Are you struggling to choose the right machining process for your part design? Do confusing terms like "face milling," "contour milling," or "CNC milled parts" leave you second-guessing your project decisions? You're not alone—milling technology is a broad and often misunderstood field. But failing to understand the types of milling operations can lead to increased costs, poor surface finishes, and longer lead times.
Here’s the solution: This comprehensive guide breaks down everything you need to know about milling operations, from how CNC milling machines work, to the differences between each method, to selecting the right process for your custom CNC milling project. With easy-to-follow explanations and practical comparisons, you’ll gain the clarity you need to make confident, informed choices.
Let’s explore the key elements of milling—from machine setup to material removal—so you can achieve higher efficiency, tighter tolerances, and better-quality CNC milled parts.
Milling operations use rotating cutting tools to remove material from a stationary workpiece. There are many types of milling operations—such as face, slot, end, and gear milling—each designed to achieve specific shapes, dimensions, and finishes. CNC milling improves precision and productivity by automating these operations through computer-controlled machines.
Before we dive into the 18 types of milling operations and how each one supports different design and manufacturing goals, let’s begin with the fundamentals—what exactly is a milling operation, and how does CNC milling work from the inside out?
What Is a Milling Operation?
A milling operation is a subtractive manufacturing process that involves the use of rotary cutters to remove material from a workpiece. It’s one of the most widely used machining technologies in industries such as aerospace, automotive, electronics, and medical device manufacturing. The process works by feeding the workpiece against a rotating cutting tool, which systematically removes material to create the desired shape.
Milling is known for its versatility. It can handle everything from simple flat surfaces to complex 3D contours. Operations range from removing large amounts of material quickly (roughing) to precision finishing (finishing). This makes it a staple in both prototyping and mass production.
In modern settings, CNC milling technology is preferred due to its automation, repeatability, and tight tolerance control. Unlike manual milling, CNC milling allows engineers and machinists to program tool paths and parameters digitally, reducing operator intervention and increasing process reliability.
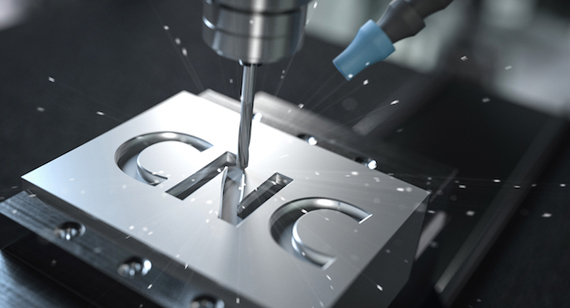
How Does CNC Milling Work?
CNC milling automates the traditional milling process through a combination of software programming, mechanical components, and electrical systems. The process begins with a digital 3D model of the part, which is converted into G-code—commands that tell the CNC milling machine how to move the cutting tools.
Here’s how the key components interact during milling:
- Machine Interface: The control panel where the operator uploads code, sets coordinates, and starts operations.
- Spindle: The motor-driven rotating part that holds and spins the cutting tool.
- Bed or Table: The surface that holds the workpiece in place during cutting.
- Column: The vertical support structure that houses the spindle and motor.
- Saddle: Positioned between the bed and table, allowing movement in multiple directions.
- Arbor: A horizontal shaft used for supporting large diameter cutters.
- Cutting Tools: Specialized tools made of carbide or HSS that vary based on material and desired cut.
Each axis of motion (X, Y, Z) is digitally controlled, enabling the cutter to approach the workpiece with high precision from multiple angles.
18 Milling Operations: Understanding the Most Common Types
Milling operations are not one-size-fits-all. In fact, there are at least 18 types of milling operations, each designed for different geometries, surface finishes, tolerances, and production goals. Whether you're roughing out a block of aluminum or finishing a precise slot in a hardened steel part, understanding the strengths and limitations of each method is critical to achieving optimal results in custom CNC milling.
Let’s break down each milling operation by function, advantages, disadvantages, and typical applications.
Face Milling
Face milling is a common milling operation in which the cutting action primarily occurs at the end corners of the milling cutter. The tool is mounted so that its axis is perpendicular to the surface of the workpiece. This method is ideal for creating flat surfaces and is used for both roughing and finishing operations. In most CNC milling services, face milling is one of the first steps used to square up material before moving to more detailed work.
Face milling cutters usually have multiple cutting edges and are often equipped with replaceable inserts. These tools operate at high speeds and can be programmed for very tight tolerances using CNC milling technology. The feed direction is typically horizontal, while the tool rotates vertically.
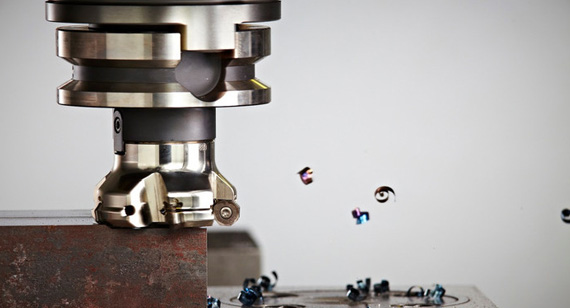
Advantages
- Smooth surface finish: Due to the shearing action of the cutter, face milling provides excellent finishes, especially for large, flat surfaces.
- High efficiency: It removes material quickly and is well-suited for large-volume production.
- Ideal for squaring parts: Perfect for preparing a workpiece before additional milling operations.
- Adaptable to multiple materials: Works well with metals like aluminum, steel, and stainless steel, commonly seen in CNC milled parts.
Disadvantages of Face Milling
- Tool Wear: Face milling tools experience significant wear, especially during high-speed operations or when machining harder materials. The cutting edges can degrade over time, requiring regular tool changes or re-sharpening.
- Limited Depth of Cut: Although face milling is efficient for large flat surfaces, it is not ideal for deep cuts. For deeper cuts, more specialized operations like slot milling may be more appropriate.
- Power Consumption: Face milling requires substantial power from the machine, especially when dealing with large workpieces or tough materials. This can lead to higher energy costs.
- Surface Distortion: In some cases, the cutting forces involved in face milling can cause material distortion or deflection in the workpiece, particularly in thin or flexible materials.
- Surface Finish: While face milling provides a good surface finish, it might not match the quality achieved by other processes like grinding or cylindrical milling for very smooth or fine finishes.
- Complexity for Intricate Shapes: While ideal for flat surfaces, face milling isn't the best choice for creating complex geometric shapes or features with tight tolerance, where other milling operations would be more effective.
These limitations should be considered when deciding if face milling is the best operation for a given project, depending on material type, machining requirements, and available resources.
Applications
Tool and die making: Used to create perfectly flat bases on dies or molds.
- Automotive: Machining cylinder head mating surfaces.
- Aerospace: Finishing structural parts made from aluminum and titanium.
- Custom CNC milling: A go-to process in prototyping and production runs for leveling surfaces before feature machining.
- General fabrication: Used across industries to prep surfaces for assemblies or finishing.
Let me know if you'd like to proceed with slot milling next or another operation!
Slot Milling
Slot milling is a type of milling operation where a rotating cutter is used to remove material along the length of a slot or groove in a workpiece. The cutter engages the material at a specific angle, typically perpendicular to the surface of the workpiece. This operation is commonly used to create slots, grooves, or keyways in parts.
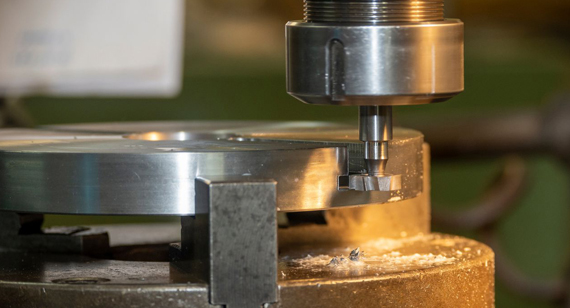
Advantages:
- Versatility: Slot milling can be used for a wide variety of slots and grooves, making it suitable for different industries and applications.
- Precise Dimensions: The use of a CNC milling machine ensures that slot milling can produce accurate dimensions and tight tolerances, particularly when required for fits or keyways.
- Smooth Surface Finish: When properly executed, slot milling can achieve a smooth surface finish, especially when fine cutters and optimal speeds are used.
- Material Removal: Slot milling is an effective method for removing large amounts of material, especially for deep slots or wide keyways, providing an efficient way to shape a workpiece.
- High Flexibility: Slot milling can be done on both simple and complex geometries, offering flexibility in terms of design.
Disadvantages:
- Tool Wear: As with most milling operations, slot milling tools wear out over time, especially when cutting harder materials. This can increase maintenance costs and tool replacement frequency.
- Power Consumption: Slot milling can require higher power input, particularly when cutting deep or wide slots. This can lead to higher energy costs and potential strain on the machine.
- Limited to Shallow Cuts: While slot milling is effective for creating shallow slots, achieving deep slots with high precision can be challenging and may require additional operations.
- Cutting Forces: The cutting forces in slot milling can sometimes lead to deflection or distortion in the workpiece, especially when machining softer materials or thin parts.
- Surface Finish: Achieving the desired surface finish can be difficult, especially when the slot’s dimensions or depth are large. Additional finishing operations might be necessary to improve the surface quality.
Applications:
- Keyways and Key Slots: Commonly used in mechanical assemblies where shafts and gears require keyways for secure mounting.
- Slots for Bearings or Bushings: Creating slots to hold bearings, bushings, or other cylindrical parts.
- Grooves for Seals: Machining grooves to hold seals in fluid applications or mechanical systems.
- Custom Fit Parts: Often used for parts that require specific dimensional fits, such as those in automotive and aerospace applications.
- Component Interlocking: Slot milling is crucial in producing components that need to interlock with others for structural integrity.
