industry
- Aircraft Structures: Fuselage frames and wing components.
- Engine Parts: Turbine blades and casings.
- Landing Gear: Struts and actuators.
Medical Devices
- Surgical Instruments: Scalpels, forceps, and clamps.
- Implants: Orthopedic screws and plates.
- Diagnostic Equipment: MRI and CT scanner components.
Defense and Military
- Weapon Systems: Barrels and receivers.
- Armored Vehicles: Hulls and protective components.
- Communication Equipment: Antenna mounts and enclosures.
Industrial Machinery
Machine Tools: Spindles and guides.
Pumps and Valves: Housings and rotors.
Conveyor Systems: Rollers and chains.
Energy Sector
- Oil and Gas Equipment: Drill bits and pipe fittings.
- Renewable Energy: Wind turbine components and solar panel frames.
- Power Generation: Generator parts and transformer housings.
Electronics and Semiconductors
- Heat Sinks: Efficient thermal management components.
- Enclosures: Protective casings for sensitive electronics.
- Connectors: Precision electrical connections.
Construction and Infrastructure
- Structural Steel: Beams, columns, and supports.
- Architectural Metalwork: Railings and facades.
- Bridges and Tunnels: Critical support components.
Tool and Die Making
- Stamping Dies: For metal forming processes.
- Injection Molds: For plastic part production.
- Cutting Tools: Drills, end mills, and taps.
Consumer Goods
- Kitchenware: Knives and cookware.
- Fitness Equipment: Weights and machine components.
- Outdoor Gear: Bicycle parts and climbing equipment.
Advantages and Challenges of CNC Steel Parts
CNC steel machining offers numerous benefits but also presents certain challenges that must be managed effectively.
Advantages of CNC Steel Machining
Precision and Accuracy
- High Tolerances: Achieving tolerances within microns.
- Consistency: Uniform quality in mass production.
Wide Range of Applications
- Versatility: Suitable for simple to complex parts.
- Material Variety: Applicable to numerous steel grades.
Increased Productivity
- Automation: Reduced manual intervention.
- Fast Turnaround: Quick setup and operation.
Superior Surface Finish
- High-Quality Finish: Reduces need for secondary finishing.
- Improved Aesthetics: Enhances product appeal.
Reduced Material Waste
- Optimized Cutting: Efficient material utilization.
- Cost Savings: Lower raw material expenses.
Customization and Flexibility
- Rapid Prototyping: Accelerates product development.
- Small Batch Production: Economical for limited runs.
Strength and Durability
- High-Quality Parts: Meets demanding application requirements.
- Longevity: Extends product life cycle.
Cost-Effectiveness in Volume Production
- Economies of Scale: Lower unit costs in large quantities.
- Reliability: Minimizes downtime and maintenance.
Challenges of CNC Steel Machining
Material Hardness
- Tool Wear: Accelerated wear requires frequent replacements.
- Machining Difficulty: Requires appropriate tooling and parameters.
Complexity of Programming
- Skill Requirement: Needs experienced programmers.
- Complex Parts: Increases programming and setup time.
Equipment Costs
- High Investment: CNC machines and accessories are expensive.
- Maintenance Expenses: Regular upkeep is necessary.
Skilled Labor Force
- Training Needs: Requires skilled operators and engineers.
- Talent Shortage: Experienced personnel may be scarce.
Thermal Deformation
- Heat Generation: Can cause part distortion.
- Cooling Systems: Effective cooling is essential.
Surface Treatment Challenges
- Additional Processes: Increases production time and cost.
- Quality Control: Ensuring consistent finishes.
Surface Treatment and Post-Processing Options for Steel Parts
Proper surface treatment enhances performance and extends the life of steel parts.
Powder Coating
- Features: Durable, corrosion-resistant coating.
- Applications: Outdoor equipment, automotive parts.
Carburizing
- Features: Hardens the surface for wear resistance.
- Applications: Gears, bearings, cams.
Nickel Plating
- Features: Improves corrosion resistance and appearance.
- Applications: Electronics, decorative parts.
