Introduction to Gear Manufacturing
Gear manufacturing is an essential aspect of many industries, from automotive to aerospace, and even small appliances. Gears are mechanical components that transmit torque and motion between machine parts, often converting speed or direction to optimize machine function. Without gears, many of the systems we rely on would simply not work—imagine your car’s transmission, an industrial conveyor, or the mechanisms inside a clock.
The production process for gears starts with a design, where engineers determine the gear’s size, type, and material. This is followed by selecting the appropriate manufacturing process, such as cutting, milling, or grinding, to create the gear. Once produced, gears undergo rigorous quality control to ensure that they meet the necessary specifications and perform reliably over their lifespan.
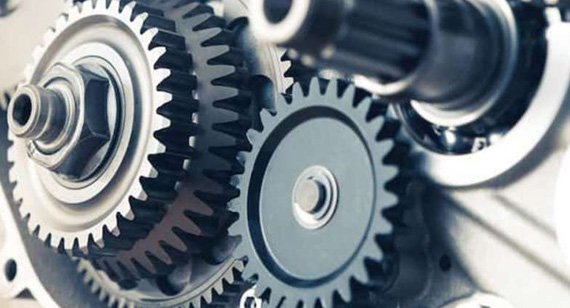
There are several types of gears, each with specific characteristics that make them suitable for particular applications. Here are the most common ones:
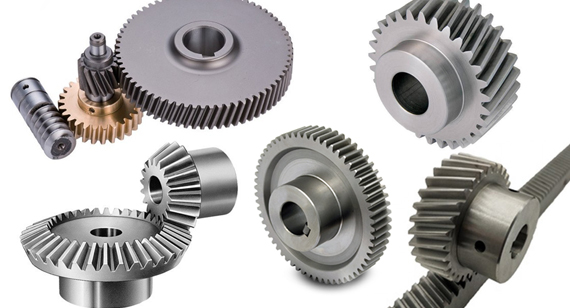
- Spur Gears: The simplest and most widely used type of gear, spur gears have straight teeth that align parallel to the axis of rotation. They are ideal for applications where high efficiency and speed are essential, such as in gearboxes or conveyor systems. However, they can be noisy and less efficient at high speeds due to their tooth alignment.
- Helical Gears: These gears have teeth set at an angle, which allows for smoother engagement between teeth compared to spur gears. This results in quieter operation, greater load capacity, and better efficiency, especially at high speeds. They’re commonly used in automotive transmissions and heavy machinery.
- Bevel Gears: Bevel gears are used to transmit power between two shafts that are set at an angle to each other, usually 90 degrees. Their teeth are cone-shaped, making them perfect for applications where the direction of the drive needs to be changed, such as in differentials in cars.
- Worm Gears: A worm gear consists of a worm (a gear in the form of a screw) meshing with a gear wheel. This design allows for high gear reduction ratios and is often used in applications where space is limited, such as in winches and conveyors. They are also useful when non-backdriving is required, meaning the gears won’t rotate unless actively powered.
Each type of gear offers distinct advantages, so understanding their characteristics helps manufacturers choose the best option for a given application.
Materials Used in Gear Manufacturing
The material chosen for gear manufacturing plays a major role in the gear’s performance and durability. Here are some common materials used:
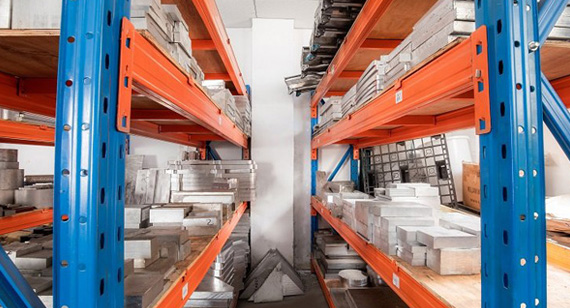
- Steel: Steel is the most common material for gears due to its strength and resistance to wear. There are different grades of steel used for gears, including carbon steel, alloy steel, and stainless steel. Each type provides varying levels of strength, durability, and corrosion resistance.