Slot milling is an essential operation in various machining processes, particularly for applications that require slots and grooves to be accurately formed in metal, plastics, or composites.
End Milling
End milling is a machining process that involves the use of a rotating cutter, called an end mill, to remove material from a workpiece. The cutter typically moves vertically into the material while rotating in a circular motion. The cutting edges of the tool are located on the sides and end of the cutter, allowing it to cut in both axial and radial directions. End milling is commonly used for producing flat surfaces, grooves, slots, and complex 3D shapes on the workpiece.
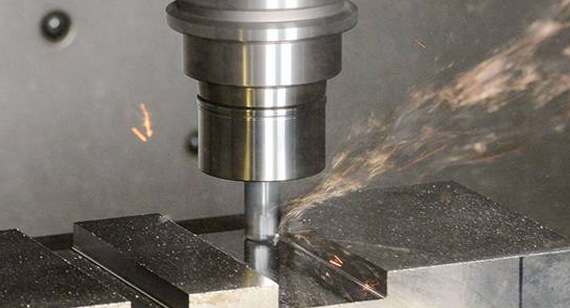
Advantages:
- Versatility: End milling can be used for a wide range of operations, including face milling, slotting, profiling, and contouring. It can handle both roughing and finishing operations.
- High Precision: With the use of CNC technology, end milling can achieve very high precision and tight tolerances, making it ideal for complex or intricate geometries.
- Ability to Cut Deep: Unlike some other milling methods, end milling is capable of cutting deep into the material, which is essential for creating deep pockets or slots.
- Good Surface Finish: When used with proper speeds and feeds, end milling can produce a smooth surface finish on parts, especially when finishing operations are required.
- Effective for 3D Contouring: End mills, especially ball nose end mills, are excellent for cutting 3D shapes and contours, making them popular in mold making and aerospace industries.
Disadvantages:
- Tool Wear: End mills can experience significant wear, particularly during heavy material removal. This can increase costs due to the need for frequent tool changes or sharpening.
- Limited Depth of Cut: The depth of cut in end milling can be limited by the rigidity of the machine, tool, and workpiece. For deeper cuts, specialized tools or multiple passes are often necessary.
- Heat Generation: End milling generates heat during the cutting process, especially when machining harder materials. Without proper cooling or lubrication, excessive heat can lead to tool wear and material deformation.
- Complex Tooling: To achieve optimal performance, various types of end mills may be needed depending on the material and operation, making the selection and maintenance of tooling more complex.
- Chip Removal Issues: In some operations, especially when cutting deep or narrow features, chip removal can become a challenge, potentially causing tool clogging or workpiece damage.
Applications:
- Slotting and Grooving: End milling is frequently used for creating slots, grooves, and keyways, particularly in mechanical assemblies that require specific fits.
- Surface Finishing: End mills are ideal for finishing flat surfaces and achieving smooth finishes on components, especially in precision machining.
- Complex Geometries: It is commonly used to machine complex shapes, contours, and 3D surfaces, especially in industries like aerospace and mold making.
- Pocketing and Drilling: End milling can be used to create pockets and holes, particularly in parts that require intricate internal features.
- Precision Parts Manufacturing: It is widely used in the production of components requiring high dimensional accuracy and tight tolerances, such as in the automotive, electronics, and medical device industries.
End milling is one of the most versatile and widely used machining operations, suitable for a wide range of materials and applications. Its precision and adaptability make it an essential operation in many industries requiring high-quality machining.
Thread Milling
Thread milling is a machining process used to cut threads on the surface of a workpiece using a rotating multi-tooth milling cutter. Unlike tapping, which uses a single-point cutting tool, thread milling utilizes a helical tool motion to create threads. This process is capable of producing internal and external threads and can be applied to a variety of materials, including metals, plastics, and composites. Thread milling is ideal for high-precision threading, particularly for large or deep threads where tapping might be inefficient or challenging.
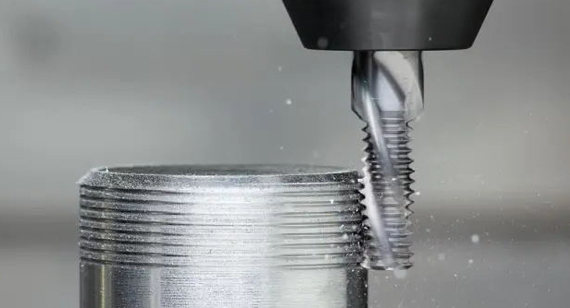
Advantages:
- High Precision: Thread milling produces highly accurate and precise threads with tight tolerances, which is essential for applications that require exact fits, such as in aerospace or automotive components.
- Flexibility: Unlike tapping, which is limited to specific thread sizes and configurations, thread milling can be used to cut various thread sizes, including both internal and external threads, and can easily accommodate multiple thread forms.
- No Need for Blind Holes: Thread milling can be used to create threads in deep holes or blind holes without the risk of tool breakage that may occur with tapping, especially when the hole depth exceeds the thread’s length.
- Better Tool Life: The use of multiple cutting edges in thread milling improves tool life compared to tapping, which uses a single-point cutting edge that wears faster.
- Reduced Chip Build-Up: The continuous cutting motion of thread milling reduces the risk of chip clogging, which is common with tapping. This makes it particularly useful when working with materials that produce long, stringy chips.
Disadvantages:
- Complex Setup: Thread milling requires precise setup, including tool selection, programming, and machine calibration. It may not be as quick or straightforward as tapping, especially for simple thread cutting tasks.
- Higher Cost: Thread milling can be more expensive compared to tapping, due to the specialized tools, machine setup, and increased cycle times. It is best suited for high-precision or high-value applications.
- Tooling Costs: The tools required for thread milling are typically more expensive than taps, especially for larger or more complex threads, which can increase production costs.
- Slower Cycle Time: Thread milling generally takes longer than tapping, as the tool must complete multiple passes to achieve the desired thread depth and form. This can make it less efficient for high-volume production of simple threads.
- Requires Skilled Operators: The process requires skilled operators and advanced CNC programming knowledge to ensure correct toolpath generation, which could increase the overall labor cost.
Applications:
- Aerospace and Automotive: Thread milling is commonly used for high-precision threaded components in the aerospace and automotive industries, where accuracy and strength are critical for performance.
- Medical Devices: For manufacturing medical devices and implants that require fine-threaded features, thread milling ensures high-quality, precise threads that meet stringent standards.
- Tooling and Fixtures: Thread milling is used to create high-quality threads for tooling and fixtures, ensuring that parts assemble correctly and maintain their integrity during use.
- Oil and Gas: For threaded components used in high-stress environments, such as oil drilling equipment, thread milling ensures that threads can withstand extreme pressures and harsh conditions.
- Precision Machinery: Thread milling is often used in precision machining operations, where the creation of small or deep threaded holes is required for complex or high-precision parts.
Thread milling offers a versatile, high-precision method for producing threads, particularly for deep or intricate applications where tapping may not be effective. However, its complexity and higher cost make it more suitable for specialized or high-value work rather than large-scale, simple thread production.
Shoulder Milling
Shoulder milling is a machining process used to cut grooves and shoulders into a workpiece using a rotating cutter. The cutting tool in shoulder milling is typically mounted at a perpendicular angle to the surface of the material, allowing for the creation of flat, vertical walls or steps on the workpiece. It is often used to create shoulders with defined edges, which are crucial for part alignment in assembly processes. Shoulder milling is commonly done with either a face mill or end mill, depending on the geometry of the workpiece and the required surface finish.
Advantages:
- Versatile Cutting: Shoulder milling is highly versatile, capable of producing a wide variety of features, including flat surfaces, grooves, and shoulders. It can also cut multiple widths and depths in a single pass.
- High Material Removal Rate: This method offers efficient material removal, making it ideal for applications where significant stock must be removed quickly. It provides faster cutting speeds compared to other operations like slot milling.
- Precision: With the right tools and settings, shoulder milling provides precise, accurate cuts. This is especially important for applications that require tight tolerances, such as in aerospace or automotive industries.
- Reduced Tool Wear: Shoulder milling tools often exhibit less wear than other types of milling tools because they have multiple cutting edges working in tandem, which helps to distribute the load evenly during machining.
- Improved Surface Finish: Shoulder milling can provide a smooth and even surface finish, especially when using carbide inserts and high-speed machining techniques. This makes it suitable for parts where the surface finish is critical.
Disadvantages:
- Complex Setup: Setting up the correct alignment and positioning for shoulder milling can be more complicated compared to other milling operations. A precise workpiece clamping and toolpath programming are required for optimal results.
- Potential for Tool Deflection: If the tool is not rigidly held or if cutting conditions are not optimized, shoulder milling can lead to tool deflection, resulting in inaccurate cuts or poor surface finishes.
- Limited to Shallow Depths: While shoulder milling can create flat or stepped shoulders, its depth of cut may be limited compared to other milling methods. For deeper cuts, additional passes or other machining processes may be needed.
- Increased Tool Wear: Although shoulder milling is efficient, the cutter can experience significant wear due to the cutting force involved in creating vertical walls. This requires tool changes at regular intervals, especially during high-volume production runs.
- Machine Constraints: Some milling machines may have limited reach or vertical capacity, which can restrict the size of the shoulders that can be milled. Special fixtures or tooling may be required for larger parts.
Applications:
- Automotive Manufacturing: Shoulder milling is frequently used to create keyways and slots in engine components, chassis, and other automotive parts that require precise shoulders or grooves for assembly.
- Aerospace Components: In aerospace applications, shoulder milling is used to create structural parts that must meet exact tolerances, including supports and attachments for various components.
- Tooling and Fixtures: This process is commonly employed in manufacturing custom tools and fixtures, where the precise fit of parts with stepped or grooved shoulders is crucial for the proper alignment of assemblies.