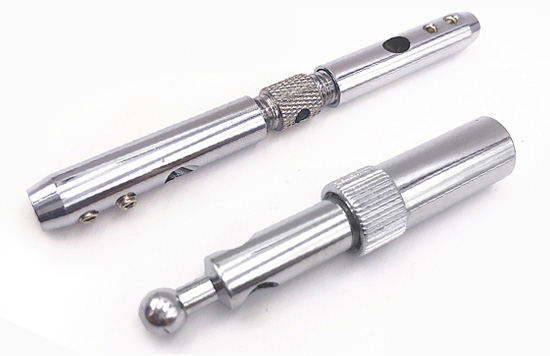
Polishing
- Features: Enhances surface smoothness and shine.
- Applications: Precision components, tools.

Machining Steel vs. Machining Aluminum: What's the Difference?
While both are common metals, steel and aluminum differ significantly in machining characteristics.
Machinability
- Steel: Harder and more challenging to machine.
- Aluminum: Softer, easier to cut.
Speed
- Steel: Slower cutting speeds to prevent tool wear.
- Aluminum: Higher speeds increase productivity.
Cost
- Steel: Lower material cost but higher machining cost.
- Aluminum: Higher material cost but lower machining cost.
Applications
- Steel: Structural strength and high-stress components.
- Aluminum: Lightweight and thermal conductivity applications.
Differences Between Steel and Iron
Although related, steel and iron have distinct properties affecting their machining and applications.
Machinability
- Steel: Generally more machinable due to controlled composition.
- Iron: Cast iron can be brittle and challenging to machine.
Strength and Hardness
- Steel: Strength and hardness can be tailored.
- Iron: High hardness but less ductile.
Applications
- Steel: Wide-ranging uses from construction to precision parts.
- Iron: Engine blocks, pipes, and heavy machinery.
Is CNC Steel Machining Expensive?
The cost of CNC steel machining depends on various factors.
Material Selection
- High-Performance Steels: More expensive but necessary for specific applications.
- Standard Steels: More cost-effective for general use.
Design Complexity
- Complex Shapes: Increase programming and machining time.
- Tight Tolerances: Require precision equipment and longer production times.
Production Volume
- Low Volume: Higher per-unit costs due to setup expenses.
- High Volume: Reduced costs through economies of scale.
Machining Time
- Extended Machining: Increases labor and machine costs.
- Optimized Processes: Reduce time and expense.
Tool Wear and Maintenance
- Frequent Tool Changes: Adds to operational costs.
- Regular Maintenance: Essential but increases overhead.
Surface Treatments and Additional Processes
- Extra Steps: Increase total production cost and time.
Technological Advancements
- Modern Equipment: Improves efficiency but requires investment.
What Design Considerations Are Important for CNC Steel Machining?
Designing parts with manufacturing in mind enhances efficiency and reduces costs.
Simplify the Design Where Possible
- Reduce Complexity: Simplifies machining and lowers costs.
- Standard Features: Utilize common sizes and shapes.
Optimize Machinability
- Material Selection: Choose steels that balance performance and machinability.
- Tolerances: Specify realistic tolerances to avoid unnecessary precision.
Consider Material Properties
- Thermal Expansion: Account for potential distortion.
- Hardening: Plan for heat treatment processes.
Tolerance Design
- Critical Dimensions: Tight tolerances where necessary.
- Non-Critical Areas: Allow for standard tolerances to reduce costs.
Facilitate Efficient Tooling
- Standard Tool Sizes: Minimize custom tooling needs.
- Access for Tools: Design parts for easy tool access.
Plan for Finishing Processes
- Surface Treatments: Incorporate allowances for coatings or plating.
- Assembly Requirements: Ensure compatibility with mating parts.
How to Choose the Right Steel CNC Machining Service?
Selecting a reliable CNC machining service provider is crucial for project success.
Experience and Expertise
- Industry Knowledge: Familiarity with your specific sector.
- Technical Skills: Proven track record with steel machining.
Quality Assurance
- Certifications: ISO standards and quality management systems.
- Inspection Processes: Rigorous quality checks and documentation.
Capacity and Capability
- Equipment: Modern machines and technology.
- Production Volume: Ability to handle your order size.
Lead Time
- Efficiency: Meet your project deadlines.
- Flexibility: Adaptability to schedule changes.
Cost-Effectiveness
- Competitive Pricing: Balanced with quality and service.
- Long-Term Partnerships: Potential for better terms.
Technology and Equipment
- Advanced Machinery: Ensures precision and efficiency.
- Continuous Improvement: Commitment to staying current.
Customer Service
- Communication: Responsive and proactive engagement.
- After-Sales Support: Ongoing assistance and problem-solving.