- Cast Iron: Cast iron is often used for large gears that don’t require as much strength but need to be heavy and durable. It's commonly found in industrial machines, such as gearboxes and conveyors, where weight and rigid construction are essential.
- Bronze: Bronze gears offer excellent corrosion resistance and wear properties, making them ideal for marine environments or machinery exposed to harsh conditions. They’re also useful in applications where self-lubrication properties are desired.
- Aluminum: Lightweight gears are often made from aluminum, especially in applications where reducing weight is important, such as in aerospace or consumer electronics.
- Composites and Plastics: For smaller, lighter gears that won’t experience heavy loads, composites and plastic materials are used. These materials are cost-effective and often found in products like office equipment, small appliances, and hobbyist tools.
The material choice depends on the specific requirements of the application, such as load, speed, and environmental conditions, and influences the gear's lifespan and efficiency.
Gear Manufacturing Processes
The manufacturing process used depends on the type of gear, the material, and the desired level of precision. Some of the most common processes are:
- CNC Cutting: This is the primary process for creating the basic shape of a gear. For spur gears, hobbing (a type of cutting process) is commonly used. For helical gears, gear cutting techniques such as shaving or broaching are used to achieve the right tooth profile.
- CNC Milling: Milling is used to create more intricate shapes and fine details on gears. This method is ideal for producing gears with specific tooth profiles, like those required in bevel or worm gears.
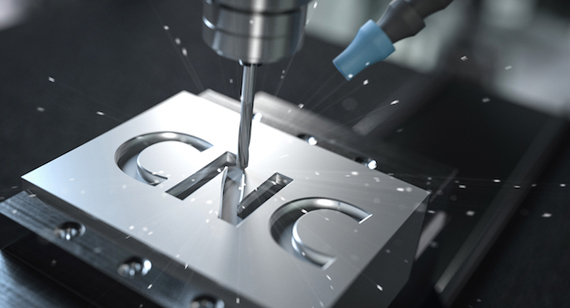
- CNC Grinding: Grinding is often used for high-precision gears that must meet strict tolerance levels, such as those used in automotive and aerospace applications. It ensures that gear teeth are smooth, uniform, and accurately shaped.
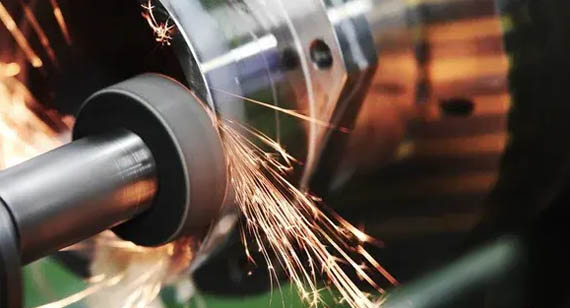
- Casting: Large gears or those made from materials like cast iron are often produced via casting. This method involves pouring molten material into a mold to form the desired gear shape, which is then refined through machining.
Each manufacturing process has its strengths and limitations. For example, cutting and milling are fast and cost-effective for mass production, while grinding offers the precision necessary for high-performance applications but is slower and more expensive.
Quality control is critical in gear manufacturing, as even a small defect can lead to failures or inefficiency. Several methods are employed to ensure high-quality gears:
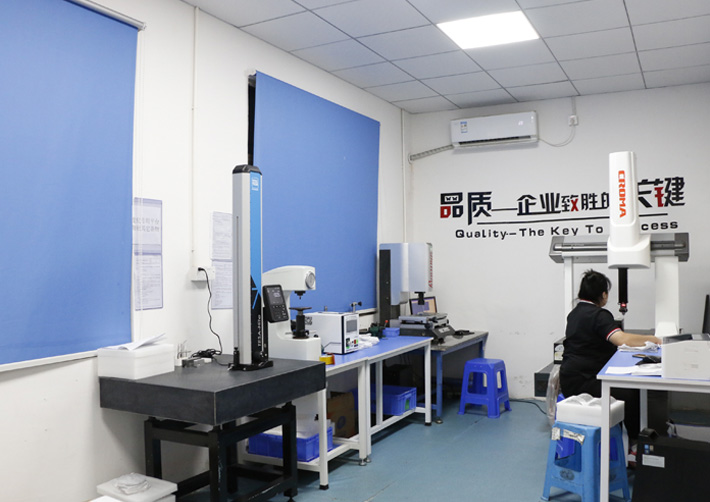
- Dimensional Inspection: This involves measuring the gear to ensure it meets the specified dimensions. Accuracy in tooth size, pitch, and profile is crucial to ensure smooth meshing with other gears.