- Medical Equipment: Shoulder milling plays a role in manufacturing medical devices such as surgical tools and implants, where high precision and a smooth finish are critical for both functionality and safety.
- Consumer Electronics: Small precision parts used in electronics often require shoulder milling to achieve the necessary alignment and fit, including connectors and housing components for devices.
Shoulder milling is a versatile and precise machining process that is ideal for creating specific geometric features such as shoulders, grooves, and stepped sections. It offers high material removal rates and superior surface finishes but requires careful setup and tooling to minimize deflection and achieve accurate results. Its applications are widespread across industries like automotive, aerospace, medical, and tooling.
Side Milling
Side milling is a machining operation that involves cutting a workpiece with the side of a rotating cutter, typically an end mill or a face mill. The cutting tool is positioned perpendicular to the workpiece surface, with the cutter's side surface doing the cutting, rather than the end. This allows side milling to create features such as grooves, slots, and flat surfaces with the sides of the workpiece. The operation can be performed using either horizontal or vertical milling machines, depending on the machine and the part's geometry. Side milling is commonly used to cut deep, narrow slots or wide surfaces requiring precision.
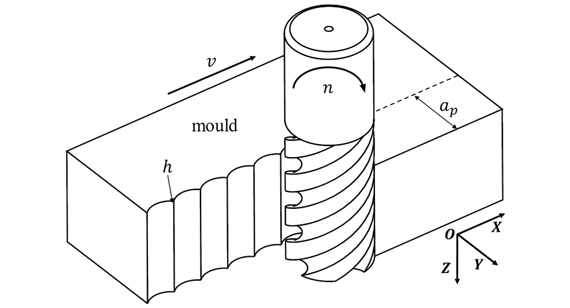
Advantages:
- Versatile Tool Use: Side milling is highly versatile because it allows for the use of various cutting tools, including end mills, face mills, and special tools, to produce different types of cuts.
- High Material Removal Rates: Due to the cutting action of the side of the tool, side milling enables faster material removal compared to other milling operations, particularly for larger parts that require significant stock removal.
- Smooth Surface Finish: Side milling can produce smooth, flat surfaces when the correct feed rate and cutting tool are used. This is essential for parts that require tight tolerances and smooth finishes, such as components in the aerospace and automotive industries.
- Precision Cutting: When performed correctly, side milling offers high precision, making it ideal for creating parts with exact dimensions and tight fits. It is commonly used for cutting grooves, slots, and steps with high accuracy.
- Ability to Machine Complex Features: Side milling is effective for cutting complex features on a workpiece, including internal slots, keyways, and grooves that might be difficult to achieve with other milling methods.
Disadvantages:
- Tool Deflection: The cutting forces involved in side milling can lead to tool deflection, especially when cutting deep or long slots. This can affect the accuracy of the cuts and reduce the quality of the surface finish.
- Limited Depth of Cut: While side milling is effective for creating narrow slots and grooves, its depth of cut is limited compared to other operations like face milling. Multiple passes may be required for deeper cuts, which increases cycle time.
- Complex Setup: Setting up a side milling operation can be more complex compared to other types of milling. Ensuring that the workpiece is aligned correctly with the tool and that the proper tool is used requires precision.
- Increased Tool Wear: Side milling can cause more wear on the tool compared to other milling operations due to the side cutting action and the forces involved. This necessitates regular tool changes, particularly during high-volume production runs.
- Requires High Precision Machines: To achieve the desired quality and finish in side milling, machines with high rigidity and precision are required. Machines with lower precision may result in less accurate cuts and poor surface quality.
Applications:
- Aerospace Manufacturing: Side milling is used to create precise slots, grooves, and flat surfaces in aerospace components, such as engine parts, structural elements, and frames, where accuracy and a smooth finish are critical.
- Automotive Industry: In the automotive sector, side milling is employed to create parts like transmission components, engine blocks, and chassis parts that require tight tolerances and high precision.
- Medical Device Production: Side milling plays a vital role in the production of medical components like surgical instruments, implants, and housings that require smooth surfaces and precise features for proper functionality and safety.
- Tooling and Fixtures: The operation is frequently used for producing custom tooling and fixtures, where precise geometric features, such as grooves or stepped sections, need to be formed to accommodate specific parts during assembly.
- Electronics Manufacturing: Side milling is applied in the electronics industry to produce components with narrow slots and grooves, such as connectors, housings, and brackets used in electronic devices.
Side milling is a versatile and effective machining operation that allows for precise cuts and the creation of complex features. It offers a range of benefits, such as high material removal rates, smooth surface finishes, and the ability to machine difficult-to-reach areas. However, it does come with challenges such as tool wear and setup complexity, which need to be managed for optimal results.
Contour Milling
Contour milling is a machining operation used to cut complex curves or irregular shapes along the surface of a workpiece. The process involves using a rotating cutting tool to follow the contours of the workpiece, producing smooth, precise profiles. Contour milling can be done using CNC milling machines, which provide the high precision required for such operations. The cutter follows the specific path dictated by the part design, often used for creating detailed external and internal shapes such as contours, curves, or complex profiles that are not easily achievable with other milling methods. This process is highly beneficial for creating custom-designed parts in industries that require detailed shapes and smooth finishes.
Advantages:
- Precision and Detail: Contour milling offers high precision and the ability to create highly detailed, complex shapes on a workpiece. This makes it ideal for industries such as aerospace and automotive, where exact specifications and tight tolerances are crucial.
- Smooth Surface Finish: The ability to use various types of cutting tools allows for excellent surface finishes, making contour milling ideal for parts that require smooth, fine surfaces. The CNC-controlled nature of the operation ensures that the contours are cut with a high degree of smoothness.
- Flexibility in Design: Contour milling is highly versatile and can handle parts with different geometric complexities. Whether the part involves simple curves or more intricate designs, contour milling can adapt to the specific needs of the project.
- Reduced Material Waste: By following the contours of the workpiece, contour milling minimizes material waste compared to other machining processes. It allows the operator to efficiently utilize material while maintaining precision in the part's shape.
- Enhanced Accuracy: With CNC machines, contour milling can consistently produce the same shapes with high accuracy, ensuring that parts meet precise engineering specifications over multiple production runs.
Disadvantages:
- Tool Wear: As with many milling processes, tool wear can be a significant disadvantage of contour milling. The rotating cutter may experience increased wear when cutting complex geometries or when used for extended periods, leading to reduced cutting efficiency and the need for frequent tool replacements.
- Longer Cycle Times: Since contour milling often involves cutting complex, curved paths, the cycle time for machining can be longer than traditional milling operations, especially if the part has intricate designs. This can increase the overall production time and costs.
- Complex Setup: The complexity of contour milling operations means that the setup time is generally longer. The machine must be accurately programmed to follow the exact contours of the workpiece, and this setup process can be time-consuming.
- Requires Skilled Operators: Because contour milling involves intricate machining paths, it requires highly skilled operators familiar with CNC programming and the specific parameters for contour cutting. An inexperienced operator may cause mistakes that impact part quality.
- Limited Material Types: While contour milling can be applied to many materials, the process is more commonly used for softer metals and plastics. Harder materials may require specialized tooling and adjustments, and excessive heat generated during milling can affect the workpiece's properties.
Applications:
- Aerospace: Contour milling is used to create complex parts for aircraft, such as wing components, turbine blades, and structural elements that require high precision and smooth surface finishes.
- Automotive: Automotive components like engine parts, suspension arms, and custom-designed car body panels often require contour milling for intricate designs and complex curves.
- Medical Devices: Parts for medical devices, such as surgical instruments, implants, and prosthetics, frequently use contour milling to meet strict precision and surface finish requirements.
- Tooling and Fixtures: Contour milling is often used to create custom tooling and fixtures for the assembly of complex parts in manufacturing environments. These tools must fit precisely into assembly lines or hold parts securely during other manufacturing processes.
- Consumer Electronics: In the production of consumer electronics like smartphones and laptops, contour milling is used for parts such as housings, connectors, and internal components that require complex shapes and a high degree of surface quality.
Contour milling is a highly effective and versatile machining operation that provides exceptional precision and flexibility for creating complex shapes and profiles. While it offers benefits like reduced material waste, smooth finishes, and high accuracy, it also comes with challenges, such as longer cycle times, tool wear, and the need for skilled operators. Despite these challenges, contour milling remains an essential process in industries requiring custom, high-precision parts.
Sawing
Sawing is a machining process used to cut through materials using a toothed blade or saw. This operation involves the use of a saw blade that moves in a continuous or oscillating motion to remove material from a workpiece. Sawing is typically employed for cutting large parts into manageable sizes or creating specific shapes. It is one of the most common and versatile cutting methods, suitable for a wide variety of materials, including metals, plastics, wood, and composites. While sawing is often seen as a preliminary process in the manufacturing of parts, it plays an essential role in shaping and sizing materials before they undergo further machining processes such as milling or turning.
Advantages:
- Cost-Effective: Sawing is one of the most economical cutting methods, especially for large volumes or bulk material cutting. It requires minimal investment in tools and equipment and is suitable for cutting various materials without significant costs.
- Simple and Fast: The operation is relatively simple to set up and execute, making it fast and efficient. It’s a straightforward process that can quickly produce parts of the required size, helping save on processing time.
- Versatility: Sawing can be used on a wide range of materials, including metals, plastics, and composites, which makes it a versatile process for various industries. Different types of saw blades can be used to achieve different cutting characteristics.
- Minimal Material Waste: Unlike other cutting methods, sawing produces relatively minimal material waste. It cuts in a straight line, which reduces the chance of excess material loss compared to processes like grinding or milling.
- Adaptability: Sawing can be performed on various scales, from manual saws for smaller jobs to large, industrial-grade saws used for high-volume production. It is also adaptable to both horizontal and vertical cutting orientations.