Conclusion
CNC steel machining stands as a cornerstone of modern manufacturing, offering unmatched precision, efficiency, and versatility. By understanding its processes, materials, and applications, you can harness this technology to produce high-quality steel components that meet the most demanding requirements. Whether you're involved in steel CNC machining parts, custom CNC machining, or seeking reliable CNC machining services, embracing CNC steel machining can elevate your projects and drive success in today's competitive market.
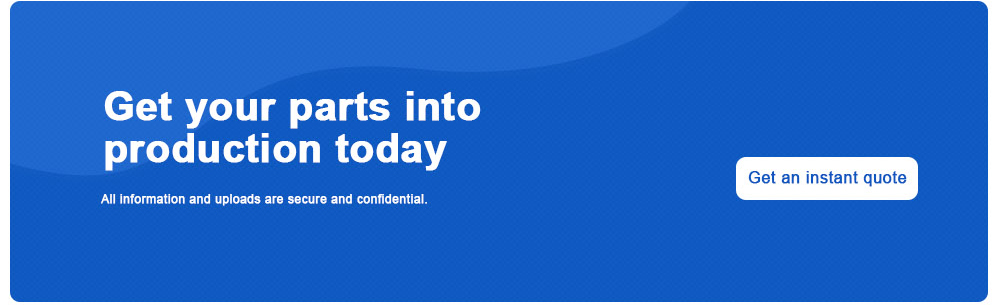
VMT's Steel CNC Machining Services
As a professional CNC machining factory, VMT specializes in high-quality steel CNC machining services. Our advanced equipment and experienced engineering team are equipped to meet your diverse machining needs.
Our Services Include:
- Custom CNC Machining: Tailored steel parts manufactured to your exact specifications with high precision.
- CNC Prototype Machining: Rapid prototyping to accelerate product development cycles.
- Surface Finishing: A variety of finishing options to enhance performance and aesthetics.
- Quality Assurance: Strict quality control processes to ensure every part meets your standards.
Why Choose VMT?
- Professional Experience: Years of expertise in steel machining across multiple industries.
- Advanced Equipment: Utilizing the latest CNC machines and software.
- Customer-Centric Approach: Flexible solutions tailored to your needs.
- Competitive Advantage: High quality, fast delivery, and reasonable pricing.
For more information or to request a quote, please contact our team. We are dedicated to providing exceptional service and solutions for your CNC steel machining projects.
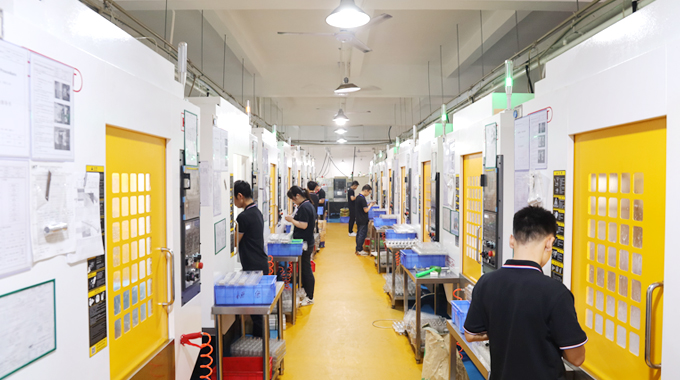
FAQs
1. What Are the Most Common Steels Used in CNC Machining?
Common steels include stainless steels like 304 and 316, carbon steels like 1018 and 1045, and alloy steels like 4130 and 4140. These materials offer a balance of machinability and mechanical properties suitable for various applications.
2. What Is the Best Steel for CNC Machining?
The best steel depends on your project's requirements. Free-machining steels like 1215 are ideal for complex machining, while stainless steels like 17-4 PH are excellent for applications requiring high strength and corrosion resistance.
3. Which Steel Is the Most Difficult to Machine on CNC Machines?
High-hardness tool steels like D2 and high-carbon steels can be challenging due to their hardness and abrasive nature, requiring specialized tooling and parameters.
4. What Is the Difference Between CNC Machining and Machining?
CNC machining uses computer-controlled machines for automated, precise, and repeatable operations, while traditional machining often involves manual control and is less precise.
5. What Is the Basic Principle of CNC Machines?
CNC machines operate based on pre-programmed sequences of machine control commands (G-code), allowing for automated control of cutting tools and machining processes with high precision and efficiency.