- Tooth Profile Testing: Special tools are used to inspect the shape and alignment of the teeth, which must mesh perfectly with other gears. Errors here can lead to noise, increased wear, and eventual gear failure.
- Load Testing: Gears are subjected to load tests to ensure they can handle the stresses they’ll face in operation. This includes simulating the actual working conditions to see if the gear can perform without failure.
- Noise and Vibration Testing: Particularly important for gears used in high-speed machinery, noise and vibration tests ensure that the gear operates smoothly and quietly.
By closely monitoring each stage of production and performing thorough testing, manufacturers can ensure that their gears perform reliably over their lifespan.
Customization in Gear Manufacturing
Customization in gear manufacturing is key when gears need to meet specific requirements. Many industries require gears tailored to unique conditions, such as special sizes, materials, tooth profiles, or load-bearing capacities. Here’s how gears can be customized:
- Size and Shape: Gears can be produced in virtually any size, from tiny components in consumer electronics to large gears used in heavy machinery. Customizing the shape allows gears to fit perfectly into their intended applications.
- Tooth Profile: Custom gears can be made with specialized tooth profiles, like helical, bevel, or spiral, depending on the application. This customization ensures that the gears perform efficiently and with minimal noise and vibration.
- Material Selection: Custom gears can be made from a wide range of materials, depending on the environment and load conditions. For example, gears used in marine environments may require corrosion-resistant materials like bronze.
Custom manufacturing ensures that gears operate optimally for their intended applications, providing better efficiency, less wear, and greater reliability.
Advancements in Gear Manufacturing Technology
Technology is transforming gear manufacturing, making it more efficient and precise. Some of the latest advancements include:
- Computer-Aided Design (CAD): CAD software allows manufacturers to design gears with high precision, optimizing tooth profiles and overall design before production. This reduces errors and speeds up the design-to-production process.
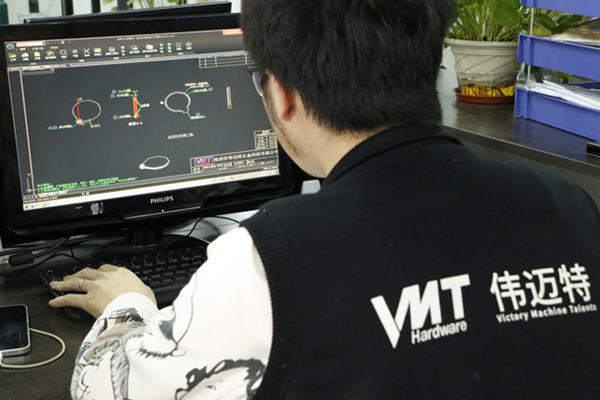
- Computer-Aided Manufacturing (CAM): CAM integrates design and manufacturing processes, making gear production faster and more automated. By using CAM, manufacturers can reduce human error and improve production efficiency.
- Additive Manufacturing (3D Printing): 3D printing is emerging as a method for producing prototype gears or small-batch runs. It allows for rapid prototyping and customization, particularly useful for industries like aerospace and automotive, where complex shapes and low production volumes are common.
These technological advancements make it possible to produce high-quality, precise gears faster and more cost-effectively, driving innovation in gear manufacturing.
Gear Maintenance and Repair
Proper maintenance ensures that gears perform well throughout their lifespan. Regular maintenance helps prevent premature failure and reduces downtime. Here are some tips for gear maintenance:
- Lubrication: Keep gears well-lubricated to reduce friction and prevent excessive wear. Regularly check the lubrication levels and replace the oil or grease as needed.