Disadvantages:
- Limited Precision: While sawing is good for rough cutting and sizing materials, it generally doesn’t provide the level of precision required for intricate, fine details. Parts may require additional machining to meet tighter tolerances.
- Surface Finish: The surface finish from sawing is typically rough, which can require further finishing processes like grinding or polishing to improve the appearance and smoothness of the cut.
- Tool Wear: Saw blades, especially when cutting harder materials, experience wear over time. This leads to the need for regular maintenance or replacement of the blades to maintain cutting performance.
- Heat Generation: Sawing generates heat as the blade contacts the material, which can affect the material properties or create dimensional inaccuracies. It can also accelerate the wear of the blade.
- Limited Complexity: Sawing is primarily used for simple straight-line cuts. It is not suitable for creating complex shapes or intricate details that require other specialized machining processes like milling or turning.
Applications:
- Metal Cutting: Sawing is widely used in metalworking for cutting large metal sheets, rods, pipes, and structural materials into smaller, manageable sizes. It is an essential operation in industries such as construction, manufacturing, and shipbuilding.
- Woodworking: In the woodworking industry, saws are used extensively to cut timber, plywood, and other wood-based materials into precise sizes and shapes. Sawing is fundamental in furniture making, construction, and cabinetry.
- Plastic Cutting: Sawing is commonly used in industries where plastic parts need to be cut into specific dimensions. It is used in manufacturing components for automotive parts, electronic housings, and other consumer products.
- Aerospace: In aerospace manufacturing, sawing is used to cut large metal sheets and titanium alloys into parts that are then processed further through other machining methods such as milling and turning.
- Construction and Structural Work: Sawing is integral in the construction industry, where large beams, pipes, and other materials need to be cut into smaller sections for assembly and installation.
Sawing remains a vital and cost-effective machining process widely used for cutting materials into basic shapes or sizes. While it may not offer the same precision or surface finish as other machining operations, it provides a practical, fast, and economical solution for rough cutting and sizing materials across various industries.
CAM Milling
CAM (Computer-Aided Manufacturing) milling refers to the process of using computer software to control a milling machine's movements to precisely machine a part or product. It utilizes a CAD (Computer-Aided Design) model to generate toolpaths that are then translated into instructions for the CNC (Computer Numerical Control) milling machine. The software optimizes the machining process, enabling more accurate, efficient, and automated production of complex parts. CAM milling is typically used in industries requiring high-precision, automated part fabrication, and it is especially beneficial in producing intricate designs with tight tolerances.
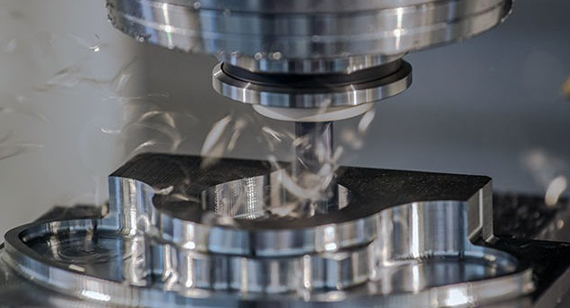
Advantages:
- Precision and Accuracy: CAM milling enables highly accurate and precise machining, ensuring that parts are fabricated to exact specifications and tolerances. It eliminates human error, leading to consistently high-quality results.
- Increased Efficiency: By automating the milling process, CAM milling reduces the time required to produce parts, as it eliminates the need for manual setup and adjustments. The software allows for faster and more efficient operations, optimizing machining time.
- Complex Geometries: CAM milling can handle complex geometries and intricate designs that would be difficult or time-consuming to achieve manually. The software’s ability to create detailed toolpaths allows for the production of sophisticated components with ease.
- Repeatability: With CAM milling, the process can be repeated consistently, making it ideal for high-volume production runs. Once the program is set up, parts can be produced with the same accuracy and specifications across multiple cycles.
- Flexibility: CAM milling software can be easily adapted to different machine tools and manufacturing processes. It can be used for a wide range of materials, from metals and plastics to composites, offering versatility in manufacturing.
Disadvantages:
- Initial Setup Cost: The setup cost for CAM milling can be high, as it requires investment in specialized software and the training of operators. While the cost is offset by the efficiency and precision gains, the upfront investment can be a barrier for smaller companies.
- Dependence on Software: Since CAM milling relies heavily on software, any errors in the design file or software malfunction can lead to defects in the final product. Ensuring the software and CAD models are accurate is crucial.
- Complexity: Operating CAM milling machines requires specialized knowledge and training, which may increase labor costs and training time for operators. While the software simplifies many aspects of the process, understanding the nuances of CAM systems is essential.
- Material Limitations: While CAM milling is highly versatile, it may not be suitable for all types of materials. Some materials may require specific modifications to the milling process, or might not be as easily machined as others.
- Machine Compatibility: Not all milling machines are compatible with CAM systems. Older or less sophisticated machines may not be able to take full advantage of CAM milling technology, limiting its effectiveness in certain shops.
Applications:
- Aerospace Industry: CAM milling is widely used in aerospace to manufacture highly intricate and complex parts, such as turbine blades, brackets, and structural components. The need for precision and performance makes CAM milling an essential process in this field.
- Automotive Industry: In automotive manufacturing, CAM milling is used to produce parts with tight tolerances, including engine components, transmission parts, and custom tooling. It also aids in prototyping and testing components for performance.
- Medical Device Manufacturing: The medical industry relies on CAM milling to create precise components for devices such as implants, surgical instruments, and diagnostic equipment. The ability to produce small, detailed parts with high accuracy is crucial in medical device manufacturing.
- Tool and Die Making: CAM milling is commonly used to create tools, dies, and molds in the tooling industry. It helps produce the necessary components for manufacturing injection molds, stamping dies, and other critical tooling for production lines.
- Electronics Manufacturing: CAM milling is used to create intricate parts for electronic devices, including housings, connectors, and circuit boards. The need for precision in the electronics industry makes CAM milling a go-to method for producing electronic components.
- Custom Parts and Prototypes: CAM milling is highly effective in the production of custom parts and prototypes, particularly in industries where unique and complex components are required. The software’s ability to design and modify parts quickly makes it ideal for rapid prototyping and small batch production.
In summary, CAM milling is an advanced manufacturing process that significantly improves efficiency, precision, and flexibility in the production of complex parts. Although it requires an investment in technology and skilled operators, its advantages, particularly in industries demanding high precision, make it an indispensable tool in modern manufacturing.
Gear Milling
Gear milling is a machining process used to create gears with specific profiles, such as spur gears, helical gears, bevel gears, and worm gears. It involves using a rotating cutter, typically a specialized gear cutter, to gradually remove material from a workpiece, shaping it into the desired gear form. The process can be performed using various milling machines, but is most commonly done using a CNC (Computer Numerical Control) machine equipped with the necessary tools and gear milling software. Gear milling is a versatile method for manufacturing both small and large quantities of gears, and it is essential in the production of components that require precise teeth and profiles.
Advantages:
- High Precision: Gear milling allows for the production of gears with high dimensional accuracy, ensuring that the teeth are cut precisely to meet stringent tolerances. This is critical for applications requiring reliable gear performance.
- Versatility: Gear milling is suitable for a wide variety of gears, including those with complex profiles such as helical and bevel gears. It is flexible in terms of both the size and type of gears it can produce.
- Speed: Compared to other gear manufacturing methods, such as gear hobbing or shaping, gear milling can be faster, particularly for smaller quantities or custom gear production. CNC gear milling allows for efficient production with minimal setup time.
- Customizability: Gear milling allows for the creation of custom gears with specific specifications. This makes it ideal for industries where standard gears do not meet the requirements, such as in the aerospace or automotive industries.
- Improved Surface Finish: Milling operations can achieve a smooth surface finish, reducing the need for further finishing processes. This is especially beneficial in applications where the gears are exposed to high-speed operations or require minimal friction.
Disadvantages:
- Limited for Large Quantities: While gear milling is efficient for small to medium batches, it can be less cost-effective than other methods like gear hobbing when producing large volumes of gears due to higher tooling costs and slower material removal rates.
- Tool Wear: Gear milling tools, particularly cutters, can experience significant wear over time due to the stresses involved in cutting the teeth. Regular maintenance and tool replacement can add to operational costs.
- Complex Setup: Setting up a CNC milling machine for gear milling can be time-consuming, requiring precise calibration and setup of the machine, tool paths, and cutting parameters to ensure accuracy.
- Limited for Very Large Gears: While gear milling is effective for a wide range of gear sizes, it is less efficient for very large gears. Other methods such as gear hobbing may be better suited for large-volume or larger gears.
- Material Limitations: Gear milling is more suited for certain materials, such as steel, aluminum, and stainless steel. Materials that are particularly hard or abrasive may require specialized tools and additional care during the milling process.
Applications:
- Automotive Industry: Gear milling is extensively used to produce automotive gears, including those used in transmissions, differential gears, and other powertrain components. The precision required in automotive applications makes gear milling an ideal choice.
- Aerospace Industry: The aerospace industry relies on gear milling to manufacture gears for aircraft engines, landing gears, and control systems. These gears must meet strict performance and safety standards, making the accuracy and reliability of the milling process critical.
- Industrial Machinery: Gear milling is commonly used to create gears for various industrial machines, including conveyors, pumps, and compressors. These gears must endure heavy loads and constant operation, making durability and precision key factors.
- Power Generation: Gears used in turbines and generators in the power generation industry are often produced using gear milling. The precision in tooth profile and strength of these gears is essential to the efficient operation of power plants.
- Robotics: In the robotics industry, gear milling is used to create custom gears for robotic arms, actuators, and other moving parts. The high level of precision and customization allows for the creation of gears that are perfectly suited for specific robotic functions.
- Marine Industry: Gear milling is also used in the manufacturing of gears for marine applications, such as in ship propulsion systems and underwater machinery. These gears must be durable, resistant to corrosion, and able to handle high stress from marine environments.
- Military and Defense: The defense industry uses gear milling for manufacturing critical components in military vehicles, weapons systems, and communication equipment. These gears must perform reliably under harsh conditions and adhere to tight specifications.
In summary, gear milling is a highly versatile and precise machining process that plays a vital role in the production of gears across various industries. While it may have some limitations, particularly in high-volume production, its ability to produce custom, high-quality gears makes it a valuable process for specialized applications requiring precision and reliability.
Angular or Oblique Milling
Angular or oblique milling refers to the process of milling a workpiece at an angle other than 90 degrees to the surface. In this operation, the cutting tool is positioned at an angle to the surface of the material, and the cut is made at an oblique angle. The angle could range from a small acute angle to larger, more pronounced angles depending on the specific application. This type of milling is typically used when a specific angle, such as a chamfer or a taper, is required on the workpiece.
Angular milling is commonly performed using a milling machine that has the ability to adjust the tool and workpiece setup to the desired angle. The cutter used in this operation can be an end mill or a specific tool designed for angled cutting. Angular milling is often used in combination with other milling processes to achieve the desired geometry on the workpiece.
Advantages:
- Ability to Cut Angles: One of the main advantages of angular milling is its ability to efficiently produce precise angles on the workpiece. This is useful in creating specific shapes or tapered surfaces that cannot be achieved with standard 90-degree milling.
- Enhanced Surface Finish: Since the tool is angled, the cutting action tends to be more gradual, reducing the chances of tool marks and improving the surface finish. This is particularly beneficial when working with materials that require smooth finishes for functional or aesthetic reasons.
- Versatility: Angular milling allows for the creation of a wide range of geometries, from simple chamfers to complex angled surfaces, making it a versatile operation in various industries. It can be used for producing parts with more complicated profiles.
- Increased Tool Life: The oblique cutting action generally reduces tool wear compared to traditional milling operations. Since the cutting load is distributed more evenly over the tool, it can contribute to extended tool life, especially for softer materials.
Disadvantages:
- Complex Setup: Angular milling often requires more time and effort to properly set up the tool and the workpiece at the correct angle. The machine's settings must be accurately adjusted to ensure that the desired angle is achieved.
- Limited to Specific Applications: While angular milling is highly effective for certain types of workpieces, it is not suitable for all machining tasks. It is primarily used for applications where angled surfaces or features are required, which limits its versatility in some cases.
- Tool Wear: While angular milling can reduce tool wear compared to traditional milling, it can still lead to premature tool failure if not properly managed. Cutting at an angle can increase stress on the tool, particularly if the material is hard or abrasive.
- Precision Concerns: Achieving high precision with angular milling can be challenging, especially when dealing with very acute or shallow angles. It requires careful control of the machine, cutting tool, and workpiece positioning to ensure accuracy.
Applications:
- Chamfering and Tapering: Angular milling is commonly used in applications where the workpiece requires a chamfered edge or a tapered feature. These applications are often found in industries like automotive and aerospace, where precise geometries are crucial.
- Tool Making: Angular milling is frequently used in tool-making processes, especially when shaping the edges of cutting tools. The ability to create precise angles is essential in producing tools like drills, reamers, and end mills.
- Automotive Industry: In the automotive industry, angular milling is used for producing parts like gears, shafts, and housings that require specific angles for fitting and assembly. It is also used for machining keyways, splines, and other features that require angled cuts.
- Aerospace Components: The aerospace industry often requires parts that include complex geometries and angled surfaces. Angular milling is used to achieve these features in components such as turbine blades, airframes, and engine parts.
- Military and Defense: Angular milling is used in the military and defense industries to create parts for weaponry, vehicles, and other defense equipment that must meet strict design and performance standards, including angled cuts and tapered surfaces.
- Furniture and Architectural Designs: In furniture making and architectural applications, angular milling is used to create decorative edges, intricate shapes, and structural components that require specific angles for aesthetic or functional purposes.
- Medical Devices: Angular milling is used to create precise cuts in the manufacture of medical devices, particularly those requiring specialized angled surfaces for assembly or function. This includes components for surgical instruments and diagnostic tools.
In conclusion, angular or oblique milling is a versatile machining process that enables the creation of parts with angled features and specific geometries. While it offers several advantages in terms of surface finish and tool life, it does have limitations such as the need for accurate setup and specialized tools. Its applications span various industries, including automotive, aerospace, military, and medical device manufacturing, making it an essential process in many engineering fields.
Profile Milling
Profile milling is a type of milling operation where the contour of a workpiece is shaped to a specific profile or contour. This process is often used to create features such as grooves, edges, or even more complex shapes that require a specific outline. The milling cutter follows the path of the contour, typically guided by the geometry of the workpiece. It is particularly useful for applications that demand the precision of detailed profiles.
Advantages:
- Precision: Profile milling allows for the precise creation of complex shapes and detailed contours. This is essential for applications that require high tolerance and accurate geometric features.
- Versatility: The process is capable of producing a wide variety of shapes, from simple straight-line profiles to intricate curves and geometries. It is versatile enough to handle both shallow and deep profiles.
- Tool Selection: Various tools can be used in profile milling, such as flat end mills or ball end mills, depending on the complexity of the profile, which allows for a wide range of applications.
- Surface Finish: Profile milling can result in a smooth and clean surface finish, which is critical in industries that require parts to have a refined appearance or function, such as the automotive and aerospace sectors.
Disadvantages:
- Complex Setup: Setting up the machine to perform profile milling can be complex, particularly when dealing with intricate profiles. The precision required means that the setup and machine adjustments must be accurate.
- Longer Cycle Times: Profile milling can often take longer than other simpler milling operations due to the level of detail involved. This can increase production time and reduce overall efficiency for large batch jobs.
- Tool Wear: Depending on the material being milled and the complexity of the profile, the cutting tool can experience higher wear and tear. This may require more frequent tool changes and increases the cost of operation.
Applications:
- Automotive Components: Profile milling is used to create complex shapes on car parts, such as body panels, engine components, and structural elements.
- Aerospace Industry: The aerospace sector uses profile milling to create intricate parts like turbine blades, wing components, and other precision aerospace parts.
- Medical Devices: In the medical industry, profile milling is applied to create components for surgical instruments and implants that require specific profiles.
- Tool Making: Profile milling is also used in the manufacturing of tools with complex profiles that need to be precise for functional applications.
Cross-Cut Milling
Cross-cut milling involves a cutting tool that moves across the surface of the material at a perpendicular angle to the length of the workpiece. This type of milling is commonly used to cut grooves or slots across a surface, often to prepare materials for further processing or to separate sections of a material. Cross-cut milling is typically performed using a horizontal milling machine or a vertical machine with a suitable cutter.
Advantages:
- Simplicity: Cross-cut milling is a relatively simple process that is easy to set up and execute. It requires fewer adjustments compared to more complex milling operations.
- Material Removal: It is highly effective for quickly removing material from a workpiece. Cross-cut milling can efficiently create grooves and slots for various applications.
- Versatility: It can be used for a variety of materials, including metals and plastics, which makes it a versatile choice for many manufacturing processes.
Disadvantages:
- Limited to Simple Cuts: Cross-cut milling is not ideal for highly intricate or detailed work. It is more suitable for creating basic grooves or slots.
- Surface Finish: The surface finish might not be as smooth as other more refined milling techniques, especially when high precision is required.
- Tool Wear: Over time, the tool used in cross-cut milling may experience wear, especially if it’s used for cutting harder materials, leading to potential tool maintenance costs.
Applications:
- Slot Cutting: Often used to create slots or grooves for assembly purposes, such as for interlocking parts or for wire channels in electrical enclosures.
- Part Separation: In manufacturing, cross-cut milling can be used to separate sections of a larger workpiece, particularly in sheet metal fabrication.
- Woodworking: Used in woodworking to cut grooves in furniture pieces or decorative items.
Group Milling
Group milling refers to a process where multiple milling tools work simultaneously to cut different parts of a workpiece. The cutting tools are arranged together on the machine to operate at the same time, allowing for faster material removal and the simultaneous processing of multiple features on a part. This process is typically performed on a machine capable of holding multiple tools, such as a multi-spindle milling machine.
Advantages:
- Increased Productivity: Group milling allows for the simultaneous machining of several features, significantly reducing the total time required for machining a part.
- Cost-Effective: By reducing the number of machining steps, group milling can be more cost-effective, especially for high-volume production.
- Improved Efficiency: Multiple tools working at once mean that the machining process is more efficient, with less downtime between tool changes or setup adjustments.
Disadvantages:
- Complex Setup: Setting up a group milling operation can be more complex compared to single-tool milling, as the tools need to be precisely aligned and coordinated.
- Limited Flexibility: The configuration of the tools in a group milling setup is fixed, which may limit its use for parts with highly variable features.
- Increased Tool Wear: Using multiple tools simultaneously can lead to faster wear on the cutting tools, especially if the material being machined is particularly hard or abrasive.
Applications:
- Mass Production: Group milling is ideal for industries that require high-volume production of parts with similar or identical features. It is commonly used in automotive and aerospace industries.
- Complex Parts Manufacturing: When multiple features need to be machined into a part simultaneously, group milling can be used to manufacture complex components with multiple features in a single cycle.
- Prototyping: Group milling is also used in rapid prototyping, where quick and efficient machining of test parts is necessary.
These milling operations offer various solutions depending on the required precision, speed, and complexity of the workpiece. Choosing the right type of milling operation involves understanding the material, the desired result, and the production requirements.