- Inspection: Regularly inspect gears for signs of wear, cracks, or damage. Catching problems early can prevent bigger issues down the line.
- Cleaning: Dirt and debris can cause gears to wear down prematurely. Make sure gears are cleaned regularly to prevent buildup that could damage the teeth.
- Repairs: If a gear's teeth become worn or damaged, it may need to be re-shaped or replaced. In some cases, gears can be resurfaced or reconditioned to extend their useful life.
Cost Considerations in Gear Manufacturing
The cost of gear manufacturing varies depending on several factors:
- Materials: High-quality metals or specialty alloys can increase the cost of production. Opting for more affordable materials might reduce upfront costs but could result in a shorter lifespan or less reliability.
- Labor: Skilled labor is often required for precision machining and quality control. Labor costs can fluctuate depending on the complexity of the gear and the manufacturing process.
- Equipment: The cost of machinery, such as CNC machines and grinding tools, can be significant. However, investing in modern equipment can lead to more efficient production and better quality control.
Manufacturers can optimize costs by choosing the right materials, streamlining production processes, and ensuring high levels of efficiency without sacrificing quality.
Future Trends in Gear Manufacturing
As technology advances, gear manufacturing is set to evolve in exciting ways:
- New Materials: Research into new, lightweight, and durable materials will likely lead to even more efficient gears with longer lifespans.
- Smart Gears: The integration of sensors and monitoring systems into gears will allow for real-time data collection and predictive maintenance, improving gear performance and reducing the risk of failure.
- Sustainability: More emphasis will be placed on sustainable manufacturing practices, including the use of recyclable materials and energy-efficient production methods.
As industries demand greater precision, efficiency, and sustainability, gear manufacturing will continue to innovate, bringing more advanced solutions to meet these needs.
By understanding the manufacturing processes, types, materials, and technological advancements in gear production, industries can better meet their specific needs, improve performance, and reduce costs. Whether you're designing gears for heavy machinery, automotive systems, or consumer electronics, the insights shared here can help guide your choices in gear production and selection.
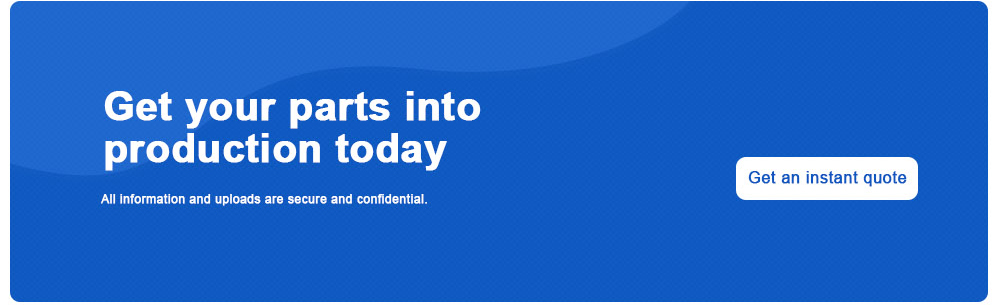
Frequently Asked Questions (FAQs) About Gears:
What is the difference between spur gears and helical gears?
Spur gears have straight teeth and are used in applications where high speed and efficiency are required. Helical gears have angled teeth and offer smoother operation, reduced noise, and increased load capacity.
How are gears made?
Gears are typically made through a combination of machining processes, such as cutting, milling, and grinding. The specific process depends on the type of gear, the material, and the desired accuracy and quality.
What materials are best for gear manufacturing?
The choice of material depends on the application and requirements of the gear. Common materials include steel, aluminum, brass, and bronze. High-performance gears may use specialized alloys or composites.
How important is quality control in gear manufacturing?
Quality control is crucial in gear manufacturing to ensure that the gears meet the specified standards and perform reliably in the intended application. It involves inspection, testing, and monitoring of the manufacturing process to identify and address any issues.
Can gears be customized?
Yes, gears can be customized to meet specific requirements, such as size, shape, tooth profile, and material. Customization allows for optimal performance and compatibility in unique applications.