Plain or Flatbed Milling
Plain or flatbed milling is a basic milling operation in which a cutting tool moves linearly along a horizontal surface to remove material from the workpiece. The workpiece is typically mounted onto a flatbed or horizontal machine table, and the tool cuts along the flat surface in a single pass or multiple passes. This operation is often used for general-purpose machining and is suitable for tasks such as face milling and surface finishing.
Advantages:
- Simple Setup: The setup for plain milling is relatively simple, as it only requires the workpiece to be secured on a flatbed with basic alignment.
- Efficient Material Removal: Plain milling allows for efficient removal of material from large, flat surfaces, making it ideal for bulk material removal.
- Versatility: It can be applied to a wide range of materials, including metals and plastics, making it a versatile choice for different industries.
Disadvantages:
- Limited to Flat Surfaces: This type of milling operation is only suitable for flat surfaces, which limits its application for parts requiring complex geometries.
- Tool Wear: Over time, the cutting tools may wear down due to continuous use, which may increase maintenance and tool replacement costs.
- Lower Precision: For parts requiring high-precision finishes, plain milling may not provide the level of accuracy that more advanced milling operations can offer.
Applications:
- Manufacturing of Large Plates: Commonly used for the production of large flat components such as plates, sheet metal, and structural pieces.
- Surface Finishing: Used to achieve a smooth surface finish on flat components, particularly in industries such as automotive and general manufacturing.
- Bulk Material Removal: Plain milling is ideal for removing significant amounts of material quickly when high precision is not critical.
T-Slot Milling
T-slot milling is a type of milling operation used to create T-shaped slots in a workpiece. This is achieved by using a T-slot cutter, which has a unique shape that allows it to mill the characteristic “T” shape required for specific applications. This type of milling is often used to create slots for fixtures, fasteners, or rail systems in machinery and workholding devices.
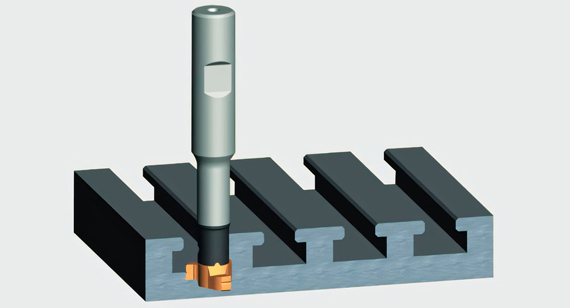
Advantages:
- Precise Slot Formation: T-slot milling allows for the creation of precise and accurately formed T-slots, which are crucial for secure fastening and assembly in various industrial applications.
- Enhanced Machining Flexibility: It can be applied to a range of materials and can handle a variety of slot sizes and configurations.
- Durability: T-slot cutters are designed for durability and can handle tough materials, which ensures long-term efficiency in production environments.
Disadvantages:
- Tooling Cost: T-slot cutters can be more expensive than standard milling tools, which may increase the initial setup cost.
- Specialized Equipment: Not all milling machines are capable of performing T-slot milling, requiring specific machinery and tools.
- Time Consumption: Due to the complexity of creating a T-shape, the process may take longer than simpler milling operations, affecting production speed.
Applications:
- Machine Fixtures and Workholding: T-slots are commonly used in worktables and machine fixtures to hold and secure parts during machining.
- Rail Systems: T-slot milling is used in the creation of rails for adjustable systems, such as conveyor systems or assembly lines.
- Structural Components: T-slots are integral to the manufacturing of structural components where multiple parts need to be fastened securely.
Cam Milling
Cam milling involves the use of a rotating cam to drive the movement of the milling tool along the surface of the workpiece. This operation is typically used for creating cam profiles, such as those used in engine timing systems. Cam milling can create complex curves or cams that follow a specific path dictated by the cam design, making it ideal for applications where precise, repetitive motion is needed.
Advantages:
- Precision: Cam milling offers high precision and is capable of producing very accurate profiles, especially for components like cams and gears.
- Consistency: It produces consistent and repeatable results, which is crucial for high-volume production runs of parts that must adhere to strict specifications.
- Complex Shapes: Cam milling is ideal for creating complex shapes and profiles that would be difficult to produce with standard milling methods.
Disadvantages:
- Complex Setup: The setup for cam milling is more complex than that of basic milling operations, requiring precise alignment and calibration of the cam and cutting tools.
- Higher Cost: Due to the specialized tools and equipment required, cam milling can be more expensive than other types of milling operations.
- Time Consuming: For parts with intricate or complex cam profiles, the machining process can take longer, impacting production speed.
Applications:
- Automotive Components: Cam milling is frequently used to create camshaft profiles in the automotive industry, where precise timing is essential for engine performance.
- Industrial Equipment: It is used in the production of equipment that requires specific motion profiles, such as in presses, levers, and linkages.
- Gears and Sprockets: Cam milling is also utilized to create gears and sprockets that require a specific tooth shape for smooth operation.
These milling operations, each with its own advantages and limitations, are applied in different industries depending on the required precision, material type, and production volume. By choosing the appropriate milling operation, manufacturers can optimize their production processes, achieve desired part specifications, and reduce overall production costs.
Milling Operations Based on Milling Mechanisms
Milling is a machining process that uses rotating cutting tools to remove material from a workpiece. Depending on the milling mechanism, operations can vary significantly in terms of speed, precision, and material removal efficiency. There are several types of milling operations based on different mechanisms, including manual milling, CNC milling, and up-cut/down-cut milling. Each of these mechanisms has its own set of advantages, limitations, and applications, making them suitable for specific projects.
Manual Milling
Manual milling involves the use of a traditional milling machine where the operator manually controls the movement of the workpiece and the cutting tool. This type of milling typically uses a hand-cranked mechanism to move the table and cutter, offering operators direct control over the operation.
Advantages:
- Low Setup Cost: Manual milling machines are typically less expensive to purchase and set up compared to CNC machines.
- Flexibility: Operators have complete control over the operation, which allows for flexibility when making adjustments during machining.
- Simplicity: Ideal for small batches, prototype machining, or one-off projects where complex setups or high-speed automation aren't required.
Disadvantages:
- Labor-Intensive: Manual operation requires more time and effort, reducing production efficiency, especially for larger batches.
- Limited Precision: Precision is largely dependent on the skill of the operator, which can lead to variations in part quality.
- Slower Speeds: Manual machines are slower than automated CNC machines, making them less suitable for mass production.
Applications:
- Ideal for prototyping, low-volume production, or applications that do not require extremely high precision.
- Commonly used in educational environments or smaller workshops for parts like brackets, housings, and fixtures.
CNC Milling
Computer Numerical Control (CNC) milling uses a computer program to control the movement of the milling machine's tool and workpiece. CNC milling is highly automated and offers more precision, flexibility, and speed compared to manual milling. The use of digital control ensures high repeatability and complex part geometries that would be difficult to achieve manually.
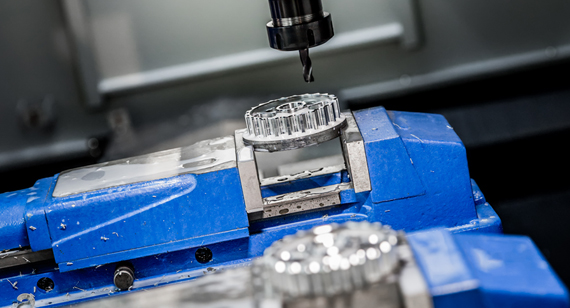
Advantages:
- High Precision and Accuracy: CNC milling offers a higher degree of precision, which is essential for producing intricate designs and tight tolerances.
- Automation: CNC machines can operate continuously with minimal human intervention, leading to higher productivity and consistency.
- Complex Geometries: Capable of performing complex cuts, angles, and shapes that manual milling cannot achieve efficiently.
Disadvantages:
- High Setup and Operational Cost: CNC machines are more expensive, both in terms of initial purchase cost and the need for skilled operators and ongoing maintenance.
- Programming Time: Although the machines are automated, the programming of complex jobs can take significant time and expertise.
Applications:
- Ideal for high-volume production, precision manufacturing, and complex designs.
- Used in industries such as automotive, aerospace, medical device manufacturing, and custom machining for intricate parts and high-precision components.
Up-Cut and Down-Cut Milling
In milling operations, the direction of the cutting tool relative to the workpiece can significantly affect the surface finish, material removal rate, and tool wear. There are two main types of cutting mechanisms: up-cut milling and down-cut milling. Both have distinct advantages and are suited for specific applications.
Up-Cut Milling:
In up-cut milling, the cutting tool rotates in a direction opposite to the feed direction of the workpiece. The cutting edges lift the material from the surface, creating a small chip that gradually becomes larger.
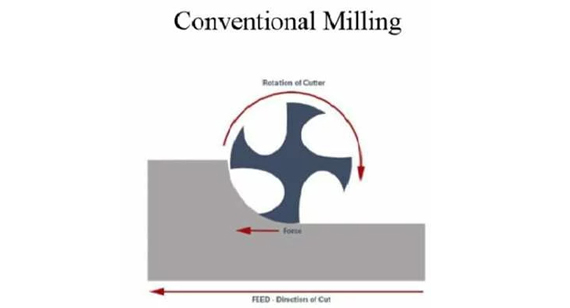
Advantages:
- Produces a smoother surface finish on the workpiece.
- Helps in reducing tool wear due to the gradual removal of material.
Disadvantages:
- More difficult to control, particularly for materials that are prone to being pushed away by the cutting tool.
- Can cause greater tool deflection when machining tough materials.
Applications:
- Commonly used in applications where a smoother surface finish is desired, such as finishing cuts or light machining on softer materials.
Down-Cut Milling:
In down-cut milling, the cutting tool rotates in the same direction as the feed of the workpiece, causing the cutting edges to push the material downwards into the machine table.
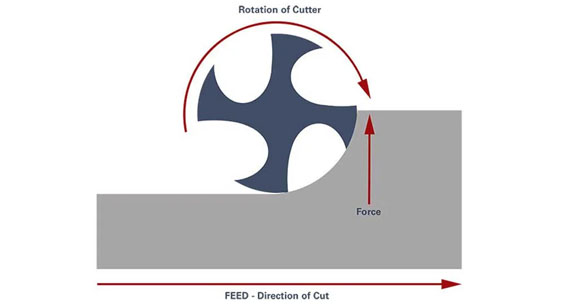
Advantages:
- Provides a better finish on the top side of the workpiece, as the tool forces the material downwards.
- Minimizes the risk of material tearing or chipping, especially on thin or brittle materials.
Disadvantages:
- Increases the wear on the tool since the material is pushed directly into the cutter, leading to higher forces and potential overheating.
- Less effective in removing chips from the cutting area, which can lead to higher tool temperatures and potentially increased tool wear.
Applications:
- Ideal for operations where a clean, precise surface is essential, especially for delicate workpieces or materials that are more sensitive to force, like plastics or composites.
Conclusion
Each milling operation, whether manual or CNC-based, has distinct advantages and limitations that make it suitable for different types of projects. Selecting the right type of milling operation depends on factors such as material, part complexity, precision, and production volume. By understanding these differences, manufacturers can optimize their processes for efficiency, cost-effectiveness, and high-quality results. Whether opting for traditional methods like turning and milling or non-traditional options like EDM and laser machining, understanding these processes helps make informed decisions for successful machining projects.
Here’s a clear comparison between Reverse Milling and Forward Milling presented in a table format to highlight the differences:
Criteria
|
Reverse Milling
|
Forward Milling
|
Cutting Direction |
The cutting tool rotates opposite to the direction of the feed. |
The cutting tool rotates in the same direction as the feed. |
Material Removal |
Chips are removed from the material in smaller increments, starting at the surface. |
Chips are removed in larger increments, beginning from the deeper part of the material. |
Surface Finish |
Results in a rougher surface finish. |
Produces a smoother surface finish. |
Tool Wear |
Increases tool wear due to the sudden engagement with the material. |
Less tool wear as the cutter enters gradually. |
Machine Deflection |
Causes more machine deflection due to the force exerted on the cutter. |
Less machine deflection, as the cutter is engaged more evenly. |
Feed Direction |
The material is fed against the direction of the cutter's rotation. |
The material is fed in the same direction as the cutter's rotation. |
Applications |
Suitable for finish cuts or softer materials. |
Better for rough cuts or harder materials. |
Cutting Forces |
Higher cutting forces, which may cause tool chatter. |
Lower cutting forces, reducing chatter. |
Chip Removal |
Chips are pushed away from the cutting area but may clog more easily. |
Chips are pushed away from the workpiece more easily. |
Use in Milling Machines |
Primarily used for finishing operations and for materials that can be cut easily. |
Commonly used for roughing operations where rapid material removal is necessary. |
This table gives a detailed comparison between reverse milling and forward milling, allowing you to understand which method would be best suited for your machining needs based on the material, cutting forces, surface finish requirements, and other factors.
Comparison Between Conventional Milling and Downcut Milling
Here is a clear comparison of Conventional Milling and Downcut Milling in a structured format:
Criteria
|
Conventional Milling
|
Downcut Milling
|
Surface Preparation |
The surface finish can be rougher since the cutting forces work in a way that can cause a more jagged surface. |
Produces a cleaner and smoother surface due to the cutting force pushing the tool downward. |
Tool Wear |
Increased tool wear as the cutting force is directed upward, causing more stress on the tool. |
Less tool wear, as the cutting force is directed downwards, reducing pressure on the tool. |
Material Removal |
Material removal occurs with the tool moving against the direction of the feed, leading to potentially higher cutting forces and rougher material removal. |
Material removal is smoother, with the tool moving in the same direction as the feed, leading to lower cutting forces. |
Material |
Suitable for harder materials that require more controlled removal. |
Better suited for softer materials or when a smoother finish is desired. |
Conventional Milling and Downcut Milling have different advantages depending on the machining requirements. Conventional milling is ideal for applications where material needs to be removed more aggressively, while downcut milling is better for smoother finishes and materials that can be cut with less force.
How to Choose the Right Milling Operation?
When choosing the appropriate milling operation for a project, several factors need to be taken into account to ensure optimal results. These factors include material type, surface finish, and the required roughness value. Let’s break down these factors to help make an informed decision on which milling operation is best suited for your needs.
Material Type
Material type is a critical factor in determining which milling operation to choose. For example, harder materials like titanium and stainless steel may require different cutting tools and operations compared to softer materials like aluminum. Each milling operation has its own set of parameters that will work better with specific materials.
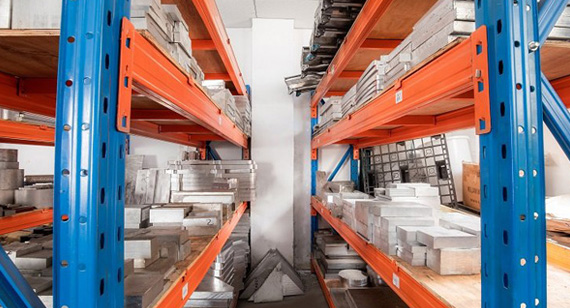
Surface Finish
Surface finish is essential when deciding on a milling operation. A smoother surface finish may be required for aesthetic or functional reasons, such as in aerospace or medical components. Some milling operations, like Face Milling, will provide a smoother finish than others, such as Slot Milling, which typically leaves a rougher surface.
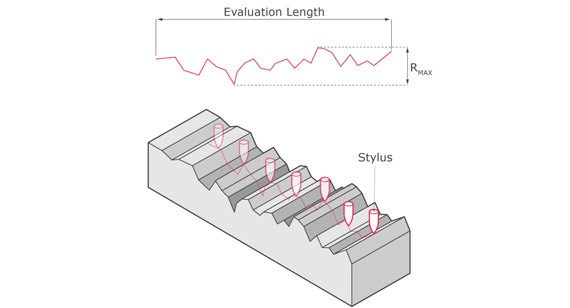
Face Milling
Roughness Ra Value (μm): Face milling is typically used for machining flat surfaces or removing material from large surfaces. The Ra value for face milling can range from 1 to 3 μm for fine finishes, depending on the tool and cutting conditions.
End Milling
Roughness Ra Value (μm): End milling can be used for making cuts along a part’s length, typically creating slots or pockets. This operation can achieve a surface finish with an Ra value around 1 to 2 μm.
Slot Milling
Roughness Ra Value (μm): Slot milling is often used for cutting grooves or channels. This operation can have a surface finish around 1 to 5 μm, depending on the tool size, speed, and feed rate.
Thread Milling
Roughness Ra Value (μm): Thread milling is commonly used for producing internal and external threads. The surface roughness can vary depending on the pitch and depth of the threads, but typically it ranges from 2 to 4 μm for most applications.
Gear Milling
Roughness Ra Value (μm): Gear milling is used for cutting gears, sprockets, or other toothed components. The required surface finish typically ranges from 2 to 6 μm for effective operation, depending on the precision needed for the gear teeth.
By considering material type, surface finish, and roughness Ra values, manufacturers can determine the best milling operation to achieve the required product quality efficiently and cost-effectively.
Here’s a table summarizing the different milling operations, their roughness Ra values, and how they relate to the material types and surface finishes:
Milling Operation
|
Roughness Ra Value (μm)
|
Material Type
|
Surface Finish
|
Applications
|
Face Milling |
1 - 3 μm |
Aluminum, Stainless Steel, Steel |
Fine |
Used for machining flat surfaces, removing material from large surfaces. |
End Milling |
1 - 2 μm |
Various materials (aluminum, steel, titanium) |
Fine to medium |
Ideal for making cuts along a part’s length, such as slots or pockets. |
Slot Milling |
1 - 5 μm |
Aluminum, Stainless Steel, Steel |
Medium to rough |
Used for cutting grooves, channels, or slots. |
Thread Milling |
2 - 4 μm |
Steel, Stainless Steel |
Fine to medium |
Produces internal or external threads, with higher precision in thread profiles. |
Gear Milling |
2 - 6 μm |
Steel, Aluminum, Stainless Steel |
Medium to rough |
Cuts gears, sprockets, or other toothed components. |
Drilling |
1 - 5 μm |
Steel, Aluminum, Plastic |
Rough to medium |
Used for creating round holes, typically using a rotating drill bit. |
Grinding |
0.1 - 1 μm |
Steel, Stainless Steel, Ceramic |
Very fine |
Used for finishing and polishing surfaces, offering a high level of precision. |
Sawing |
3 - 10 μm |
Aluminum, Steel, Brass |
Rough |
Cuts through materials to shape parts, typically with a saw blade. |
Broaching |
0.5 - 2 μm |
Steel, Cast Iron |
Fine to medium |
Cuts complex shapes or keyways into a part using a broach. |
Planing |
1 - 5 μm |
Steel, Aluminum |
Medium to rough |
Removes large amounts of material to create a smooth flat surface. |
This table provides a quick comparison of common milling operations based on their surface finish (Ra value), material compatibility, and specific applications.
Geometric Complexity
When selecting the right milling operation, the complexity of the geometry plays a crucial role. Simple geometries like flat surfaces and basic slots can be effectively handled by traditional milling operations like face milling and end milling. However, more intricate shapes, such as those with tight radii or complex contours, may require specialized operations such as contour milling or 3D milling. The ability of the machine and the tooling involved to handle complex geometries without compromising accuracy is essential for achieving the desired design outcome.
Tolerance Requirements
Milling operations often involve high precision. The tighter the tolerance requirements, the more specific the choice of operation becomes. For parts that require tight tolerances, precision milling operations like micro milling, CNC milling, or grinding are suitable. These methods provide better control over the finished dimensions, ensuring the components meet the desired specifications. In cases where loose tolerances are acceptable, simpler operations like traditional milling or sawing can be used.
Considering Machine Parameters and Settings
The settings and capabilities of the milling machine will influence the quality and efficiency of the operation. Parameters such as feed rate, cutting speed, tool type, and cutting depth must be optimized based on the material, the type of operation, and the desired outcome. Machine tools with better precision and advanced features (like CNC machines) allow for more intricate and complex operations. Understanding machine parameters helps operators optimize their setups for efficiency and high-quality output.
Production Volume
The volume of parts needed for the project is another critical factor in choosing the right milling operation. For large-scale production runs, automated CNC milling or high-speed machining operations are more efficient and cost-effective. These processes offer repeatability and high productivity for bulk production. On the other hand, low-volume or custom parts may benefit from manual or smaller-scale operations, which may be more flexible and cost-effective when fewer units are required.
Choosing the Right Tool for Different Milling Operations
The choice of tooling depends on the material being machined, the operation type, and the desired outcome. For rough cutting, larger, more robust cutting tools are used, while finer, smaller tools are needed for precision and finishing operations. Carbide tools, for example, are typically used for harder materials, while high-speed steel tools are often sufficient for softer materials. Choosing the right tool ensures high performance, longevity, and minimal tool wear, leading to better overall machining results.
Cost Considerations
Cost is always a major factor in selecting the right milling operation. Precision operations or those requiring high-quality finishes may have higher setup and tooling costs but provide superior results. For larger production volumes, automated CNC machining can reduce labor costs and increase throughput, making it more cost-effective despite the higher initial investment. In contrast, simpler operations like manual milling may be more economical for small runs, but they may lack the precision and repeatability of automated processes.
Available Machine Tools and Technologies
The available machinery in the shop will also influence the choice of milling operation. Advanced CNC machines with multi-axis capabilities offer more flexibility and precision, enabling complex operations like 5-axis milling or multi-material machining. In contrast, older or less advanced equipment may limit the types of operations that can be performed effectively. Availability of machine tools and technologies determines the ability to meet both design specifications and production timelines efficiently.
Tool Availability and Compatibility
Tool availability and compatibility with the milling machine are also essential factors in the decision-making process. Different machines require different tool types and sizes. For example, CNC machines may require specific types of cutting tools, tool holders, and adapters that are not compatible with manual mills. The availability of the right tools also affects the lead time and cost of production, as sourcing specialty tools may delay the project and increase the overall cost.
Operator Skill Level
The skill level of the operator is another consideration in selecting the appropriate milling operation. CNC machining requires skilled operators who are proficient in programming and machine setup. On the other hand, manual milling machines can be operated by less experienced individuals, although this may sacrifice some precision and efficiency. Highly skilled operators can also optimize settings to achieve better results and handle more complex jobs, making their experience an important factor in selecting the right operation.
Safety Requirements
Safety is paramount in all manufacturing processes. Milling operations that involve high-speed rotation or cutting tools may present risks such as flying debris, sharp edges, or heat buildup. Safety features like machine guards, emergency shutoff switches, and proper tooling setups help minimize these risks. The operation must comply with safety regulations to protect operators and minimize the risk of injury or accidents. Ensuring the right milling operation is selected based on safety requirements helps prevent accidents and promotes a safer working environment.
Milling Operation Applications
Milling operations are used across a wide range of industries and applications. For example, in the automotive industry, milling is used to produce engine components, gears, and chassis parts. In aerospace, precision milling is crucial for manufacturing aircraft components that require high levels of accuracy. Medical industries rely on milling for making intricate medical devices and implants, while the electronics sector uses milling to manufacture components like housings and connectors. Choosing the right milling operation ensures the right balance of performance, cost, and precision for the specific application.
In conclusion, choosing the correct milling operation depends on several factors, including material type, required tolerances, production volume, cost, and safety. An understanding of these considerations allows manufacturers to select the optimal operation for their needs, ensuring high-quality results while meeting time and cost constraints.
Summary: Milling Operation: Understanding the Process, Type, Diagram, and Application
Milling is a critical machining operation used to remove material from a workpiece using rotary cutters. It plays an essential role in various industries due to its versatility and precision. CNC milling machines are commonly employed for their ability to automate the milling process, increasing efficiency and reducing human error.
There are several types of milling operations, including face milling, slot milling, end milling, and more, each with its unique set of advantages, disadvantages, and applications. Face milling, for instance, is ideal for large, flat surfaces, while slot milling is used to cut narrow slots or grooves. End milling is effective for making precise cuts, while thread milling is used for producing threaded holes.
When selecting the right milling operation, factors such as material type, surface finish requirements, tool availability, and machine parameters must be considered. CNC machining offers high precision and repeatability, making it suitable for producing complex parts in large quantities, while manual milling can be ideal for smaller runs and custom pieces.
The milling process also includes various mechanisms such as up-cut and down-cut milling, each affecting surface quality, material removal, and tool wear differently. Operators must choose the appropriate milling method based on the desired outcome, material, and complexity of the part being machined.
Additionally, non-traditional milling techniques, like laser and water jet machining, offer unique advantages for specific applications that require high precision, minimal thermal impact, or the ability to cut through hard materials. Understanding these methods is essential for selecting the most suitable process based on the project’s needs.
Ultimately, milling operations are essential in manufacturing parts with high precision, diverse shapes, and complex geometries. With the right combination of milling type, machine, and tools, manufacturers can optimize production processes and deliver high-quality results.
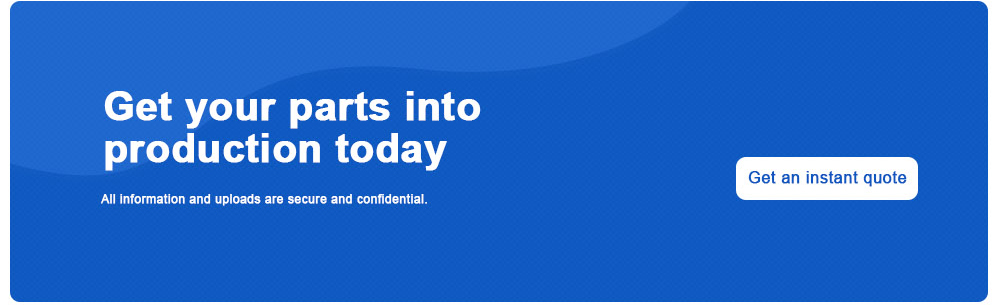
Milling Operation FAQs
What are the basic types of milling machines?
The basic types of milling machines are vertical, horizontal, and CNC (computer numerical control) milling machines. Vertical milling machines have a vertically oriented spindle, whereas horizontal milling machines have a horizontally positioned spindle. CNC milling machines are automated and controlled via computer programming, enabling high precision and repeatability.
Which milling operation achieves the highest precision?
End milling and slot milling are among the milling operations that offer the highest precision. These methods provide tight tolerances and are used for producing intricate, detailed cuts on small parts or precision components.
Which type of milling operation is the most expensive?
Gear milling tends to be one of the most expensive milling operations due to the specialized tools and complex setup required to produce gears with high accuracy and surface finishes.
Which type of milling operation is the most cost-effective? Face milling is generally the most cost-effective milling operation for producing large flat surfaces. This method is widely used in mass production due to its simplicity and effectiveness in removing material from large surfaces quickly.
What is the most common milling operation?
Face milling is the most common milling operation, as it is used for producing flat surfaces on workpieces. It is versatile and effective in a variety of industries, such as automotive, aerospace, and manufacturing.
What is the most popular milling technology?
CNC milling technology is the most popular milling technology. CNC milling machines are automated, controlled via computer programs, and offer high precision, repeatability, and efficiency in producing complex parts.
What is the most accurate milling operation?
End milling is typically the most accurate milling operation. It is used for producing complex shapes, contours, and precise features in high-accuracy applications, such as medical devices, aerospace parts, and electronic components.
What is the cheapest milling operation?
Face milling is one of the most cost-effective milling operations, as it is quick and suitable for mass production. It is commonly used for creating flat surfaces and is efficient for high-volume production runs.
What is the most expensive milling operation?
Gear milling is often one of the most expensive due to the complexity of cutting gears, the specialized tools involved, and the precision required in producing gears for high-performance applications.
What is the oldest industrial milling technology?
Manual milling machines are among the oldest milling technologies. These machines have been used since the early 19th century, and while modern CNC machines have replaced many manual operations, manual milling remains valuable for custom and low-volume production.
What are the three basic forms of milling processes?
The three basic forms of milling processes are face milling, slab milling, and end milling. These cover a range of operations, from creating flat surfaces to cutting detailed features and shapes.
What is the best milling process?
The "best" milling process depends on the specific requirements of the project. CNC milling is often considered the best for producing complex, high-precision parts with tight tolerances. For large surface finishes, face milling might be the best choice.
What is a contour milling operation?
Contour milling involves cutting along the contour or perimeter of a workpiece. It is often used for creating curved shapes or detailed surfaces and is commonly applied in the production of molds and toolpaths.
What are the 7 lathe operations?
The seven common lathe operations are turning, boring, drilling, facing, knurling, parting, and thread cutting. These operations are used for shaping and finishing cylindrical or spherical parts.
What are the four processes of machining?
The four main processes of machining are cutting, grinding, milling, and turning. Each process is used to remove material and achieve specific shapes or features.
What are the six basic machines?
The six basic machines in machining are lathe, milling machine, grinder, drilling machine, shaper, and saw. These machines are used for various operations such as cutting, shaping, grinding, and drilling parts to meet specific requirements.